行业知识
球磨制备超细硅酸锆分段磨的实践
作者:admin日期:2020-02-04阅读
0 引言
硅酸锆超细粉作为釉料乳浊剂广泛用于卫生洁具、墙地砖、釉面砖、炻器制品、工艺陈设瓷及特种陶等。目前,硅酸锆超细粉的生产加工广泛采用的粉磨设备主要有搅拌磨、气流磨、振动磨等,而球磨机一直被认为是一种效率、能耗大的生产设备,难以将物料粉碎到微米级,故在超细粉磨行业很少使用。但湿法球磨具有操作方便、产量大和产品粒度分布窄等其他超细粉碎设备不可比拟的优点。在国内先进行硅酸锆珠磨超细技术的研发,2000年采用球磨机湿法制备超细硅酸锆的生产线投产,现产量可达6000t/a,从而使国产超细硅酸锆的市场份额大幅增加。
1 球磨分段磨湿法生产工艺
1.1 分段磨原理
所谓分段法磨矿技术,即在磨矿工艺流程和设备选择时,以提高磨矿能力为前提,以采用分段磨矿为主要手段,选择高效化磨矿、分级设备,优化组合,实现磨矿系统高处理量能耗的目的。
根据磨矿动力学可知,物料在磨机中的磨矿速率与磨机中所具有的粗颗粒含量成比例(可理解为大于指定粒度的颗粒)。理想的情况是粗颗粒一经磨至合格粒度,就马上从磨机中排除,然后经分级作业分出,送往下一步工序中,粗大颗粒部分进行再磨。但在实际工作中,由于采用的分级设备分级效率的影响以及给到磨机的总物料量(原矿+返砂)对适宜球料比的影响,都会导致磨矿效率偏。
众所周知,研磨介质的大小,直接影响球磨机加工产品的终粒度和粒度分布。研磨介质的直径愈大,对大颗粒的作用愈明显,产品的终粒度愈粗;反之,研磨介质的直径愈小,对小颗粒的作用愈明显,产品的终粒度愈细。另外,颗粒粒度越细,比表面积越大,粉碎时所需有效粉碎区域越大。而减小磨球直径,增加磨球个数,可增加磨球间的有效粉碎区域。由微观机械化学基本理论可知,在超细粉碎过程中,一方面,机械作用导致物料颗粒粒度减小,比表面积;另一方面,机械作用也促进物料颗粒的聚结,从而表观粒度,减小比表面积。经过一定时间,超细粉碎处于粉碎、团聚的动态平衡(即颗粒尺寸达到粉碎限),在这种状态下,即使再延长粉碎时间,也难以再减小物料颗粒粒径,甚至会使其表观粒度变粗,大大降磨矿效率。通常研磨介质在运转一段时间后就会形成一定的直径大小级配,随着粉碎的进行,颗粒粒度变小,在粉碎高效阶段各直径大小级配的球可以满足不同阶段所需的有效粉碎区域,但随着小颗粒数量的继续增多,研磨介质中小球的数量已经满足不了所需的有效粉碎区域,这时磨矿效率就会下降,磨机延长球磨时间才能达到粉碎的目的。等达到这种研磨介质直径大小级配粉碎的,就会出现上面提到的超细粉碎处于粉碎、团聚动态平衡的现象。在球磨制备超细硅酸锆过程中,为了提高粉碎效率必须把细颗粒部分分离出来,即分级,但通过分级后的沉砂粒度已经比锆英砂细了很多,研磨介质中的大球对其粉碎作用变得很小,如果采用混合磨,则在前期大球只对锆英砂起到快速的粉碎作用,而对沉砂的粉碎效果较差,从而降了粉碎效率,这就使得分段磨显得特别重要。
1.2 二段磨与一段磨工艺对比
1.2.1 工艺流程对比
一段磨和二段磨工艺流程图见图1和图2。
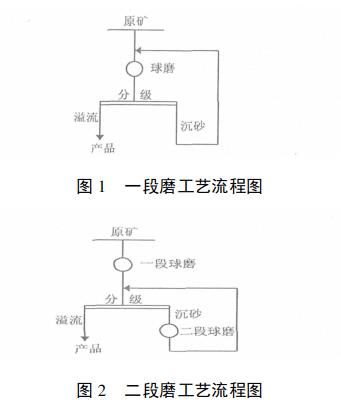
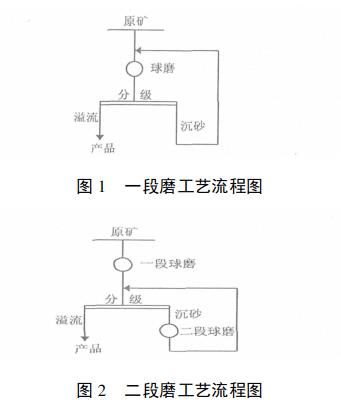
1.2.2 生产试验条件
试验粉碎设备:佛山产的 1.8m×3.4m球磨机,每次装料3t,转速25r/min;分级设备:卧式螺旋分级机;粒度测试仪:辽宁丹东百特公司所产BT-9300激光粒度仪;研磨介质:一段球磨研磨介质为直径30mm刚玉球,二段球磨研磨介质为直径10mm的刚玉球,研磨介质直径大小级配为研磨过程中所形成的自然级配,装球率为45%~50%;入球物料:锆英砂粒度为80目(173μm),分级沉砂粒度为D50=12.88μm,D97=58.37μm,-5μm21.58%,-10μm42.86%;磨料质量分数为72%。
1.2.3 试验过程
在一段磨工艺流程中,球磨返砂比为112.77%,1#球按工艺流程图1装料,球磨时间7h;2#球用于二段磨工艺流程的一段球磨,3#球用于二段球磨,按工艺流程图2装料,球磨时间分别为7h和6h,其他条件按规定要求。到点后按规定要求放球、取样、测试粒度。
2 试验结果及分析
流程稳定运行一段时间,对1#、2#、3#球磨料的粒度测试结果进行归纳总结,从中找出具有代表性的一组数据,数据如下:
1#球:D50=3.65μm,D97=24.10μm,-5
μm60.38%,-10μm82.9%;
2#球:D50=3.63μm,D97=24.11μm,-5
μm60.56%,-10μm82.97%;
3#球:D50=2.73μm,D97=13.82μm,-5
μm72.89%,-10μm93.39%。
从1#、2#球的磨料粒度测试数据对比来看,
两球的磨矿效果没多大差别,说明一段球磨由磨混合料变为全部磨锆英砂,而磨矿效果、效率没多大改变;对比1#球、3#球的磨料粒度测试数据,可看出二段球磨的磨矿效果明显提高,磨料粒度:D50从3.65μm降为2.73μm,D97从24.10μm降为13.82μm,-5μm百分含量从60.38%提高到了72.89%,-10μm百分含量从82.9%提高到了93.39%。另球磨时间缩短了1h,说明磨矿效率明显提高。从一段磨矿的磨料粒度测试结果来看,5μm、10μm颗粒的含量已分别达到了60%和80%,所以一段磨料先分级而后分级沉砂用小直径研磨介质进行二段磨矿的二段磨工艺比较经济,具有高磨矿效率。
3 分段磨应用效果
超细锆微粉有限公司球磨湿法制备超细硅酸锆生产线自2004年由一段磨工艺流程改为二段磨工艺流程,产量增加,生产成本下降。按5号产品计算,产量增加6.0%,磨矿直接成本下降30元/t(改前磨矿直接成本为300元/t,改后磨矿直接成本为270元/t)。从试验结果看,试验达到了预想的结果,提高了磨矿效率,降了生产成本。另外,由于时间的缩短减少了研磨介质的磨耗,提高了产品氧化锆的含量,可以得到更纯的氧化锆珠,使产量得到提高。
4 结论
a.分级沉砂小直径研磨介质二段磨工艺与分级沉砂返回再磨工艺对比,球磨效率明显提高,磨料粒度:D50从3.65μm降为2.73μm,D97从24.10μm降为13.82μm;球磨时间缩短了1h,生产成本大幅下降。
b.在超细粉加工过程中,要充分利用分段磨和分级的优点,制定适宜的、合理的工艺,提高磨矿效率。
c.球磨机由于结构简单、机械可靠性强、产量大、容易上规模和工业化等特点,所以如对球磨机的工艺参数、加工工艺加以优化,球磨机在超细粉加工方面仍然具有很好的应用前景。