行业知识
氧化锆球的滚制成型法制备技术与性能研究
作者:admin日期:2020-01-04阅读
研究了滚制成型法制备氧化锆球坯工艺及烧结温度对陶瓷磨球体积密度、压碎强度和自磨损性能的影响。结果表明:凝胶固相合成法生产的亚微米级3mol%Y2O3-ZrO2陶瓷粉体适用于滚制成型法制备体积密度高、圆度好、大小均匀的球坯。
在1500℃保温2h的烧结条件下得到的微晶氧化锆球在快速研磨机中的自磨损率,其微观结构均匀,晶粒尺寸约0.5μm,体积密度为5.97g/cm3,Υ2.75mm和Υ6.36mm陶瓷磨球的平均压碎强度分别达到326kg和1377kg。
氧化锆球是氧化锆材料中一类用量很大、应用面很广的产品,除了在氧化锆类陶瓷粉体研磨中大量使用外,在其它电子陶瓷粉料,磁性材料粉料、高技术结构和功能陶瓷粉料、日用陶瓷色料和釉料,化工和各类涂料,机械抛光用粉料,医药和食品粉剂的超细研磨中也发挥了为重要的作用。
目前,氧化锆球多用3mol%Y2O3部分稳定的ZrO2材料体系制备[1],与大量使用的氧化铝陶瓷磨球相比,氧化锆陶瓷比重可达6.0g/cm3左右,因此冲击力大,在同样条件下,可减少所需的研磨时间,提高研磨效率[2];其次,氧化锆陶瓷与氧化铝陶瓷的硬度相近,约为12~14GPa,但强度高达800~1000MPa,断裂韧性可达10MPa·m1/2以上,均为氧化铝陶瓷的二到三倍。因此其磨耗很,压碎强度很高,可以显著减少被研磨物料中杂质引入,同时在一些特殊的超细粉体研磨设备如搅拌磨机、砂磨机、高速振动磨机等新型设备中,不易破碎的高强高韧微晶氧化锆球已成为可用的产品,尽管微晶氧化锆磨球价格高,但由于其磨耗,对被研磨物料的研磨和分散效果好,无需时常补加料,因此综合使用成本仍相对较。其使用领域不断扩大,正在逐渐代替氧化铝、硅酸锆、玛瑙等研磨介质球。
通常,高质量的微晶氧化锆磨球多采用氧化钇部分稳定的氧化锆(Y-TZP)超细粉体为原料成型后经高温烧结(1400~1600℃)致密化,然后通过自磨或添加超细研磨粉料抛光得到。球粒尺寸根据使用要求不同,包括了从Υ0.1mm以上各种级别。对于大尺寸磨球,多采用冷等静压成型工艺,即先将粉体料浆喷雾造粒,然后装入特殊设计的硬橡胶模袋中进行冷等静处理获得球坯。该工艺所得坯体致密度高,烧结成瓷材质好,密度高。但由于模具限制,其球坯园度不好,表面形成的棱边需进一步打磨处理,同时,该工艺设备投资费用大,生产成本高,不适合于生产直径小于Υ10mm的小球。
国内生产氧化锆小球也有采用泥段滚制成型工艺,即先将粉体与水、粘接剂、增塑剂、润滑剂等加入练泥机混合练制成泥,经陈腐形成塑性泥料,放入挤泥机挤制成泥条,并切成长度与直径尺寸相当的泥段,再放入滚球机滚制成球坯。该工艺只要控制好挤泥机模头口径和切段长短,就可以得获到一致性较好的泥段,滚制的球坯园度也容易保证。但由于塑性泥料含水量和添加物较多,使球坯密度相对较,需提高烧结温度才能获得较致密瓷体,导致晶粒尺寸长大,难以获得微晶耐磨的效果。
粉体直接滚制法使用简单廉价的旋转滚球机,先加入预制的球坯晶种,然后边旋转喷水雾边添加陶瓷粉体,粉体不断粘附于晶种表面逐渐长大,终得到所需尺寸的球坯。目前,滚制成型法制备陶瓷小球技术在氧化铝陶瓷中已获得了比较广泛的应用[3]。该技术具有设备和生产工艺简化、生产效率高、产量好的优势,是一种适合于规模化大生产的工艺技术,但至今尚未见到用该工艺生产氧化锆球的报道。
3.2 烧结温度对氧化锆陶瓷磨球性能的影响在1500℃保温2h的烧结条件下得到的微晶氧化锆球在快速研磨机中的自磨损率,其微观结构均匀,晶粒尺寸约0.5μm,体积密度为5.97g/cm3,Υ2.75mm和Υ6.36mm陶瓷磨球的平均压碎强度分别达到326kg和1377kg。
氧化锆球是氧化锆材料中一类用量很大、应用面很广的产品,除了在氧化锆类陶瓷粉体研磨中大量使用外,在其它电子陶瓷粉料,磁性材料粉料、高技术结构和功能陶瓷粉料、日用陶瓷色料和釉料,化工和各类涂料,机械抛光用粉料,医药和食品粉剂的超细研磨中也发挥了为重要的作用。
目前,氧化锆球多用3mol%Y2O3部分稳定的ZrO2材料体系制备[1],与大量使用的氧化铝陶瓷磨球相比,氧化锆陶瓷比重可达6.0g/cm3左右,因此冲击力大,在同样条件下,可减少所需的研磨时间,提高研磨效率[2];其次,氧化锆陶瓷与氧化铝陶瓷的硬度相近,约为12~14GPa,但强度高达800~1000MPa,断裂韧性可达10MPa·m1/2以上,均为氧化铝陶瓷的二到三倍。因此其磨耗很,压碎强度很高,可以显著减少被研磨物料中杂质引入,同时在一些特殊的超细粉体研磨设备如搅拌磨机、砂磨机、高速振动磨机等新型设备中,不易破碎的高强高韧微晶氧化锆球已成为可用的产品,尽管微晶氧化锆磨球价格高,但由于其磨耗,对被研磨物料的研磨和分散效果好,无需时常补加料,因此综合使用成本仍相对较。其使用领域不断扩大,正在逐渐代替氧化铝、硅酸锆、玛瑙等研磨介质球。
通常,高质量的微晶氧化锆磨球多采用氧化钇部分稳定的氧化锆(Y-TZP)超细粉体为原料成型后经高温烧结(1400~1600℃)致密化,然后通过自磨或添加超细研磨粉料抛光得到。球粒尺寸根据使用要求不同,包括了从Υ0.1mm以上各种级别。对于大尺寸磨球,多采用冷等静压成型工艺,即先将粉体料浆喷雾造粒,然后装入特殊设计的硬橡胶模袋中进行冷等静处理获得球坯。该工艺所得坯体致密度高,烧结成瓷材质好,密度高。但由于模具限制,其球坯园度不好,表面形成的棱边需进一步打磨处理,同时,该工艺设备投资费用大,生产成本高,不适合于生产直径小于Υ10mm的小球。
国内生产氧化锆小球也有采用泥段滚制成型工艺,即先将粉体与水、粘接剂、增塑剂、润滑剂等加入练泥机混合练制成泥,经陈腐形成塑性泥料,放入挤泥机挤制成泥条,并切成长度与直径尺寸相当的泥段,再放入滚球机滚制成球坯。该工艺只要控制好挤泥机模头口径和切段长短,就可以得获到一致性较好的泥段,滚制的球坯园度也容易保证。但由于塑性泥料含水量和添加物较多,使球坯密度相对较,需提高烧结温度才能获得较致密瓷体,导致晶粒尺寸长大,难以获得微晶耐磨的效果。
粉体直接滚制法使用简单廉价的旋转滚球机,先加入预制的球坯晶种,然后边旋转喷水雾边添加陶瓷粉体,粉体不断粘附于晶种表面逐渐长大,终得到所需尺寸的球坯。目前,滚制成型法制备陶瓷小球技术在氧化铝陶瓷中已获得了比较广泛的应用[3]。该技术具有设备和生产工艺简化、生产效率高、产量好的优势,是一种适合于规模化大生产的工艺技术,但至今尚未见到用该工艺生产氧化锆球的报道。
实 验
2.1 氧化锆球坯的制备
采用某材料有限公司用凝胶固相合成法[4]和国内某企业用化学共沉淀法生产的两类3mol%Y2O3-ZrO2陶瓷粉体为原料,分别记为F1和F2。用滚制成型法制备氧化锆陶瓷磨球坯体,制备工艺为:冷等静压粉体坯料,破碎,过筛预制晶种,加入滚球机滚动,喷水雾,添加粉料,喷水雾,添加粉料······,滚动长大至预定尺寸(约Υ3.2mm和Υ7.3mm两种),滚动表面抛光※干燥※球坯。
2.2 氧化锆球坯的烧结工艺
将氧化锆球坯体分成三组装匣钵烧结,烧结工艺制度如下:室温至1000℃,升温速率为100℃/h;1000℃至烧成温度,升温速率为50℃/h,三组试样烧成温度分别定为1450℃、1500℃、1550℃,保温2h后随炉冷却,得到直径约Υ3mm和Υ6mm的氧化锆陶瓷磨球。
2.3氧化锆球性能测试方法
(1)体积密度测定:将烧结后氧化锆陶瓷磨球在万分之一精度天秤分别测定其干重和在水中的重量,用阿基米德法计算氧化锆陶瓷磨球的体积密度。
(2)自磨损率测定:把每组待测定的氧化锆陶瓷磨球称取1kg左右,记为m1(精确度0.01g,以下同),装入标称1L的球形氧化铝陶瓷罐,加入500mL去离子水,在快速研磨机(振磨机)上振磨5h,取出样品用水清洗干净,于80℃烘箱中烘干后称重,计为m2,自磨损率=1000(m1-m2)/5m1,单位为g/kg·h。
(3)压碎强度测定:在100kN材料试验机的上下压头处衬垫厚约10mm的氧化铝陶瓷板,将待测
氧化锆陶瓷磨球放置于其间,以0.5mm/min.的加载速率施加压力直至破碎,记录大压力定为陶瓷球压碎强度。对于每种球径,各测三个试样,取平均值做为平均压碎强度。
3.1 滚制成型氧化锆球坯对粉体特性的要求
3.1 滚制成型氧化锆球坯对粉体特性的要求
在喷雾水中加入0.3wt%PVA粘结剂,用凝胶固相合成法生产的氧化锆陶瓷粉体(F1),通过控制滚球机倾角与转速,喷水雾和加粉相对量及其时间间隔等参数,可获得圆度好、大小均匀的球坯,经测定其体积密度达到3.82g/cm3。而用共沉淀法生产的氧化锆陶瓷粉体(F2),在球坯滚制过程中向晶种上粘粉困难,需喷较多水雾,但又容易结团,造成球坯尺寸大小不均匀,密度达到3.27g/cm3,而且容易破碎,破碎断口明显有分层现象。图1为两类粉体的SEM图。从图中可以看出,F1是分散性良好的等轴球状颗粒,其晶粒均匀,原晶尺寸约为0.2μm左右,完整,这种粉体是经1300℃以上高温合成后经砂磨机粉碎得到,其比表面积不到8m2/g,因此用水量少,堆集紧密,所得球坯体积密度高。而F2粉体原晶尺寸细,不够充分,存在明显团聚情况,无法适用于滚制成球。本文用F2粉体滚制成型氧化锆球坯未能成功,而用F1粉体则没有什么困难。显然,以往认为氧化锆球难以滚制成型,其主要原因是对粉体的要求不清所致。由于目前国内市场主要销售的是共沉淀法制备的氧化锆粉体,其锻烧合成温度较(一般于1100℃),粉体过于膨松,比表面积很大,因此不适合于滚制成型法制备陶瓷球坯。
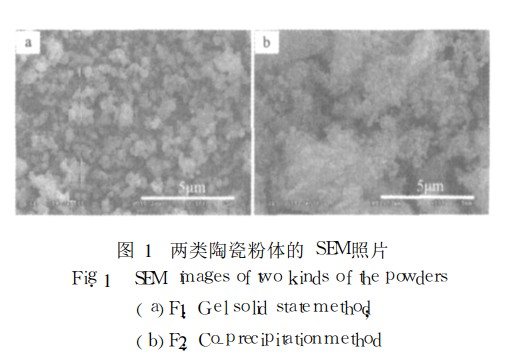
采用F1粉体滚制成型法制得的两种尺寸球坯体,按规定的烧结工艺制度烧成后,测得其体积密度和自磨损率与烧成温度的关系,同时测定了自磨损率的1500℃烧结陶瓷磨球的压碎强度,如表1所示。可以清楚地看到,F1粉体滚制成型球坯有很好的烧结性,在1450℃烧结后即达到约97%的相对密度(理论密度按6.10g/cm3计算)。随着烧结温度的提高,氧化锆磨球的体积密度逐渐,在1550℃烧结后达到约99%的相对密度。这表明F1是一种高烧结活性的亚微米级氧化锆粉体,同时证明滚制成型法可以制得高致密度的氧化锆磨球。
1500℃烧结的Υ2.75mm磨球的自磨损率为1.02g/kg·h,而且其平均压碎强度达到了326kg,超过了通常Υ3.0mm磨球压碎强度大于300kg的规定。在本试验条件下,磨球的自磨损率并不完全取决于其体积密度的高,而是以1500℃烧结后的氧化锆陶瓷磨球,且对于两种尺寸的磨球规律是一致的。图2是不同烧结温度磨球的断口微观形貌,可以看出,1450℃烧结后尚有少量微气孔,致密化程度较(图2a),故其耐磨性不如1500℃烧结者,说明瓷体密度是影响磨球自磨损率的重要因素之一;而1550℃烧结后,晶粒尺寸有异常长大现象(图2c),其自磨损率明显,以致超过1450℃烧结者,说明晶粒尺寸对磨球自磨损率的影响更大;1500℃烧结后,瓷体在具有较高致密度的同时并保持了均匀细小的晶粒(图2b),故获得了的自磨损率。因此,对于氧化锆研磨介质球而言,更需强调其微晶结构的重要性。
另一值得注意的问题是,在本试验中,较大尺寸磨球的自磨损率明显高于较小尺寸的磨球,这与一般在滚筒磨机进行自磨损试验中观察到的结果不一致。一般认为,同质量的小尺寸磨球因其球粒数量多,接触磨损点多,因此自磨损率高。但本试验在快速研磨机进行,由于强烈的振动冲击条件,磨球尺寸越大,磨球之间所产生的冲击力也越大,此时磨球表面的摩擦磨损机理可能已发生了变化,对此应做进一步的研究。
4 结 论
(1)采用凝胶固相合成法生产的亚微米级3mol%Y2O3-ZrO2陶瓷粉体为原料,通过控制合适的滚制成型工艺参数,可获得体积密度高、圆度好、大小均匀的球坯;
(2)烧结温度对氧化锆陶瓷磨球的自磨损率有重要影响,在快速研磨机试验条件下,经1500℃烧结后,磨球体积密度为5.97g/cm3,晶粒尺寸约0.5μm,自磨损率;
(3)在快速研磨机试验条件下,由于振动冲击的影响,较大尺寸磨球的自磨损率明显高于较小尺寸的磨球,这与一般在滚筒磨机进行自磨损试验中观察到的结果不一致,此时磨球的摩擦磨损机理可能已发生了变化,对此应做进一步的研究。