行业知识
玻璃珠、氧化锆珠、钢珠对色浆研磨效率的影响
作者:admin日期:2020-01-19阅读
研磨介质对色浆研磨效率的影响
2.2.1 研磨介质的类型对研磨效率的影响
研磨介质按材料不同可以分为玻璃珠、陶瓷珠(包括硅酸锆珠、氧化锆珠)、钢珠等。化学组成及制造工艺的差异决定研磨介质的晶体结构的不同,继而决定了研磨介质不同的抗压强度和耐磨性,成分的含量不同决定了研磨介质的密度,而由动力学公式P=mv可知,研磨介质的冲量P与研磨介质的质量成正比,研磨介质的密度越大,动能越大,研磨效率也就越高[3]。表3是常用的研磨介质的参数对比。
研磨介质按材料不同可以分为玻璃珠、陶瓷珠(包括硅酸锆珠、氧化锆珠)、钢珠等。化学组成及制造工艺的差异决定研磨介质的晶体结构的不同,继而决定了研磨介质不同的抗压强度和耐磨性,成分的含量不同决定了研磨介质的密度,而由动力学公式P=mv可知,研磨介质的冲量P与研磨介质的质量成正比,研磨介质的密度越大,动能越大,研磨效率也就越高[3]。表3是常用的研磨介质的参数对比。
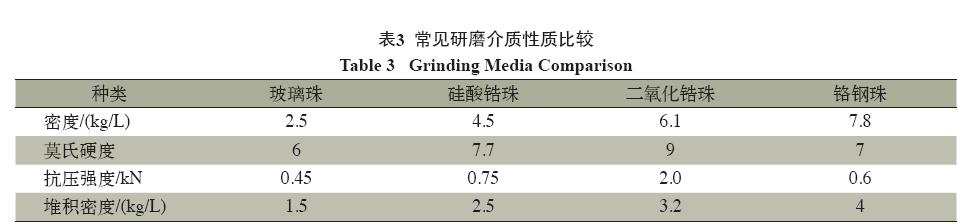
配制450 kg的钛白粉浆,在A型砂磨机中按65%体积填充比分别填充玻璃珠(Φ2~3 mm)和硅酸锆珠(Φ2.2~2.4 mm),在额定功率下研磨,每隔一段时间测定细度,试验结果见图7。
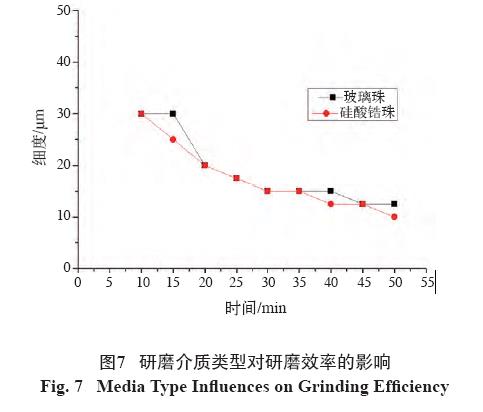
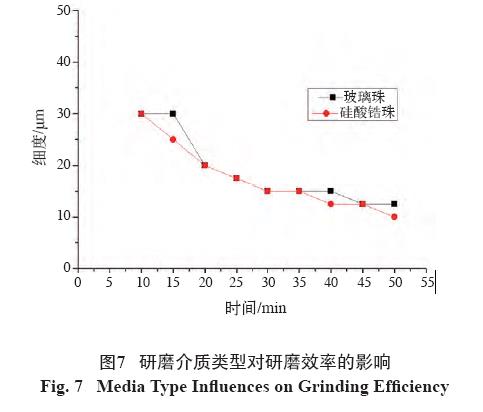
由图7可知,硅酸锆珠的分散效率略高于玻璃珠,这主要是由于在硅酸锆珠相比玻璃珠的堆积密度和硬度大,具有更高的动能,提高了研磨效率;而在实际生产过程中也发现,相比硅酸锆珠,玻璃珠的磨耗率更高,更容易出现碎珠现象,卡在介质分离的缝隙内,阻塞出料装置,影响研磨效率。
研磨介质的尺寸对研磨效率的影响
研磨介质的大小决定了研磨介质与色浆的接触点的多少,粒径小的研磨介质在相同体积下的接触点越多,理论上的研磨效率越高;但另一方面,在研磨初期颜料粒径较大时,研磨介质粒径小的冲量较小,达不到较好的研磨效果;研磨后期,大粒径的研磨介质由于接触点少,密度不足,导致粒径分布比小尺寸研磨介质差[4]。
本试验结合廖红[5]等在砂磨机研磨介质装填量中的计算和笔者的实际应用经验,在卧盘式砂磨机B中按70%体积填充比分别填充Φ2.2~2.4 mm硅酸锆珠、Φ1.2~1.4 mm纯氧化锆珠和上述两种研磨介质按质量比1∶1混装的混合珠,分别测定堆积密度,结果见表4。
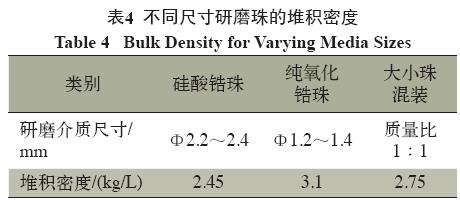
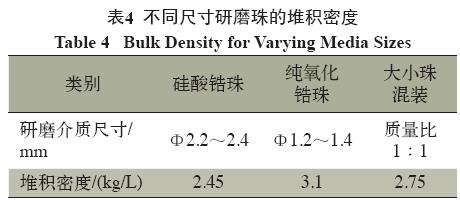
配制250 kg酞菁蓝浆,在上述3种不同研磨介质中进行研磨,每隔一段时间测定细度,结果见图8。由图中曲线可知,单独使用Φ2.2~2.4 mm硅酸锆珠时,前30 min的分散效率较高,单独使用Φ1.2~1.4mm氧化锆珠时,产品终细度,采用大小珠混合
的方式时,效率并没有比单独使用Φ1.2~1.4 mm的研磨介质提高,反而有所降。
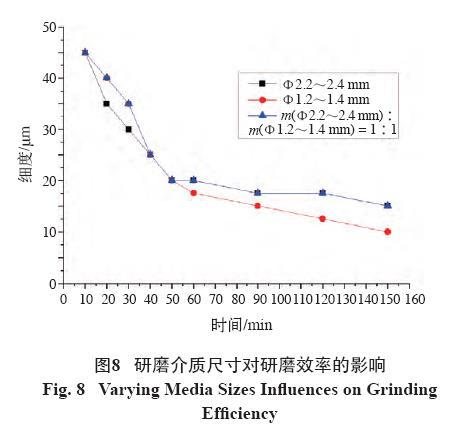
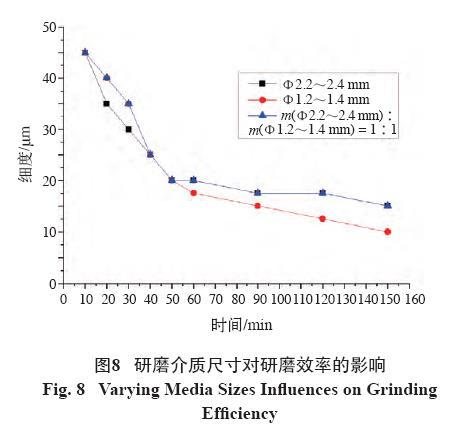
研磨工艺对研磨效率的影响
不同品种的色浆,因其颜料类型(无机颜料、颜料、炭黑)、细度要求、色浆黏度等参数的不同,所对应的研磨工艺也不尽相同。选择合适的色浆研磨工艺可以显著地提高色浆的研磨效率,提高色浆的研磨效果,对产量的稳定性提高有非常重要的意义。
按量制备250 kg炭黑浆,采取3种不同的研磨工艺进行研磨,并分别测定细度如下:
(1)卧砂A单机双缸三道,细度达到17.5 μm;
(2)卧砂B单机双缸三道,细度达到12.5 μm;
(3)卧砂A一道+卧砂B二道,细度达到10 μm。
结果表明:(3)卧砂A一道+卧砂B二道的模式,结合了A型砂磨机前期效率高和B型砂磨机后期效率高、终细度的特点,提高了分散效率。在实际生产中使用该工艺一段时间后统计,研磨中色素炭黑和颜料色浆时,研磨效率提高15%以上,且色浆拥有贮存稳定性。
2.4 色浆流量对研磨效率的影响
用卧式砂磨机B(大流量卧式砂磨机)进行试验。以70%填充比填充Φ1.2~1.4 mm纯氧化锆珠,相同的转轴速度(800 r/min)和同一冷却水条件下,对比不同色浆流量对研磨效率的影响,试验结果见表5。由表5可知,在相同的转轴速度下,选择大流量时,色浆在筒体内的停留时间短,在无机颜料的分散
和颜料的初期分散中,细度相差不大,而分散颜料的后期,适当降流量,增加在筒体内的停留时间,可以保证通过两次研磨即可达到细度要求减少了研磨道数。因此选择一道色浆流量为6.5 L/min,二道色浆流量无机颜料6.5 L/min、颜料和炭黑色浆为5 L/min。
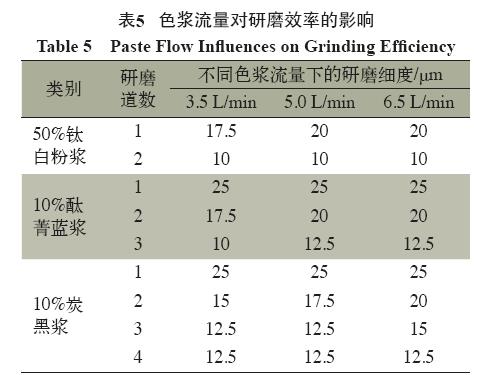
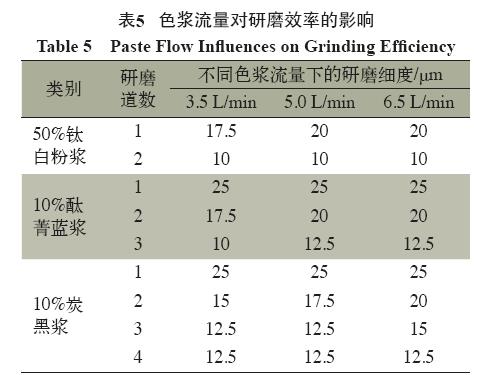
结 语
(1)涂料色浆的研磨效率和效果与研磨分散设备的参数、研磨介质类型与尺寸和研磨工艺有关;研磨设备介质分离结构的动态离心分离系统比传统的鼓型出料筛圈在介质分离的稳定性上有优势;采用填充卧式砂磨机A(Φ2.2~2.4 mm硅酸锆珠填充)串联卧式砂磨机B(Φ1.2~1.4mm纯氧化锆珠填充)的研磨工艺,提高了羟基丙烯酸树脂色浆的研磨效果和稳定性,研磨效率提高15%以上。
(2)大流量卧式砂磨机拥有高密度和动态介质分离结构的设计特点,实现了较好的研磨效果和较高的研磨效率。选择6.5 L/min为一道研磨流量,5L/min为二道研磨流量,以填充比为70%填充Φ1.2~1.4 mm纯氧化锆珠的设备运行参数和工艺,研磨效果较好,可以提高色浆的研磨效率。