行业知识
超细液状分散染料研磨工艺条件的优化
作者:admin日期:2020-08-12阅读
超细液状分散染料的制备大致可以分为三个过程:润湿、研磨与分散、稳定。润湿即为分散染料颗粒表面的空气被水所置换。但是,润湿要有一个过程,特别是因为分散染料滤饼是一个团聚体,溶剂需要浸入染料的空隙。在超细液状分散染料的制备过程中,由于分散染料的性较小,水对分散染料的润湿便有困难,需要添加分散剂对分散染料颗粒进行表面改性,以提高其亲水性。
研磨与分散是将分散染料超细化的一种十分高效且经济的手段。因为分散染料滤饼是一个团聚体,因此要将它们细化并且分散开来,这需要给予一定的剪切力或撞击力。机械球磨法的原理是利用外部机械力的作用,即通过球磨介质、球磨罐和染料颗粒之间的频繁碰撞,染料颗粒在球磨过程中被地剪切、挤压、变形、碎裂。随着球磨过程的继续,颗粒表面的缺陷密度增加,颗粒逐渐细化。
分散染料在球磨机中研磨时,对于体积为V 的染料悬浮体系,部分体积Veff能克服粒子内部张力,发生破碎。破碎概率公式如(2-1)
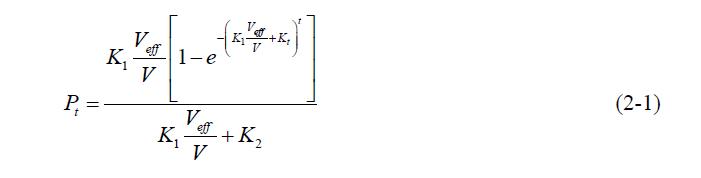
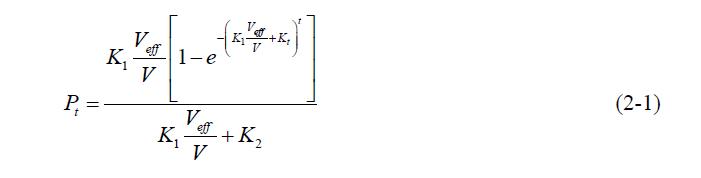
根据破碎概率公式(2-1)可知,Pt 为染料破碎概率,破碎概率越大,团聚数目就越少,粒径就越小,研磨效率就越高。研磨时间为t,当t 由小变大时,Pt 逐渐变大,但变化越来越小,当t 接近无穷大时,Pt 达到值;当有效体积Veff 越大,Pt 就越大。有效体积Veff 与球磨设备、染料含固量及研磨介质等指标有关;比例系数K1 与搅拌速度、助溶剂和分散剂等有关;比例系数K2 与温度和分散剂等有关[1,3]。机械球磨法具有工艺简单、成本及产量大等优点,目前广泛应用于颜料、染料、陶瓷及其它无机氧化物的超细化加工中。付少海[4]利用研磨法制备了超细颜料红122的水性分散体系,探讨了研磨机转速、研磨时间、超分散剂及吸附促进剂对超细颜料红122 粒径大小及其分散体系稳定性的影响;沈卫庆等[2]从分散染料的团聚和破碎机理出发,建立了团聚破碎概率的数学公式,并据此优化了研磨工艺参数,得到了均匀稳定的染料液体;吴艳平等[5]也通过对研磨珠大小、研磨机转速及研磨时间的探讨,制备出了符合陶瓷喷墨打印性能要求、实际打印效果较好的陶瓷墨水;万志友等[6]采用单因素试验设计方法研究了氧化锌浓度、研磨时间及转轴转速对制备纳米氧化锌的影响,筛选出了湿法研磨制备纳米氧化锌的佳工艺条件,结果显示样品颗粒大小均一。
本章采用单因素试验设计方法,通过探究研磨机转速、氧化锆球直径大小、研磨时间、分散染料含固量、分散染料与氧化锆球质量比及分散剂用量对分散橙30 研磨效率的影响,从而对研磨工艺条件进行优化。
2.1 实验部分
2.1.1 实验药品
分散橙30 滤饼(浙江万丰化工有限公司提供),分散剂SL(木质素磺酸钠)、分散剂MF(甲基萘磺酸钠甲醛缩合物)(安阳双环助剂厂),乙二醇(分析纯,江苏无锡县化学试剂厂),去离子水(实验室自制)。
2.1.2 实验仪器
PMQW 系列行星式球磨机(南京驰顺科技发展有限公司),Zetasizer Nano ZS90 纳米粒度和Zeta 电位分析仪(英国Malvern 公司),JJ200 型精密电子天平(常熟双杰测试仪器厂),ALC-210 电子天平(德国赛多利斯集团)。
2.1.3 实法
2.1.3.1 研磨机转速对研磨效率的影响
设定液状分散染料的含固量为30%,分散剂SL 与原染料干重比为3:8。称取分散橙30 5.58 g(折干重5 g)加入到球磨罐中,再加入1.88 g 分散剂SL、15.47g 去离子水及50 g 氧化锆球(1 mm),分别在400 r/min、500 r/min、600 r/min 的转速下进行研磨12 h,每隔2 h 测其粒径和扩散性。
2.1.3.2 氧化锆球直径对研磨效率的影响
设定液状分散染料的含固量为30%,分散剂SL 与原染料干重比为3:8。称取分散橙30 5.58 g(折干重5 g)加入到球磨罐中,再加入1.88 g 分散剂SL、15.47g 去离子水及50 g 氧化锆球,其直径分别为0.5 mm、1 mm、6 mm,在500 r/min 的转速下进行研磨12 h,每隔2 h 测其粒径和扩散性。
2.1.3.3 研磨时间对研磨效率的影响
设定液状分散染料的含固量为30%,分散剂SL 与原染料干重比为3:8。称取分散橙30 5.58 g(折干重5 g)加入到球磨罐中,再加入1.88 g 分散剂SL、15.47g 去离子水及50 g 氧化锆球(1 mm),在500 r/min 的转速下进行研磨,每隔2 h 测其粒径和扩散性,直到粒径不再变化。
2.1.3.4 分散染料含固量对研磨效率的影响
设定分散剂SL 与原染料干重比为3:8。称取分散橙30 11.16 g(折干重10 g)加入到球磨罐中,再按表2-1 所示的分别加入一定量的分散剂SL 和去离子水,然后加入100 g 氧化锆球(1 mm),在500 r/min的转速下进行研磨18 h,每隔2 h 测其粒径和扩散性。
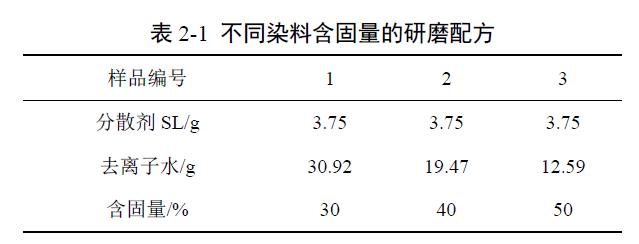
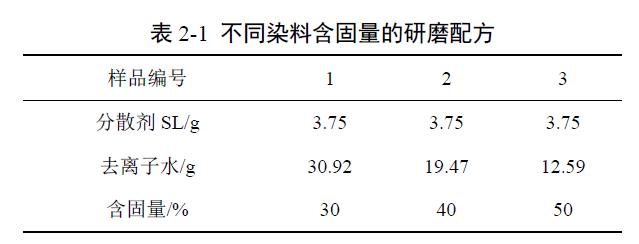
2.1.3.5 分散染料与氧化锆球质量比对研磨效率的影响
设定液状分散染料的含固量为40%,分散剂SL 与原染料干重比为3:8。称取分散橙30 11.16 g(折干重10 g)加入到球磨罐中,再加入3.75 g 分散剂SL、19.47 g 去离子水以及质量分别为50 g、100 g、150 g 氧化锆球(1 mm),在500 r/min的转速下进行研磨18 h,每隔2 h 测其粒径和扩散性。
2.1.3.6 分散剂对研磨效率的影响
设定液状分散染料的含固量为40%。
称取分散橙30 11.16 g(折干重10 g)加入到球磨罐中,再按表2-2 所示的分别加入一定量的分散剂和去离子水,然后加入100 g 氧化锆球(1 mm),在500 r/min 的转速下进行研磨18 h,每隔2 h 测其粒径和扩散性。
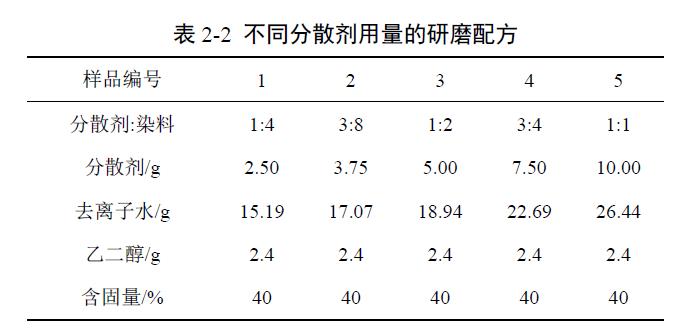
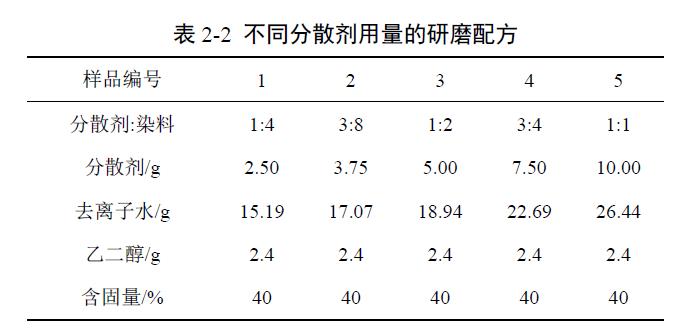
2.1.4 测试方法
2.1.4.1 超细液状分散染料颗粒的粒径及Zeta 电位测试
取少量液状超细分散染料,用去离子水稀释至1000 倍。开启Malvern 纳米粒度及Zeta 电位分析仪30 min 后,将少量稀释的分散液倒入样品池中,使用动态光散射以90°散射角测量分散染料颗粒粒径及粒径分布指数(PDI),其中PDI 数值越小,颗粒粒径分布越窄,粒径越集中;PDI 数值越大,则粒径分布越宽,粒径越离散。取少量稀释的分散液于带有电的毛细管样品池中,采用激光多普勒微量电泳法测量颗粒表面Zeta 电位。
2.1.4.2 超细液状分散染料的扩散性测试[7]
根据HG/T 3399-2001 《染料扩散性能的测定》,具体方法如下:称取染料样品0.5 g(按液状分散染料的含固量折算,精确至0.001 g),加少量去离子水调成浆状,再加去离子水至100 mL,搅拌,备用。将滤纸平放在表面皿上,吸取0.2 mL 染料悬浮液,垂直并保持滴管距离滤纸约1 cm,然后自然滴落,待液滴将渗完时再滴下一滴,使其自然扩散。待干燥后与“染料扩散性能测试样卡”对比评级。扩散等级分为1~5 级,1 级差,5 级好。
2.2 结果与讨论
2.2.1 研磨机转速对研磨效率的影响
分别设定研磨机转速为400 r/min、500 r/min、600 r/min,图2-1 表示在不同研磨机转速下,液状分散橙30 颗粒粒径随研磨时间的变化,表2-3 为相应研磨时间下,其扩散性能,图2-2 为其粒径分布指数随研磨时间的变化。
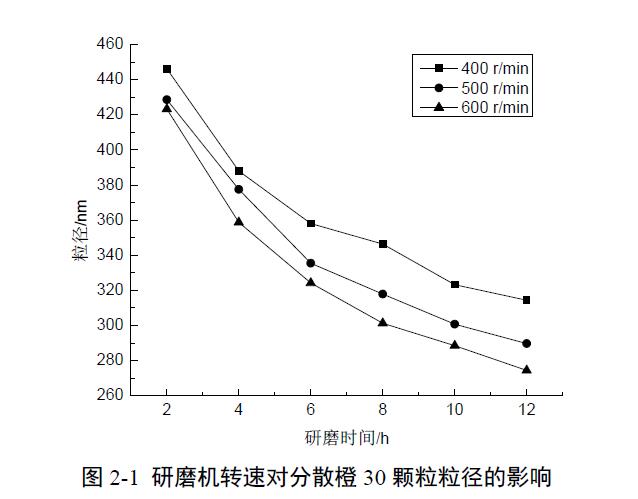
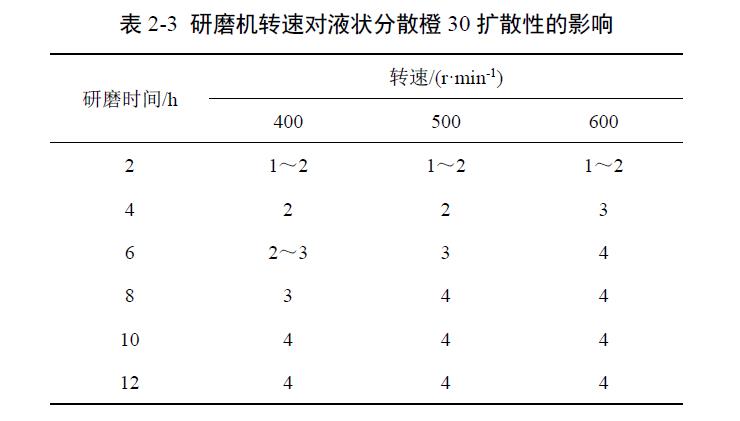
由图2-1 可以看出,当研磨机转速为600 r/min 时,在相同的研磨时间内,得到的分散橙30 颗粒粒径小,其次是转速为500 r/min 时,当转速为400 r/min 时,染料颗粒粒径大。由表2-3 也可知,当转速为500 r/min、600 r/min 时,液状分散橙30 的扩散性达到4 级分别需要8、6 h,而当转速为400 r/min 时,扩散性达到4 级,需研磨10 h。所以,当研磨机转速为600 r/min 时,研磨效率高,转速为500 r/min时,研磨效率次之,当转速为400 r/min 时,研磨效率。即在相同研磨条件下,研磨机转速越大,液状分散染料颗粒平均粒径越小,且在较短的时间内能获得的扩散性能。因为染料破碎和分散是一个耗能的过程,染料团聚体从外界获得足够的才能发生破碎。研磨机转速越高,研磨介质产生的剪切力越大,单位时间内染料颗粒获得的越多.
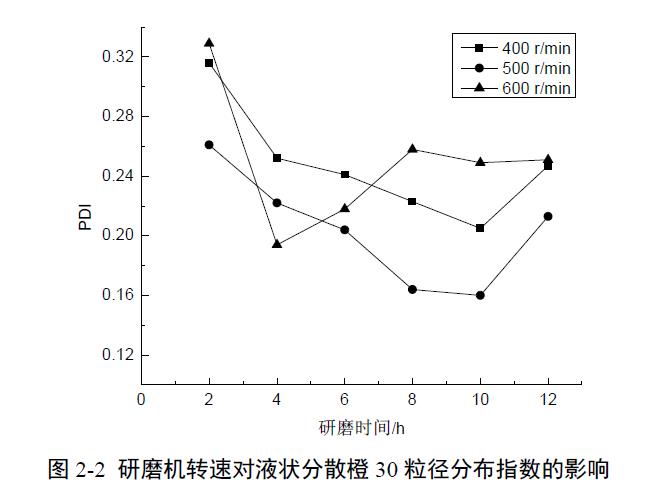
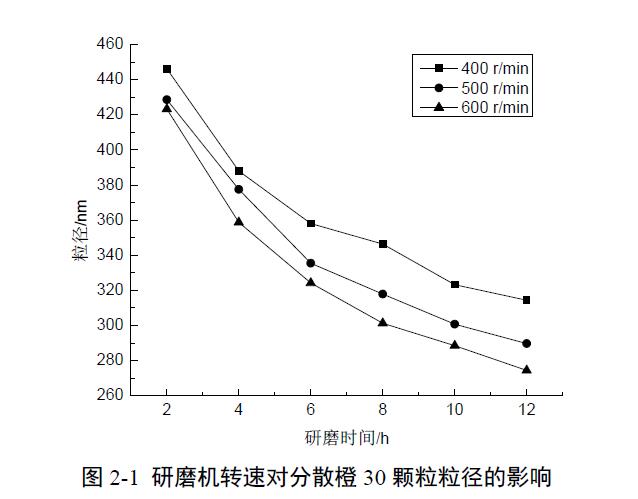
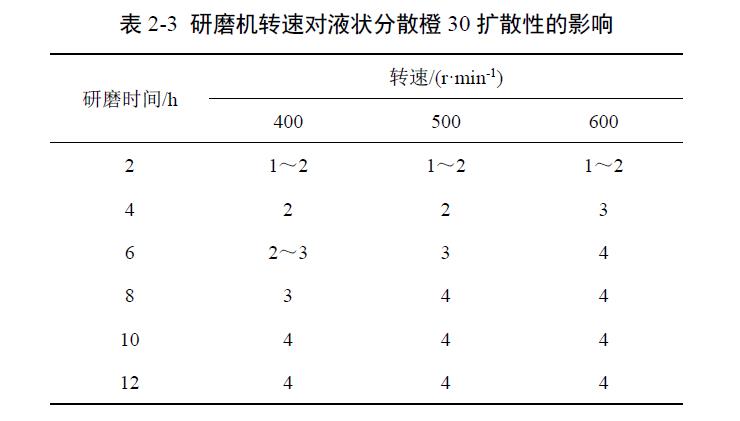
由图2-1 可以看出,当研磨机转速为600 r/min 时,在相同的研磨时间内,得到的分散橙30 颗粒粒径小,其次是转速为500 r/min 时,当转速为400 r/min 时,染料颗粒粒径大。由表2-3 也可知,当转速为500 r/min、600 r/min 时,液状分散橙30 的扩散性达到4 级分别需要8、6 h,而当转速为400 r/min 时,扩散性达到4 级,需研磨10 h。所以,当研磨机转速为600 r/min 时,研磨效率高,转速为500 r/min时,研磨效率次之,当转速为400 r/min 时,研磨效率。即在相同研磨条件下,研磨机转速越大,液状分散染料颗粒平均粒径越小,且在较短的时间内能获得的扩散性能。因为染料破碎和分散是一个耗能的过程,染料团聚体从外界获得足够的才能发生破碎。研磨机转速越高,研磨介质产生的剪切力越大,单位时间内染料颗粒获得的越多.
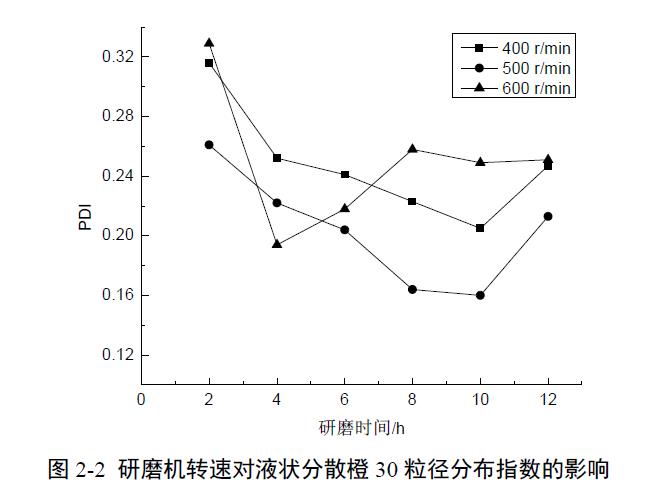
但是,研磨机转速太高,染料颗粒获得巨大的,短时间内产生过小或过大的染料颗粒,从而使得颗粒粒径分布变宽,图2-2 表明,当研磨机转速为600 r/min时,研磨4 h 后,液状分散橙30 颗粒粒径分布指数就开始,甚至逐渐超过了转速为400 r/min 时研磨得到的液状分散染料。同时,在过高的转速下,研磨罐和研磨介质的磨损,机器发热量也变大,容易对机器造成,影响机械使用寿命。考虑到当研磨机转速为500 r/min 时,研磨8 h 后,液状分散橙30 的扩散性也能达到4级,而且,在研磨过程中颗粒粒径分布指数较小,粒径分布较窄。所以,后续实验研磨机转速选择500 r/min。
2.2.2 氧化锆球直径大小对研磨效率的影响
分别用0.5 mm、1 mm、6 mm 的氧化锆球对分散橙30 滤饼进行研磨,图2-3 表示在不同直径的氧化锆球研磨下,染料颗粒粒径随研磨时间的变化,表2-4 为相应研磨时间下,其扩散性能,图2-4 为其粒径分布指数随研磨时间的变化。
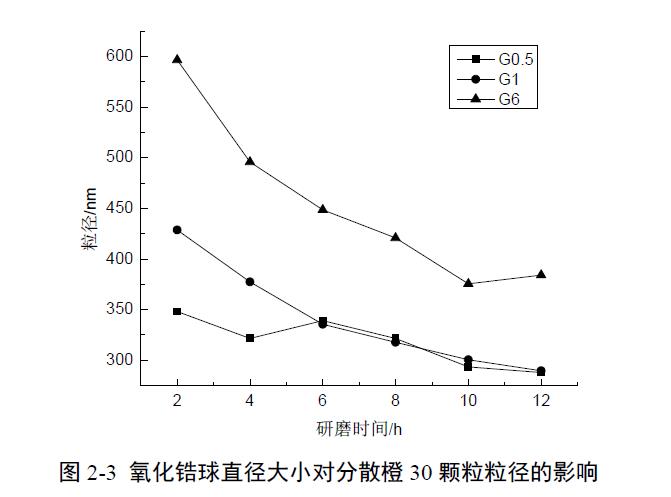
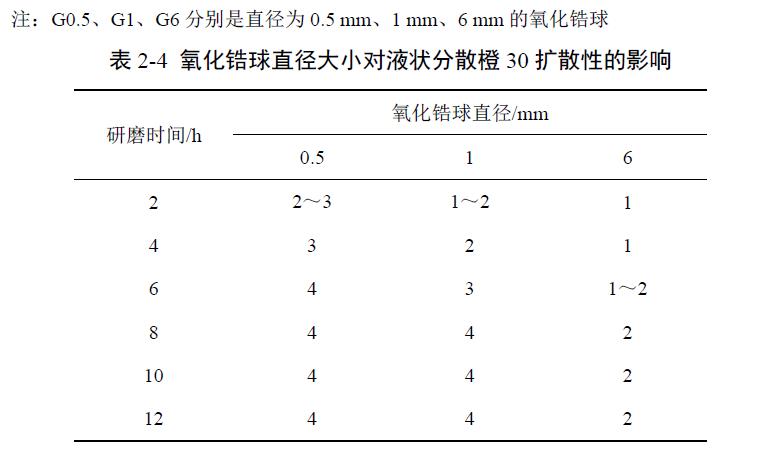
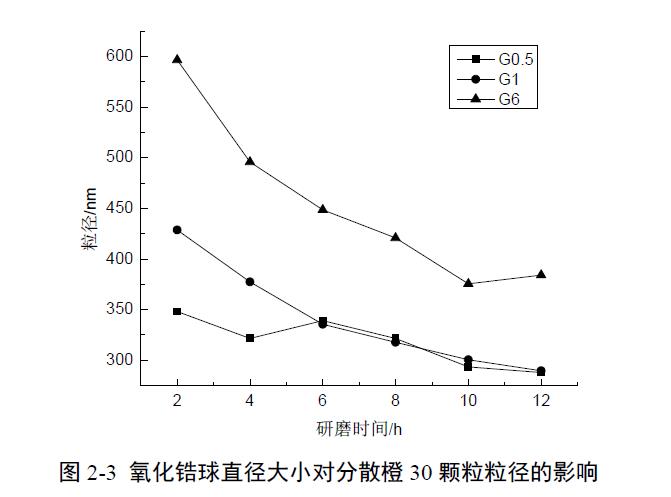
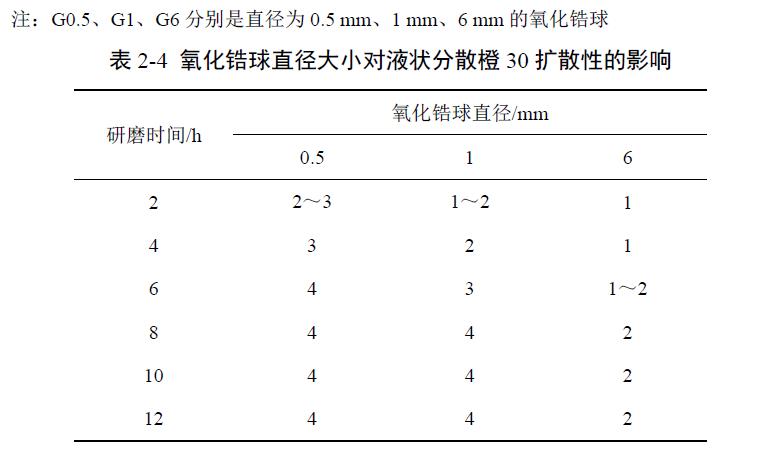
由图2-3 可以看出,氧化锆球直径越小,分散橙30 颗粒粒径下降得越快,研磨效率越高,即说明在相同研磨条件下,直径较小的氧化锆球能在较短时间内降染料颗粒的粒径。但是,研磨6 h 后,用直径为0.5 mm 和1 mm 的氧化锆球研磨的液状分散染料颗粒粒径相当,即G0.5 的研磨效率优势减小,这与表2-4 染料扩散性表现出来的规律相符,在研磨8 h 后,使用G0.5 和G1 研磨的液状分散橙30 的扩散性均达到4 级,且随后两者的扩散性均没有再变化。然而,无论从颗粒粒径,还是扩散性来看,G6 的研磨效率都要差很多。一方面,直径小的氧化锆球,球与球之间的空隙会更小,故可以通过挤压得到粒径更小的颗粒;另一方面,氧化锆球可以与染料发生正面碰撞,这种由碰撞带来的强大剪切力可以将染料颗粒粉碎得更小。在氧化锆球质量相同的情况下,其直径越小,与染料颗粒的接触点越多,即可与染料颗粒发生碰撞的总面积越大,所以,能够产生的冲击越多,碰撞越剧烈,颗粒被碎裂得越小。
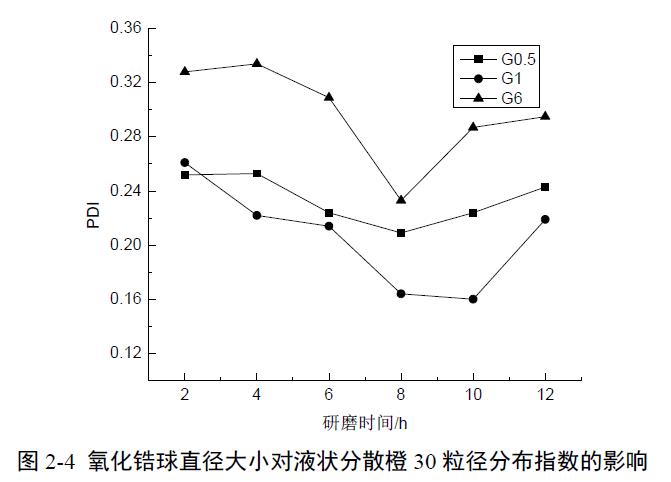
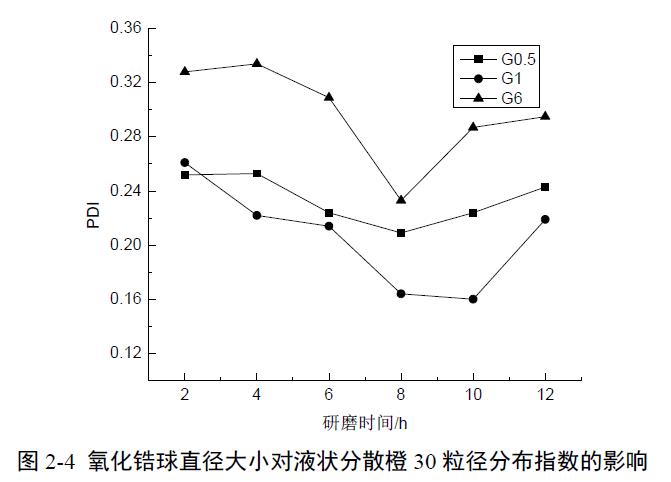
虽然直径较小的氧化锆球的研磨效率更高,更有利于使染料颗粒研磨得更小。但是,氧化锆球的直径也并非越小越好,因为经研磨细化的液状分散染料颗粒还涉及到分散稳定性的问题。由于直径较小的氧化锆球产生的碰撞越多,也越容易使分散体系的温度升高,从而加剧了粒子的热运动,了粒子间的接触机率,更易与发生二次团聚,使得分散体系的分散性变差,如图2-4 所示,G1 研磨得到的液状分散橙30 粒径分布指数比G0.5 研磨的小,颗粒粒径分布更窄,即粒径更加集中,颗粒分散更稳定。而且,氧化锆球直径太小,单个小球重量小,尤其在制备高含固量分散体时,由于其粘度变大,因粘滞力的影响会导致碰撞剪切力减小,不利于研磨;同时,氧化锆球太小,研磨结束后,氧化锆球与液状分散染料分离困难。所以,后续实验采用直径为1 mm 的氧化锆球进行研磨。
2.2.3 研磨时间对研磨效率的影响
图2-5 为研磨时间对分散橙30 颗粒粒径及粒径分布指数的影响,图2-6 为液状分散橙30 的扩散性随研磨时间的变化。由图2-5 可以看出,随着研磨时间的延长,染料颗粒粒径逐渐变小,研磨2~6 h,染料颗粒粒径急剧减小,研磨6~14 h,染料颗粒粒径减小的趋势变缓,研磨14 h 后,基本保持不变,此时的研磨效率已经很,继续延长研磨时间对分散染料研磨效果帮助不大。在研磨过程中,染料的破碎与团聚是同时存在的,经过一定时间后,染料的破碎-团聚处于动态平衡,正如破碎概率公式(2-1)所示,当t 接近无穷大时,Pt 达到值。在这种情况下,即使延长研磨时间,染料的粒径也不再有较大的变化。染料的分散和聚集是一个动态过程,一方面随着研磨时间的增加,染料在外力的作用下获得,染料颗粒被粉碎,粒径减小,并且在分散剂的作用下,分散的颗粒可以保持相对稳定,另一方面,染料颗粒在范德华力作用下相互吸引,易发生聚集,特别是当染料的粒径降后,比表面积,表面自由能增加,染料颗粒自动聚集的倾向变大。当这两种作用达到平衡后,染料颗粒的粒径不再变化。如图2-5 所示,当研磨14 h 后,平均粒径达到289.4 nm,此后,粒径变化幅度很小。即分散和聚集可能已经达到平衡。
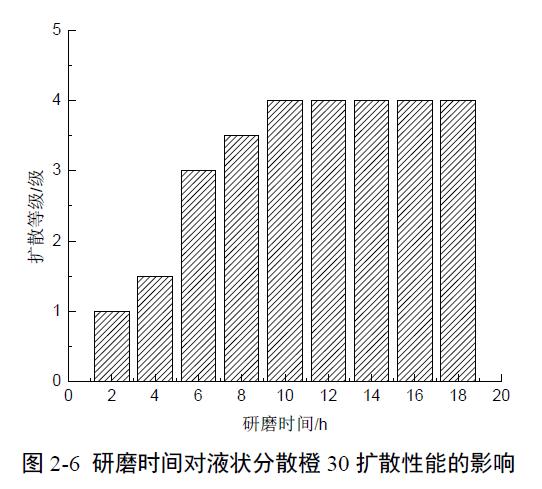
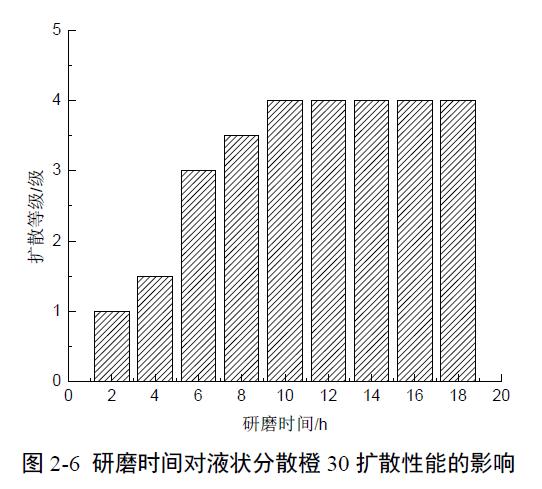
而且,研磨时间继续延长,染料颗粒粒径分布指数开始,染料粒径分布变宽,粒径分布变得更加离散。图2-6 表明,研磨10 h 后扩散性也一直保持在4 级,所以,综合各类因素后研磨时间定为14~18 h。
2.2.4 分散染料含固量对研磨效率的影响
分别设定液状分散橙30 的含固量为30%、40%、50%,图2-7 表示不同含固量下,染料颗粒粒径随研磨时间的变化,表2-5 为相应研磨时间下,其扩散性能,图2-8 为其粒径分布指数随研磨时间的变化。
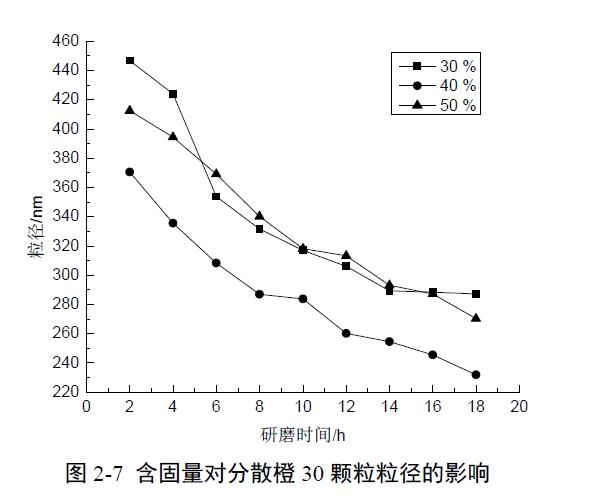
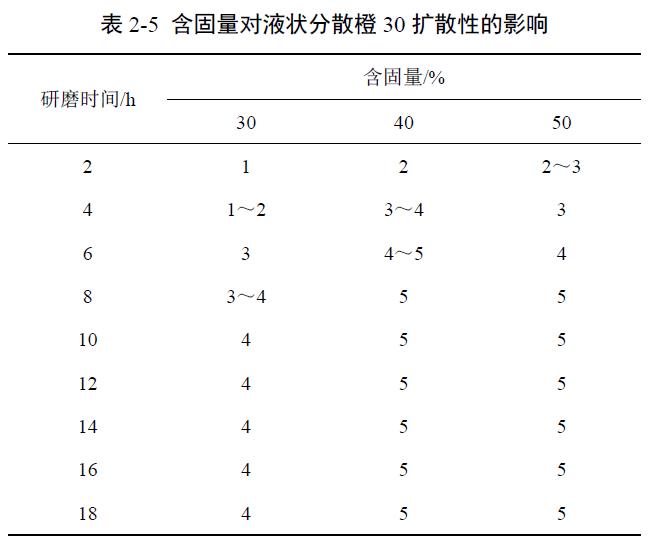
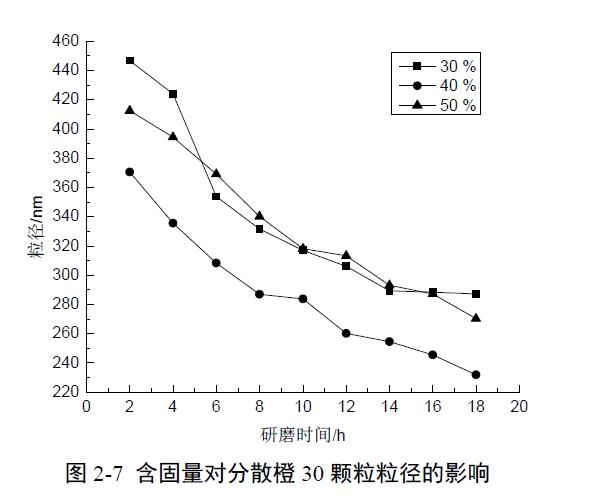
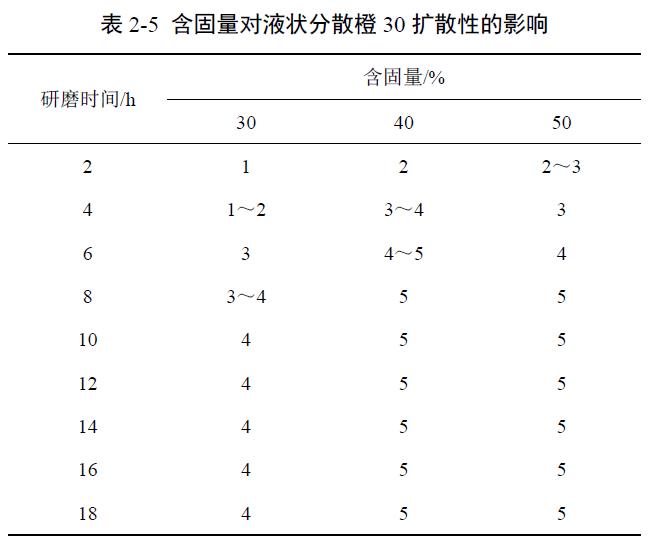
由图2-7 可以看出,在相同的研磨时间下,含固量为40%的液状分散橙30 颗粒粒径远小于含固量为30%、50%的颗粒粒径,则其研磨效率远高于含固量为30%、50%的分散体系,而且,研磨18 h 后,其颗粒的平均粒径也比含固量为30%、50%的小40~50 nm。表2-5 也显示,当含固量为40%时,研磨8 h 后,液状分散橙30 的扩散性就能达到5 级,当含固量为50%时,研磨8 h 后,其扩散性也同样能达到5 级,虽然此时染料颗粒粒径较大,但是,如图2-8 所示,此时染料颗粒粒径分布指数很小,粒径分布集中,有利于染料的均匀扩散,而当含固量为30%时,其扩散性始终只能达到4 级。因为研磨时,染料含固量过,单位体积染料浆料中染料颗粒较少,即有效体积Veff 就变小,所以,氧化锆球与染料颗粒碰撞机会就相对较少。因此,提高染料含固量,有助于增加氧化锆球与染料颗粒的碰撞几率,提高破碎概率,更高效地使染料颗粒细化,从而在一定程度上提高染料的研磨效率。但如果染料的含固量高于40%,再继续提高染料的含固量却不能有效增加研磨效率,因为随着染料含量增加,染料颗粒之间接触、碰撞的几率也会增加,这会导致已经细化的颗粒重新团聚而使得粒径变大,所以研磨效率反而会降。此外,染料含固量过高使得染料分散体粘度变大,一方面对氧化锆球产生粘滞阻力,减小剪切力,另一方面,会影响研磨结束后研磨介质与染料浆料的分离。所以,后续实验采用染料含固量为40%。
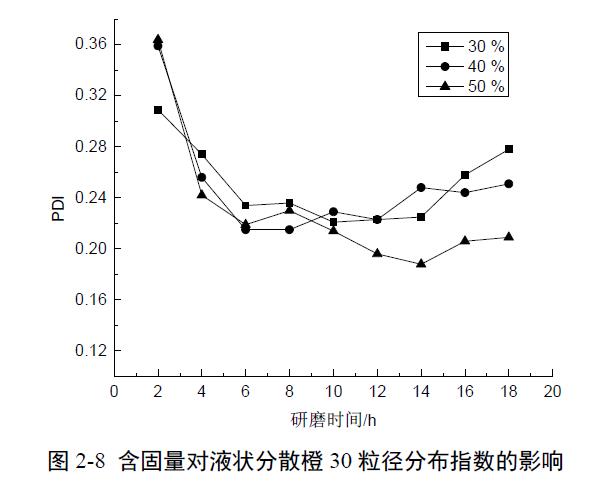
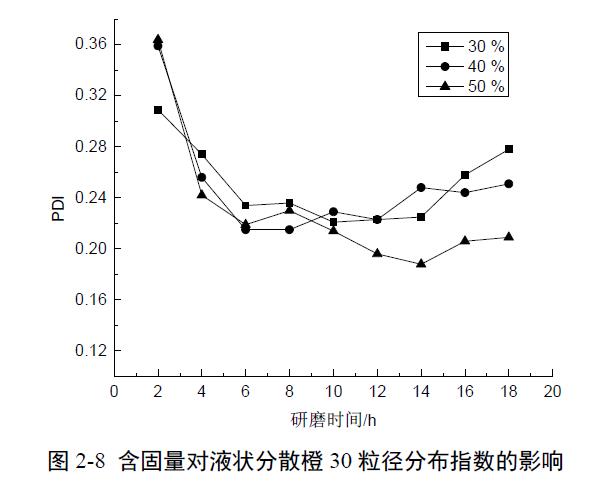
2.2.5 分散染料与氧化锆球质量比对研磨效率的影响
分别设定分散橙30 与氧化锆球(1 mm)质量比为1:5、1:10、1:15,图2-9 表示在不同染料与氧化锆球质量比下,染料颗粒粒径随研磨时间的变化,表2-6 为相应研磨时间下,其扩散性能,图2-10 为其粒径分布指数随研磨时间的变化。
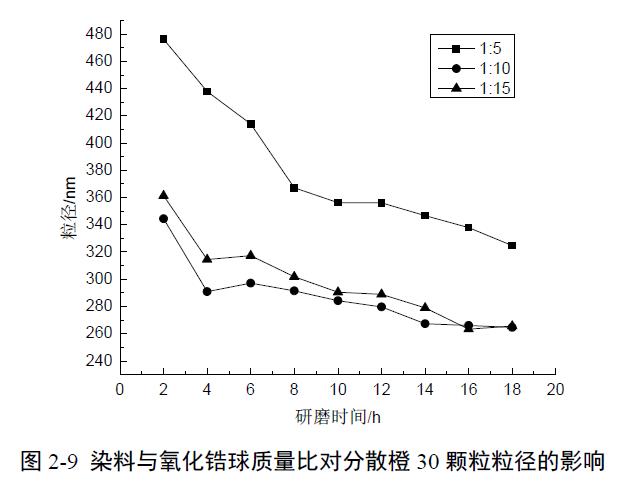
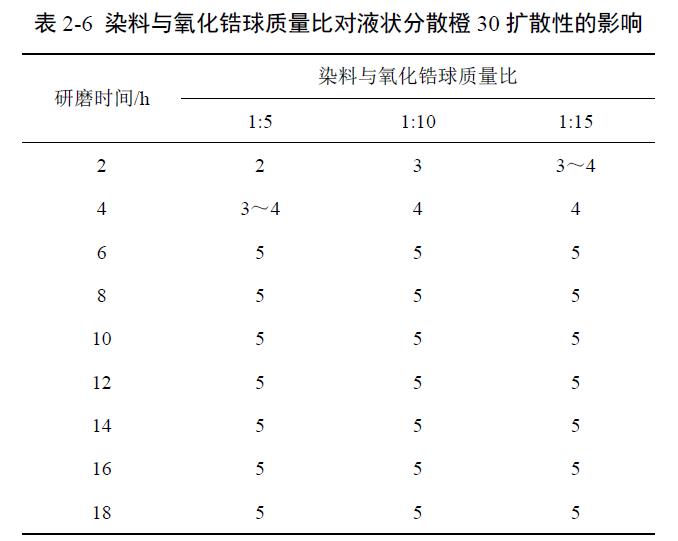
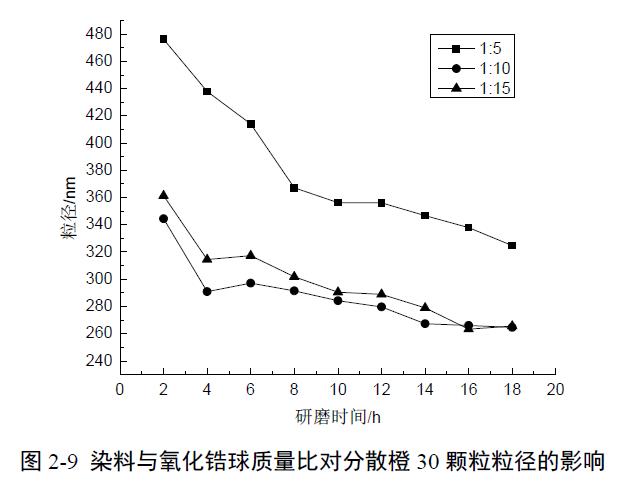
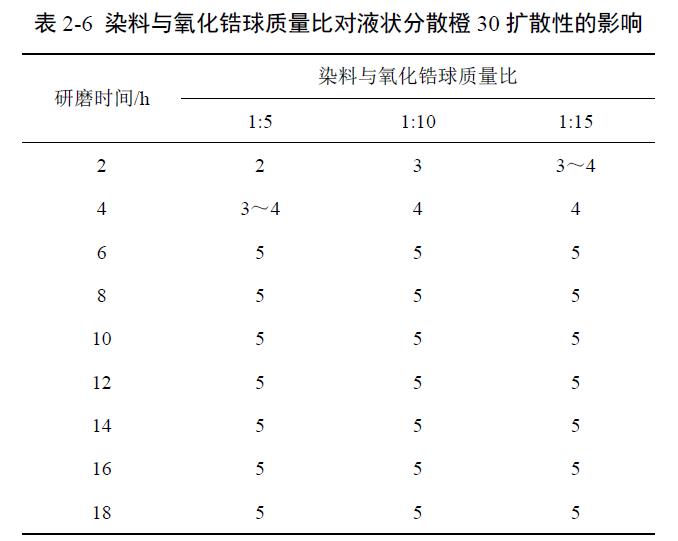
由图2-9 可以看出,当染料与氧化锆球质量比为1:10 时,在相同的研磨时间内,染料颗粒粒径小,质量比为1:15 时的染料颗粒粒径次之,但研磨16 h 后,两者粒径几乎相同,在研磨过程中质量比为1:5 的染料颗粒粒径却始终远大于前两者。可能是氧化锆球太少,从而导致单位体积内氧化锆球与染料颗粒的碰撞几率减小,故研磨效率。而当染料与氧化锆球质量比为1:15 时,研磨效率反而比质量比为1:10 时还要一些,可能因为在染料量一定时,增加氧化锆球的量,导致很多氧化锆球在进行自我撞击,并没有将转化到染料颗粒上,相反,由于氧化锆球自我碰撞产生大量热量使分散体温度升高,加剧了颗粒的热运动,染料颗粒接触机会,导致染料颗粒更易发生团聚。表2-6 显示,研磨6 h 后,染料与氧化锆球质量比为1:5、1:10、1:15研磨得到的液状分散橙30 的扩散性均能达到5 级。所以,综合染料颗粒粒径及扩散性来看,当染料与氧化锆球质量比为1:10 时,研磨效率高。
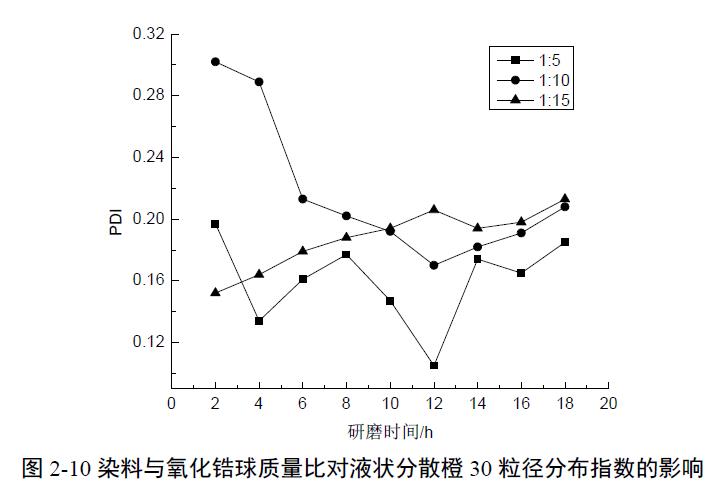
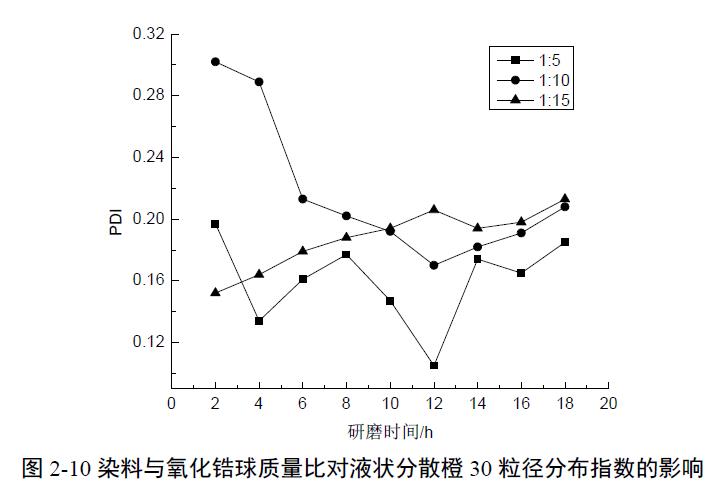
而且,图2-10 表明,质量比为1:5 研磨得到的液状分散橙30 颗粒粒径分布指数波动较大,质量比为1:15 研磨得到的液状分散橙30 颗粒粒径分布指数随着研磨时间的延长,一直增加,这说明液状分散橙30 颗粒尺寸不稳定,很难达到分散-聚集平衡,而质量比为1:10 研磨得到的液状分散橙30 颗粒粒径分布指数随着研磨时间的延长逐渐减小,然后趋于稳定,说明达到了分散-聚集平衡。故后续实验选择染料与氧化锆球质量比为1:10。