新闻中心
常用各类砂磨机设计结构原理详解
研磨粉碎设备
一、研磨粉碎简述
众所周知,疏水性粒子在水中分散比较困难,通过加工过程,能在原药粒子表面覆盖一层表面活性剂,使表面活性剂的亲水端指向外面,疏水端指向粒子。由于表面活性剂的作用,原本不亲水的粒子通过表面活性剂表现出良好的亲水性,从而达到加工目的。另外,由于粒子表面是同一形态离子的表面活性剂,也降了微小粒子相互黏结的可能性,从而改善了微粒在水中的分散性能。
悬浮剂(SC、SE、OF、LSD、DF)产品的标准中要求其悬浮率≥70%,这就要求粒子细度小于5μm,大多数粒子的粒度分布要求粒径在2μm以下。研磨粉碎设备是湿粉碎的设备。常用的研磨粉碎设备是各种结构的砂磨机。
砂磨机的粉碎过程可以认为是悬浮液与研磨介质之间各种力相互作用的结果。悬浮液、研磨介质可以看作一个研磨体系,砂磨机分散盘高速旋转产生很大的离心力,离心力使研磨介质以三种方式运动:①研磨介质与悬浮体同方向流动。由于介质间可能产生速度差,对颗粒产生剪切力;②研磨介质克服悬浮液的黏滞阻力,向砂磨机内壁冲击,产生冲击力;③研磨介质本身产生自转。如果相邻两介质的相对自转方向或速度不同,会对颗粒产生摩擦作用。由于上述三种运动和三种粉碎力(实际情况更复杂)的存在,颗粒被粉碎时少要受到两个力的同时作用。
早期使用的砂磨机为立式开放式和密闭式两种,现在逐渐为能克服介质偏析、研磨不匀、不易启动等缺点的卧式砂磨机所代替。卧式砂磨机研磨后的物料细而均匀,研磨介质为玻璃珠、砂、氧化锆珠、陶瓷珠等,直径为0.5~5mm,根据砂磨机的规格和产品粒度选定。靠它产生的剪切力将料液中的物料磨细,较粗的物料应先在预分散机等其他设备中预磨50~200目,再进入砂磨机研磨。
二、立式砂磨机
立式砂磨机又分敞开式和密闭式两种,其工作原理基本相同。研磨介质和悬浮液混合在一起,由于分散盘的高速旋转产生离心力,研磨介质和颗粒在离心力的作用下冲向磨筒的内壁,介质对颗粒产生强烈的剪切、摩擦、冲击和挤压作用,颗粒受到作用力后被粉碎。立式砂磨机的基本结构如图2-1所示。
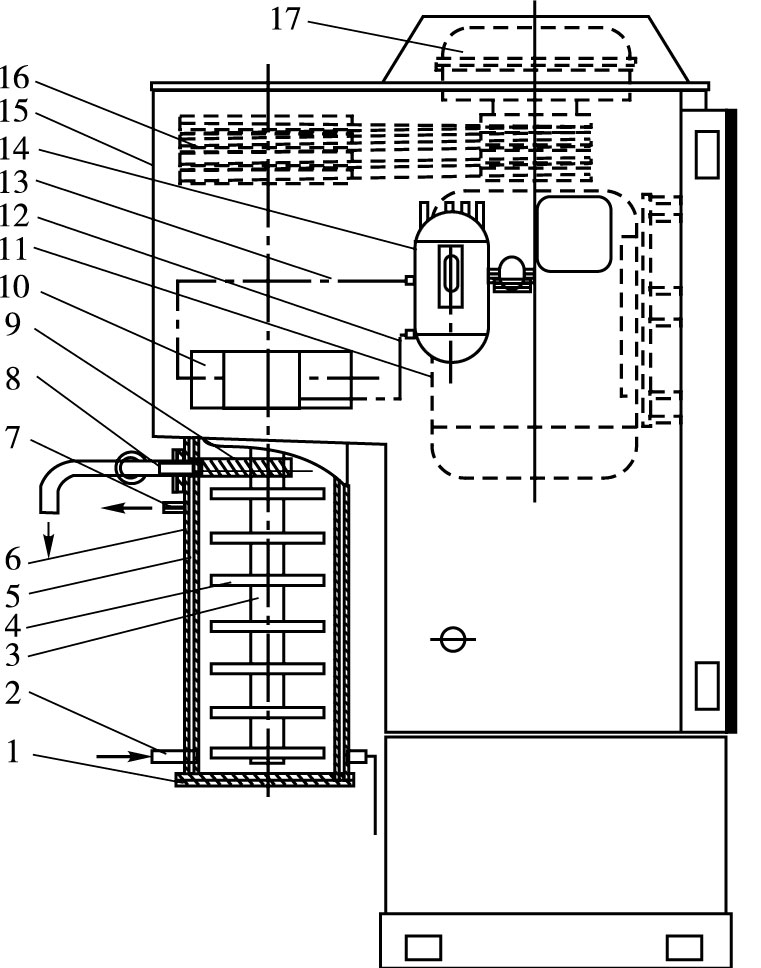
图2-1 立式砂磨机基本结构图
1—盖;2—物料入口管;3—搅拌轴;4—分散圆盘;5—研磨筒;6—夹套;7—冷却水进出口管;8—物料出口管;9—过滤网;10—机械密封;11—电机;12—密封液进口管;13—密封液出口管;14—压力罐;15—机座;16—皮带轮;17—液力偶合器
敞开式(简称开式)砂磨机截留研磨介质的金属网暴露在外面。这种结构的特点是由于分离器的筛网露在外面,研磨介质与悬浮液的分离情况可以观察,结构简单,清洗方便,维修容易,见图2-2。缺点是研磨介质填充系数小,悬浮液的水分易蒸发,在分散器高速旋转下,空气容易进入悬浮液中,产生气泡而降磨效,有时要加入消泡剂。另外,对溶剂、有毒性物料、高黏度物料的研磨也受到一定限制。
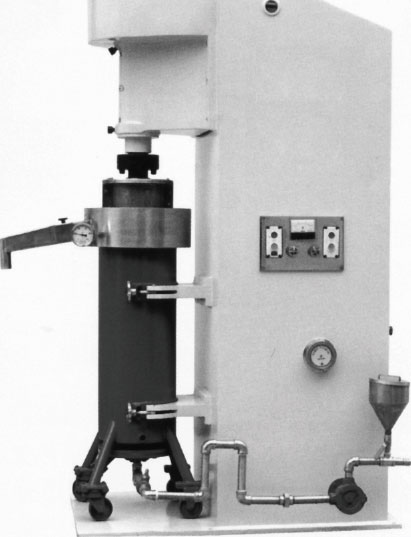
图2-2 敞开式砂磨机
密闭式(简称闭式)砂磨机分离介质的金属网伸入到磨筒内,或设间隙式动态分离器,均与外界隔开。它的优点是介质的填充系数高,可以达到70%~90%,能研磨50Pa·s的高黏度物料。与敞开式相比,悬浮液的发泡率大大降。应该说,密闭式砂磨机较敞开式砂磨机有更多的优点,见图2-3。
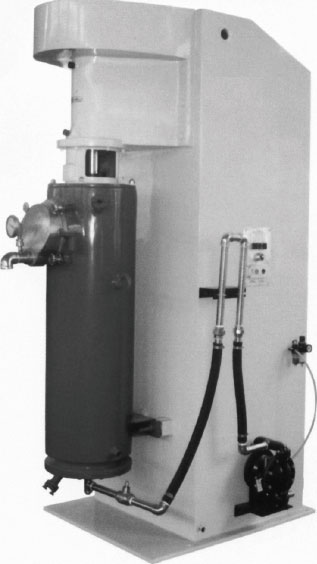
图2-3 密闭式砂磨机
三、双冷却系统搅拌棒式砂磨机
双冷却系统搅拌棒式砂磨机是德国20世纪80年代开发的新型湿式粉碎设备,适用于、颜料、涂料、磁性材料、油墨等化工产品的分散及粉碎,可以把物料粉碎到微米级。
1. 结构原理和特点
普通砂磨机因其转子外壁和定子内壁间距较大(即研磨间隙宽),磨室内的密度分布不均匀(见图2-4)。距转子外壁和定子内壁较近的地方密度较大,粉碎效果较好。反之,密度较小,粉碎作用甚微。这种密度分布不均衡的现象导致了被粉碎物料的粒度不均,且粒径分布范围较宽,粒径较大的颗粒影响了产量。此外,磨室间隙宽导致砂磨机的平均密度,为1.5kW/dm 3 左右,因而其粉碎和分散的效率都不高。
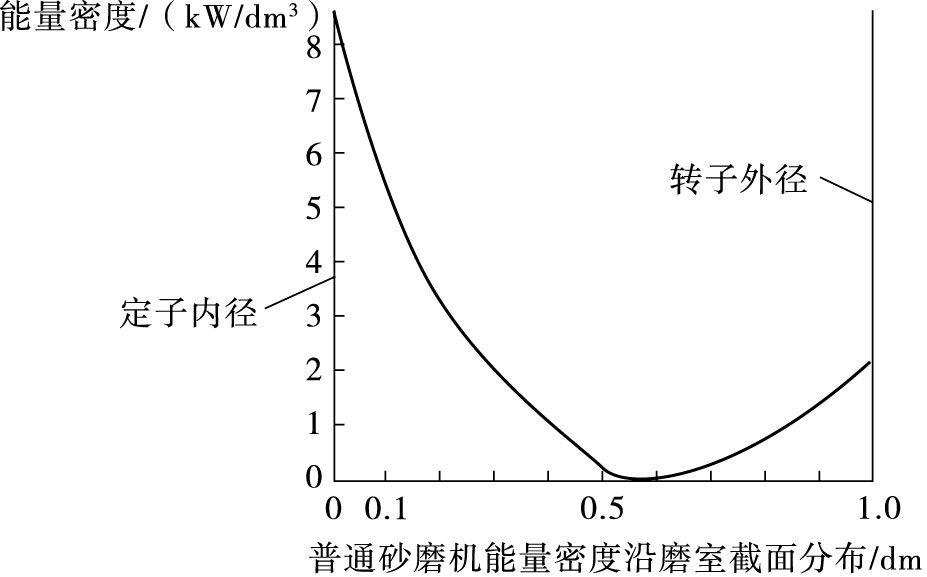
图2-4 普通砂磨机密度沿
搅拌棒式砂磨机了搅拌分散轴直径,大大缩小了转子和定子之间的间隙,使磨室内的任何部位都具有几乎相等的密度,提高了研磨、粉碎和分散效果。在该砂磨机的转子和定子上分别设置的销棒,强化了对物料的挤压、摩擦、冲击和剪切等复合粉碎作用,提高了粉碎效率和处理量,该设备外形见图2-5。
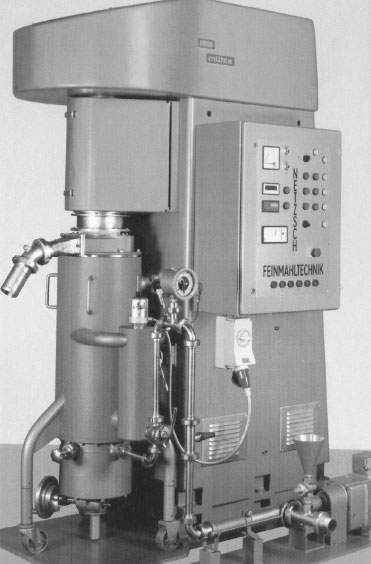
图2-5 搅
如图2-6所示,双冷却搅拌棒式砂磨机主要由转子、定子、分离装置及传动装置组成。转子是圆柱形结构,内设双冷却水通道,形成空心轴结构。在有密封盖,以物料、研磨介质及空气进入轴内,转子外壳安装有圆柱形销棒。定子是圆筒形结构,外设通冷却水夹套。在定子内侧,有序排列许多圆柱形销棒,排列位置与转子错开。分离装置设在出料口上,动态分离装置能够连续把达到细度的物料与介质分开。
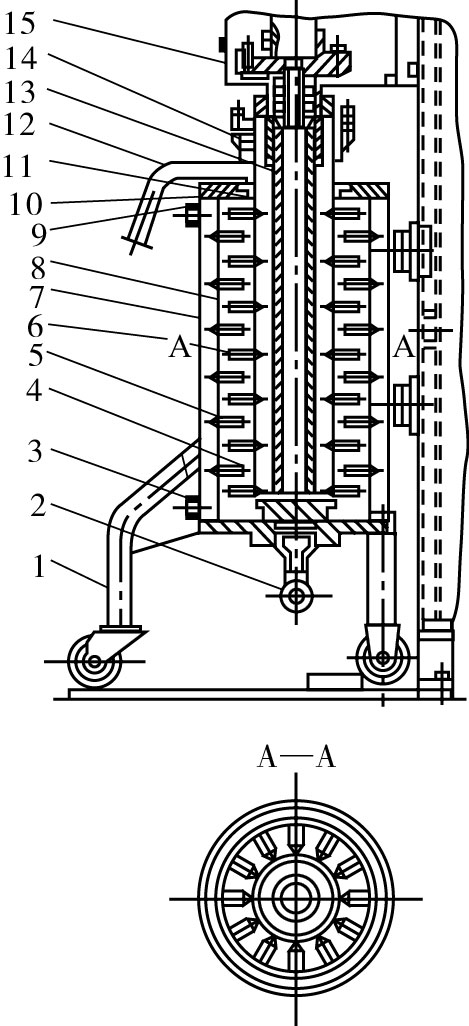
图2-6 双冷却
1—支脚;2—物料入口管;3—冷却水入口管;4—轴外套;5,6—销棒;7—夹套;8—容器;9—冷却水出中管;10—转子;11—定子;12—物料出口管;13—轴内管;14—密封填料;15—机座
转子和定子之间形成的环隙构成研磨室,进料口在研磨室底部,出料口在上部侧面,传动装置在砂磨机与转子相连。
2. 设计原理
物料的研磨和粉碎不是发生在磨室壁之间,而是在研磨介质的珠球和物料颗粒之间。搅拌分散轴设计成大直径的空心圆筒,缩小了分散轴与磨室壁之间的距离(研磨缝隙),保证了分散轴与珠球范围内的冲击速度,这样可以使磨室内的任何部位都具有几乎相等的研磨和粉碎效果。由于分散轴的高速旋转,研磨介质和颗粒在分散轴上的各组销棒力的作用下,产生了强烈的搅拌、摩擦、冲击、剪切等复合粉碎作用,其中剪切力起着主要作用。料浆包围着介质或在介质之间通过,其中固体颗粒因受上述力的作用而被研磨、粉碎,保证了研磨室内的密度均衡。靠近分散装置的区域,其密度高,密度与珠球距分散装置的距离有如下关系:
(2-1)
式中 ——密度,kW/dm 3 ;
a ——珠球距分散装置的距度,dm。
磨室内密度的均衡消除了无用功的产生,节约了能源,并使料液中的颗粒细化,粒径分布集中,从而可获得理想的微粉碎效果。
3. 工作原理
悬浮液在送料泵的作用下从底部进入研磨室,与研磨介质混合。由于转子的高速旋转,转子、定子及销棒向介质传递,使进入介质区(粒子捕获区)的物料颗粒受到来自介质的挤压、剪切、摩擦等作用,在短时间内得到粉碎。研磨介质及较大的颗粒集中在定子壁附近,在这里形成一个具有高密度的有效研磨区域。由于研磨室为环状,而且内外壁的距离较小,研磨室有很高的密度。转子、定子、销棒交错排列,介质随转子周向运动,更加提高了研磨效率。介质的高速运动,使磨室从下至上每一个平面的介质数量都基本相同,无堆积现象和研磨死角。底部进料后把已经磨细的物料从顶部经分离器排出,系统为连续工作。如入研磨介质,还可以作分散、均质之用。除了上述优点以外,搅拌棒式砂磨机还有如下特点:
① 在筒形分散轴(转子)和磨室壳体(定子)的夹套内分别设计了冷却水流道结构,从而保证了磨室能在较温度下操作,能适应热敏性物料和熔点较物料的粉碎。
② 与普通砂磨机相比,磨室内研磨介质少,从而减少了物料黏附在介质上的黏附量,更换物料时减少了物料的浪费,提高了经济效益。
③ 物料在密闭系统中连续操作,料浆不易起泡。当研磨、粉碎有毒有害物料()时,减少了液体挥发,改善了劳动条件,了劳动强度。
④ 全套装置结构紧凑,占地面积小,有利于安装。
4. 使用方法
根据实际需要,亦可进行多次操作。此时,只要把从磨筒上部物料出口处排出的物料返入砂磨机旁的容器中,使物料在系统中,直至产品达到预定的要求。系统出料后再加入新的料液进行下一批操作。
四、卧式砂磨机
卧式砂磨机的磨筒水平放置,搅拌轴在磨筒中心也水平布置,外形见图2-7。它的工作原理与立式砂磨机基本相同。卧式砂磨机除具备立式砂磨机的优点外,同立式砂磨机比较有如下优点:经研磨的实验表明,同体积的卧式砂磨机比立式砂磨机的生产能力高出2倍左右;卧式砂磨机的启动功率,消耗功率也于立式砂磨机。但卧式砂磨机的轴承、密封、分离器的磨损较严重,加工制造对材料的要求都很高。图2-8是卧式砂磨机的结构简图。根据不同物料的性质,设计出多种结构的分散盘,图2-9是砂磨机常用分散盘的实物照片。
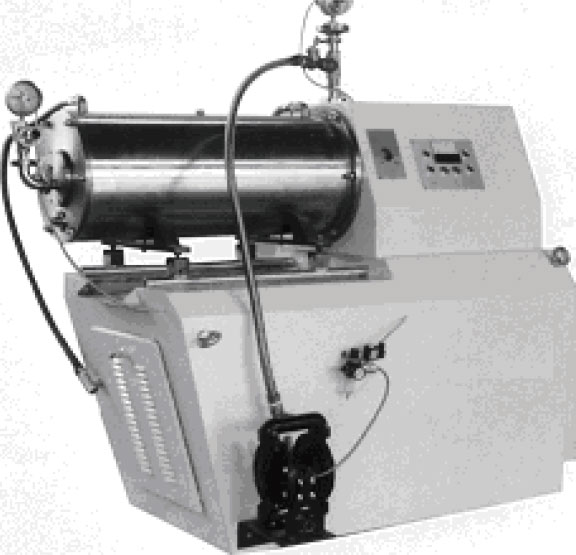
图2-7 国产卧式砂磨
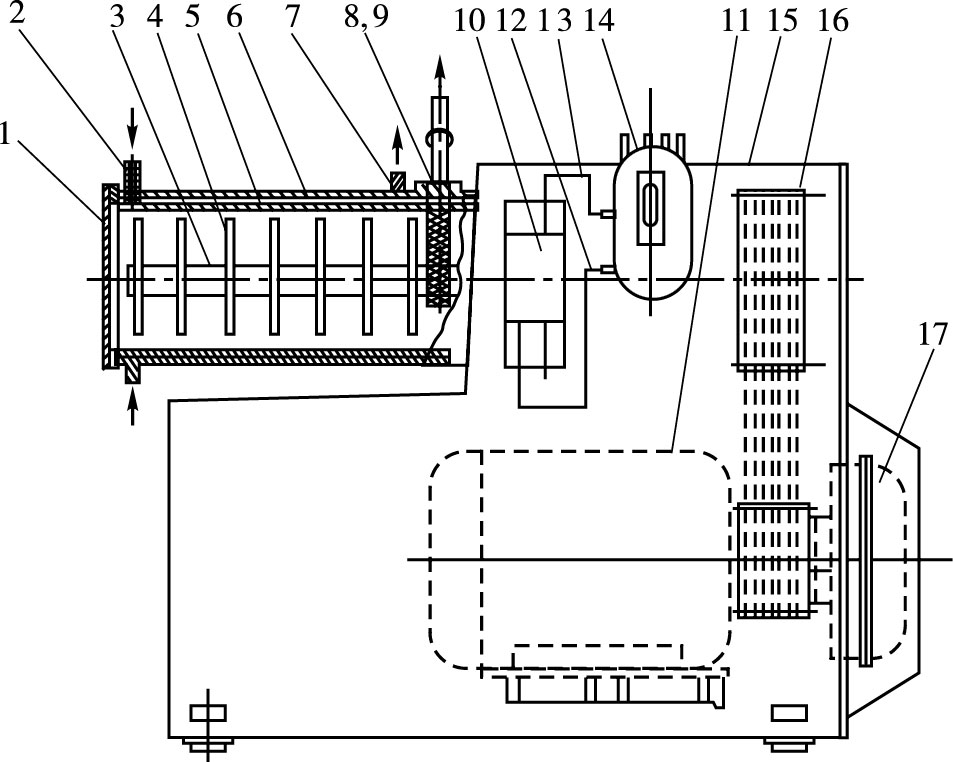
图2-8 国产卧式砂磨机结构简图
1—盖;2—物料入口管;3—搅拌轴;4—分散圆盘;5—研磨容器;6—夹套;7—冷却水进出口管;8—物料出口管;9—过滤网;10—机械密封;11—电机;12—密封液进口管;13—密封液出口管;14—压力罐;15—机座;16—皮带轮;17—液力耦合器

图2-9 卧式砂磨机常用分散盘的实物照片
表2-1是国产卧式砂磨机主要技术参数,表2-2是德国耐驰精研磨技术有限公司制造的卧式砂磨机主要技术参数。
表2-1 国产卧式砂磨机主要技术参数
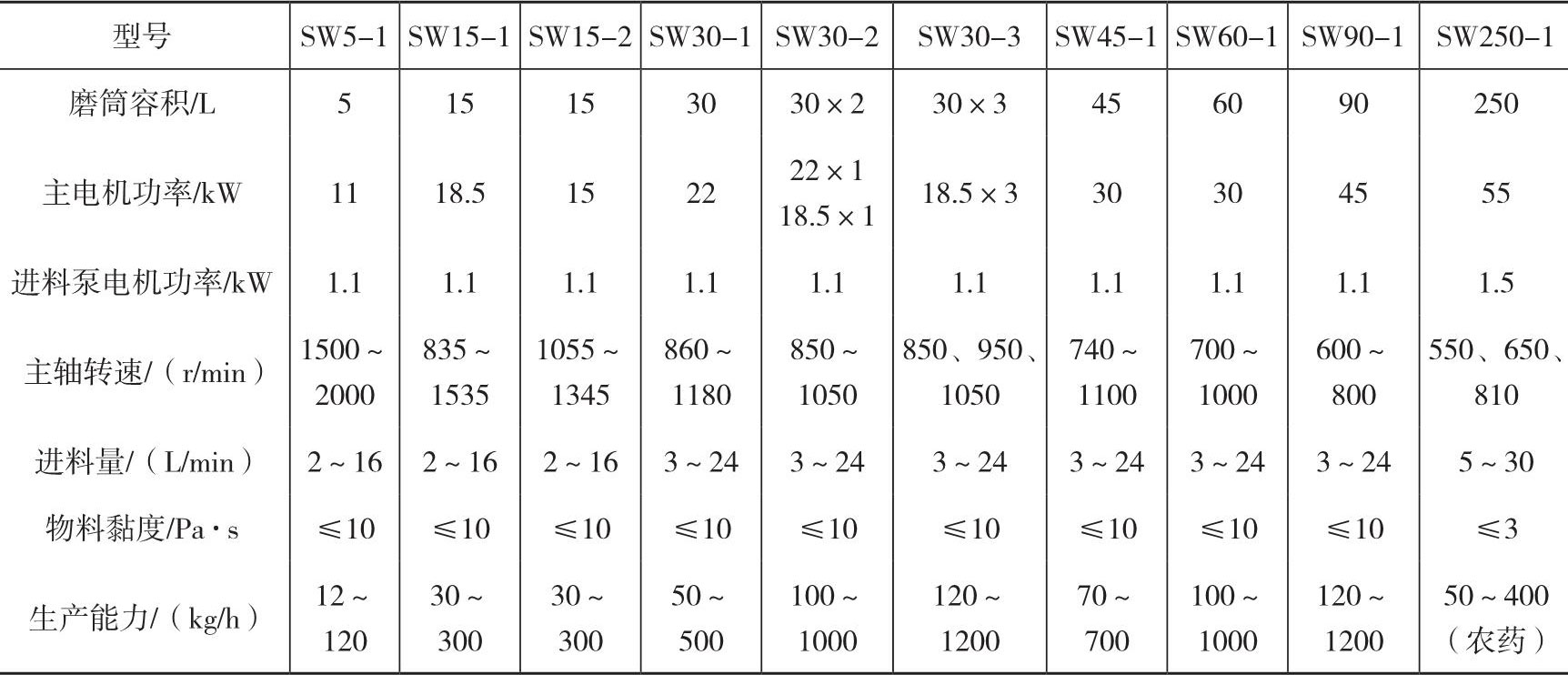
表2-2 德国产卧式砂磨机主要技术参数
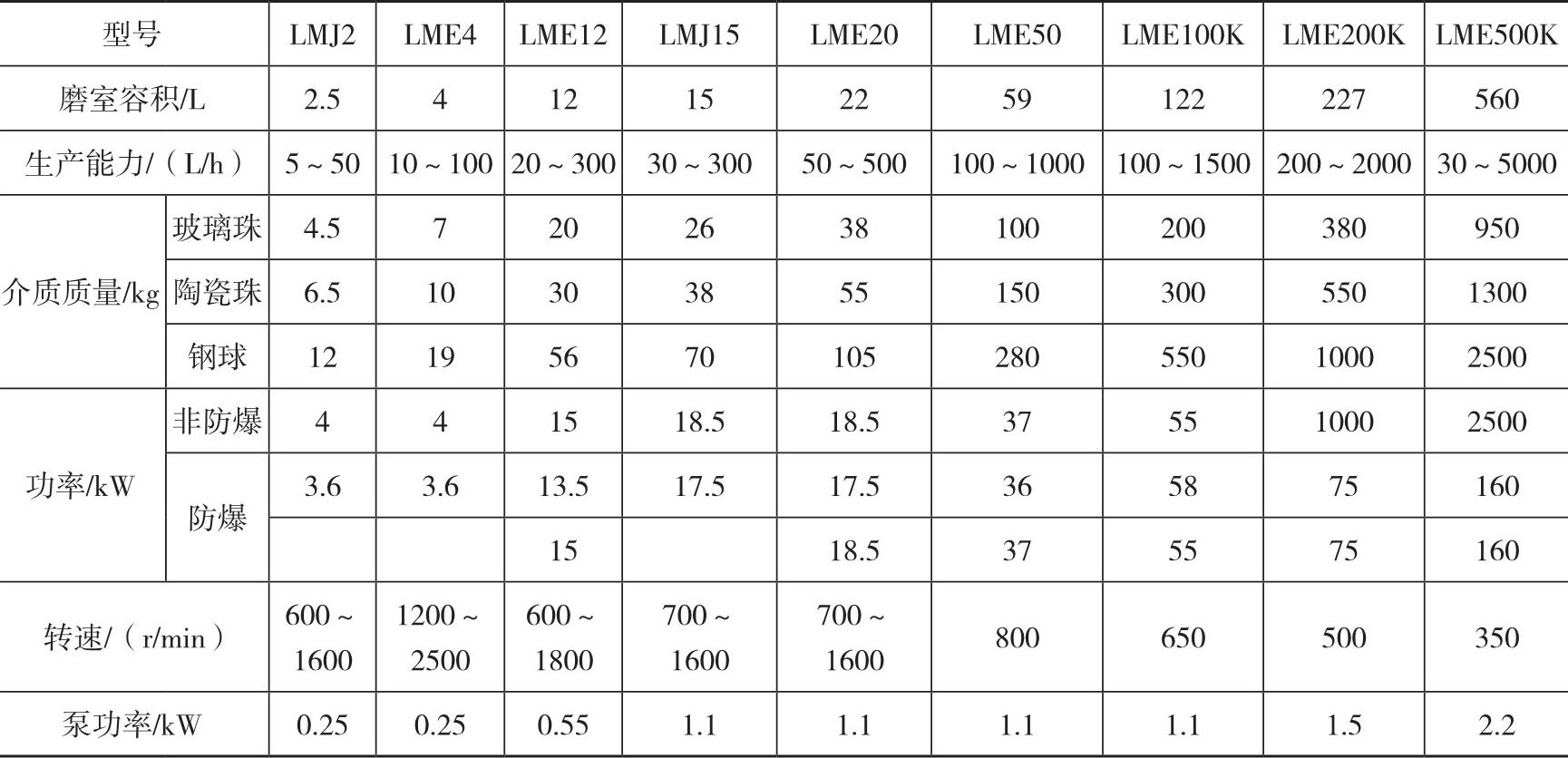
图2-10是耐驰精研磨技术有限公司制造的卧式砂磨机。这种砂磨机一改主轴带分散盘的结构,而是在加粗的主轴上安装有销棒而形成转子,筒体内壁也安装有固定的销棒而形成定子。转子和定子的销棒交错排列,研磨效率很高,该砂磨机转子端面结构见图2-11。
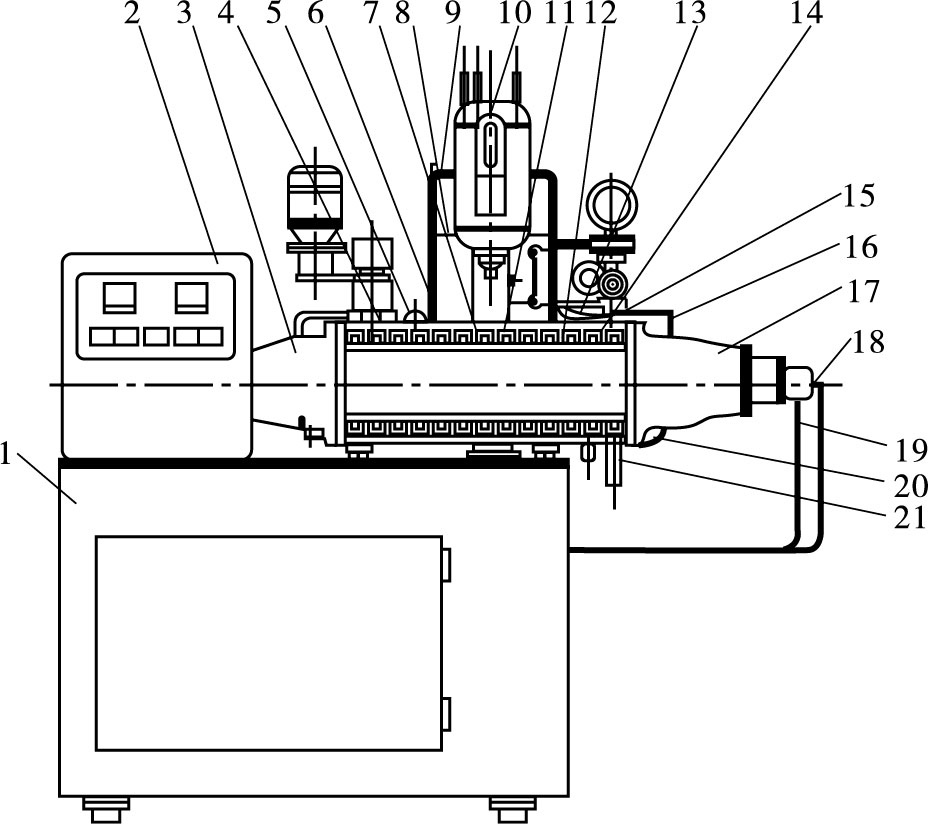
图2-10 耐驰精研磨技术有限公司制
1—机座;2—仪表盘;3,17—机械密封;4—物料出口管;5,18—冷却水出口管;6,7—销轴;8,9,16,20—密封液进出口管;10—压力罐;11—轴内管;12—轴外套;13—夹套;14—容器;15—物料入口;19,21—冷却水入口
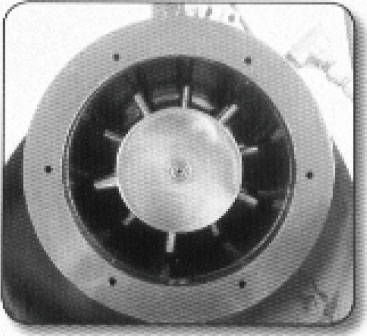
图2-11
五、涡轮砂磨机
砂磨机的粉碎主要发生在研磨介质之间以及研磨介质与器壁的接触区域。在摩擦、碾压、剪切等力的作用下夹在研磨介质之间或研磨介质与器壁之间的固体颗粒被粉碎。但因传统砂磨机一般为圆筒形结构,分散盘带动研磨介质,因此研磨效果十分有限。而涡轮砂磨机增加了研磨介质与机体的摩擦面积,从而提高了研磨效率。
此砂磨机的外壳为卧式圆筒形结构,但在水平放置的圆筒式主轴上,串联若干个涡轮式加速器,这是提高研磨效率的主要原因,见图2-12。表2-3是涡轮砂磨机主要技术参数。
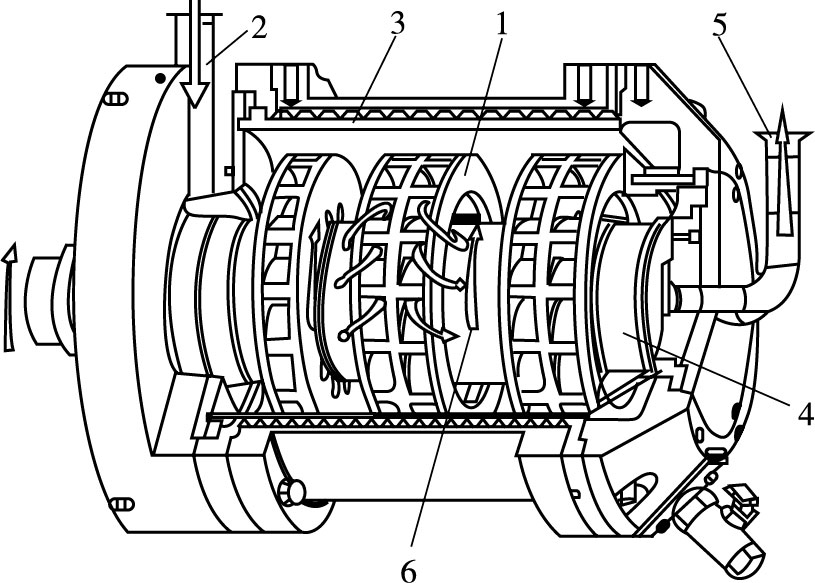
图2-12 涡轮砂磨机
1—涡轮加速器;2—物料和研磨介质入口;3—研磨筒体;4—动态分器装置;5—产品出口;6—介质路径
表2-3 涡轮砂磨机主要技术参数
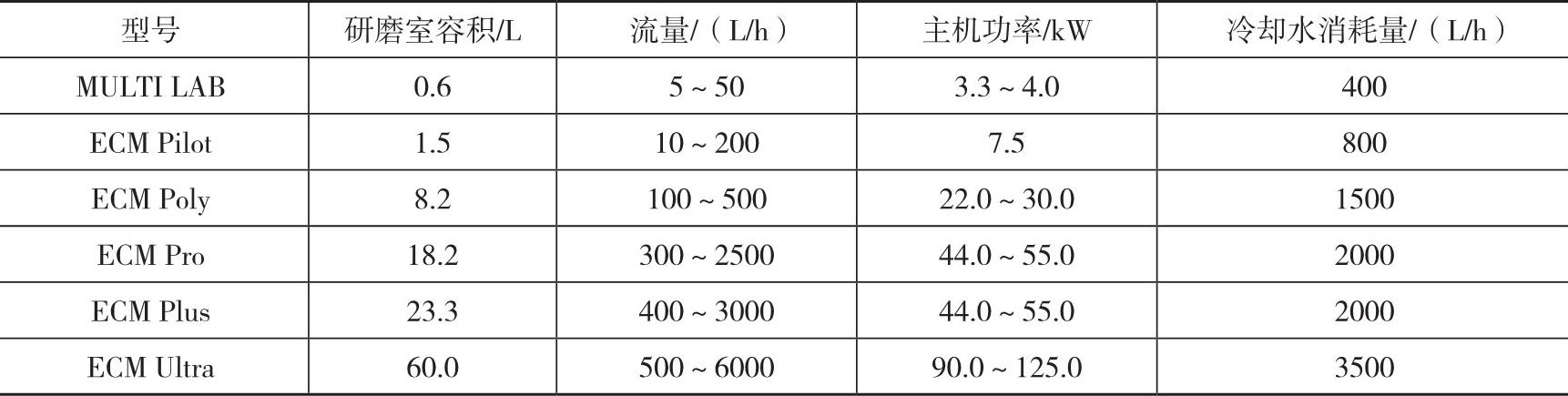
工作时,液体悬浮剂与研磨介质充满于研磨筒内,在加速器的内外均充满研磨介质,在离心力的作用下,高速旋转的加速器将研磨介质高速甩出并冲向器壁,研磨介质在运动过程中,与加速器和外筒内壁均有撞击和摩擦效果,加快了物料的粉碎。加速器使更多的研磨介质增加了冲击,也强化了粉碎作用。
研磨介质在研磨室里经过涡轮加速器进行加速,基于砂磨机磨室内的优化设计,内部涡轮的研磨介质将在较短的时间里达到高的密度,这种涡轮的研磨介质在强度和速度上都要比平流运动效果大几倍。涡轮式砂磨机有如下特点:
① 涡轮加速器确保了研磨介质的高、均匀的运动,从而保证了高磨效;
② 理想的通道式和式生产工艺,连续不断的高效能实现了粒径分布窄;
③ 使用高质量的材料(碳化硅、氧化锆、硬铬合金)确保了更长的使用寿命;
④ 高效的转换降了能耗;
⑤ 较小的研磨容积和理想的冷却效果确保了对温度敏感产品的顺利研磨。
六、三室砂磨机
在粉碎过程中,颗粒要经过粗分散、细分散和超细粉碎几个阶段。按照砂磨机分散、粉碎的特点,研磨介质直径应由大到小逐级改变才能得到的粉碎效果。基于这个规律,国内开发出SW30×3三室卧式砂磨机。
SW30×3三室卧式砂磨机是具有三个水平磨室的研磨设备,由主机、传动系统、供料系统及电器等部分组成。主机装有密闭工作室,筒体的径长比为1∶2.5,在工作室内部有分离装置,结构如图2-13所示。
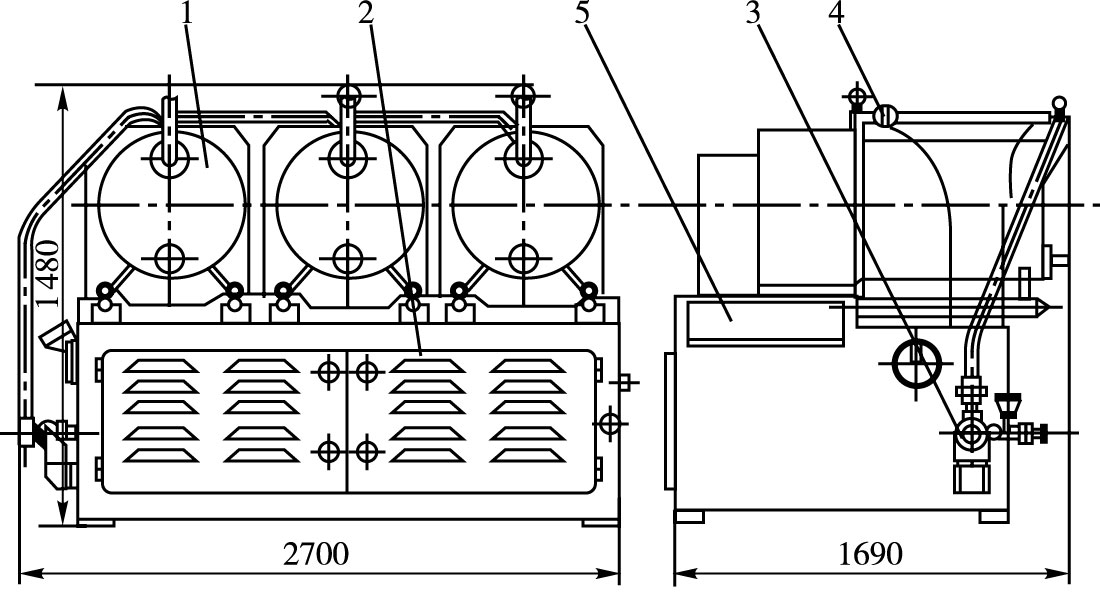
图2-13 SW30×3三室卧式砂磨机
1—主机;2—机身;3—加料系统;4—冷却系统;5—控制盘
电机通过液力耦合器把动力传递给主轴,物料由无级变速器带动齿轮泵,悬浮液依次通过三个磨室,砂磨机通过圆筒鼓形筛圈出料。筛圈的薄处为4mm,出料面积为25.2cm 2 。为了保证砂磨机的正常运行,该机装有压力和温度自控连锁装置,设定压力为0.1MPa,采用自动控制技术。分散盘也设计成螺旋形结构,强化了研磨效果。
悬浮液通过齿轮泵送入磨室,分散盘的转动使研磨介质与物料颗粒间产生研磨作用。一磨室的作用是将粗大颗粒打碎并使其分散,需要较大的撞击力,因此装有较大粒径的研磨介质,一般使用直径为4mm的研磨介质。较大的团块被分散后物料进入二磨室,同理二磨室改用直径为3mm的研磨介质,同时,分散盘的转速较一磨室提高20%。三磨室为超细研磨,因而介质直径还要减小,采用直径为2mm或更小的介质,同时,转速比二磨室提高20%,经过三个磨室的物料能够达到细度要求,后经分离出料。
七、Coball Mill砂磨机
Coball Mill砂磨机是FRYMA机械有限公司开发的产品。砂磨机的磨室是转子与定子间形成的锥形环隙,工作时磨室具有几乎相等的密度,克服了其他传统砂磨机密度宽的缺点,在粉碎中具有广阔的应用前景。
(一)结构原理
Coball Mill砂磨机的结构及工作原理如图2-14所示,主要由转子、定子、冷却室、动态分离器、主轴等组成。带冷却室的定子和转子构成的缝隙就是研磨室,动态间隙分离器在磨室的上端,从底部进料,上部出料。
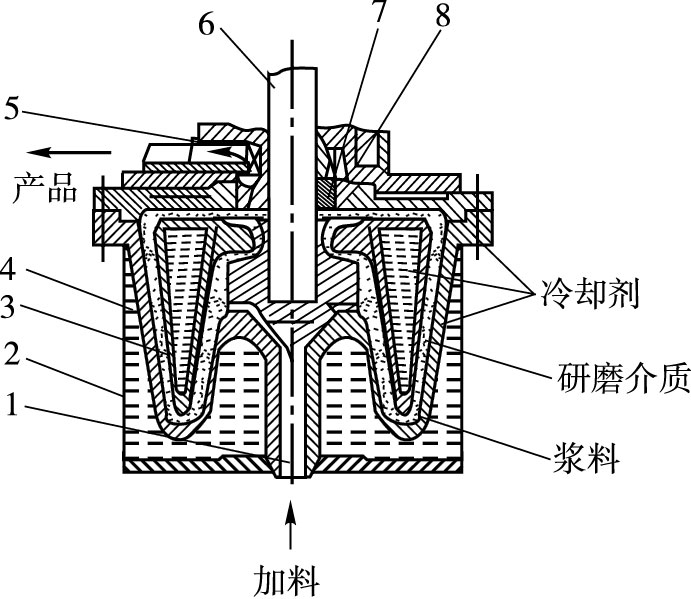
图2-14 Coball
1—加料管;2—容器;3—转子;4—定子;5—料液出口管;6—旋转轴;7—转子环;8—定子环
转子、定子及上盖等与介质接触的表面均采用硬质合金或高耐磨防护层,这些防护层容易更换。MS-32以上规格均设有水压装置(水的压力为0.2~0.6MPa),保证快速打开或关闭机器,以方便维修或清洗。当需要调节线速度时,通过改变传动比来完成。动态分离器能够连续把物料与研磨介质分开,以防介质流出机外。分离器的间隙不大于介质直径的1/3,进料采用两种输料泵,当输送溶剂时用齿轮泵,输送悬浮剂时用Mhoo泵。进料速率由一个接触型压力表控制,一般进料压力限制在0.1MPa。
悬浮液经进料泵送入研磨室,研磨室装有一定数量的研磨介质。转子的转动带动介质在悬浮液中高速旋转,由于磨室很小,磨室中有相当高的密度,物料在短时间内得到粉碎。因底部不断进料,被粉碎后的物料向上运动,经动态分离器分离排出机外。
(二)主要技术参数
1. 砂磨机的主要技术参数
Coball Mill砂磨机目前共有五个型号,主要技术参数见表2-4。
表2-4 Coball Mill砂磨机主要技术参数
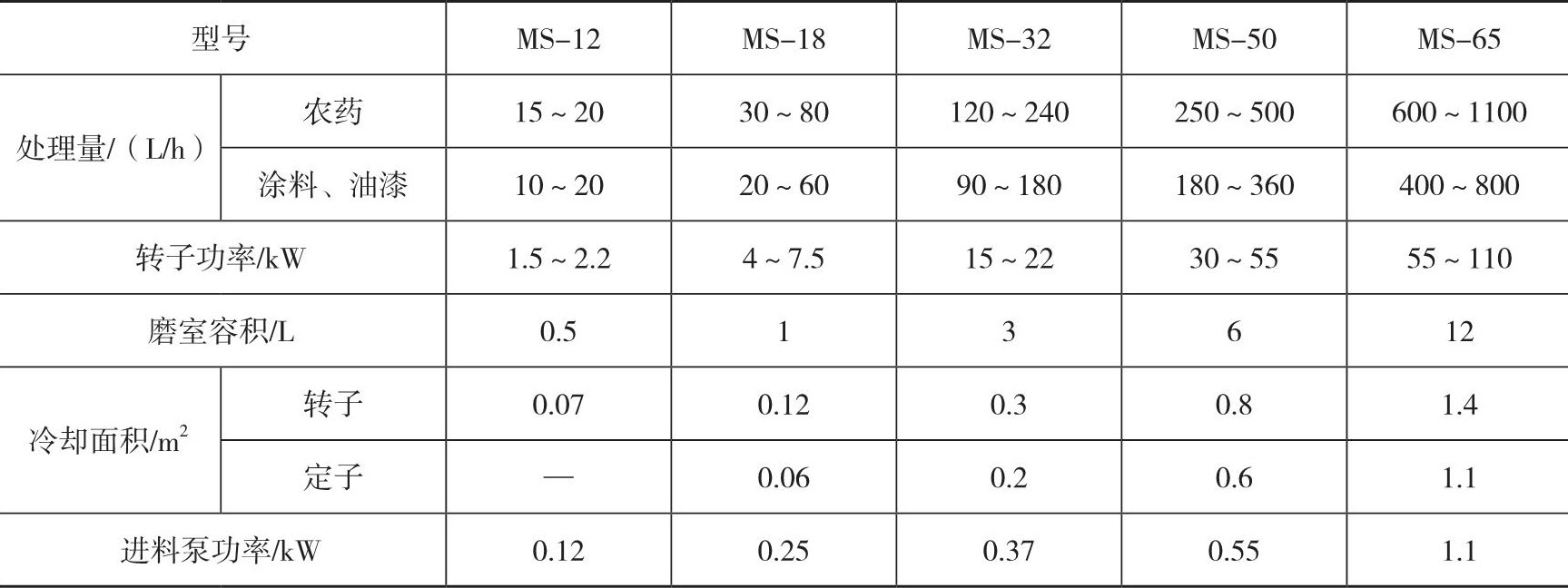
2. 研磨介质的选择
不同的磨室装填不同的研磨介质,磨室容积大,相应的介质直径也大。研磨介质直径与磨室间隙的关系见表2-5。
表2-5 研磨介质直径与磨室间隙的关系
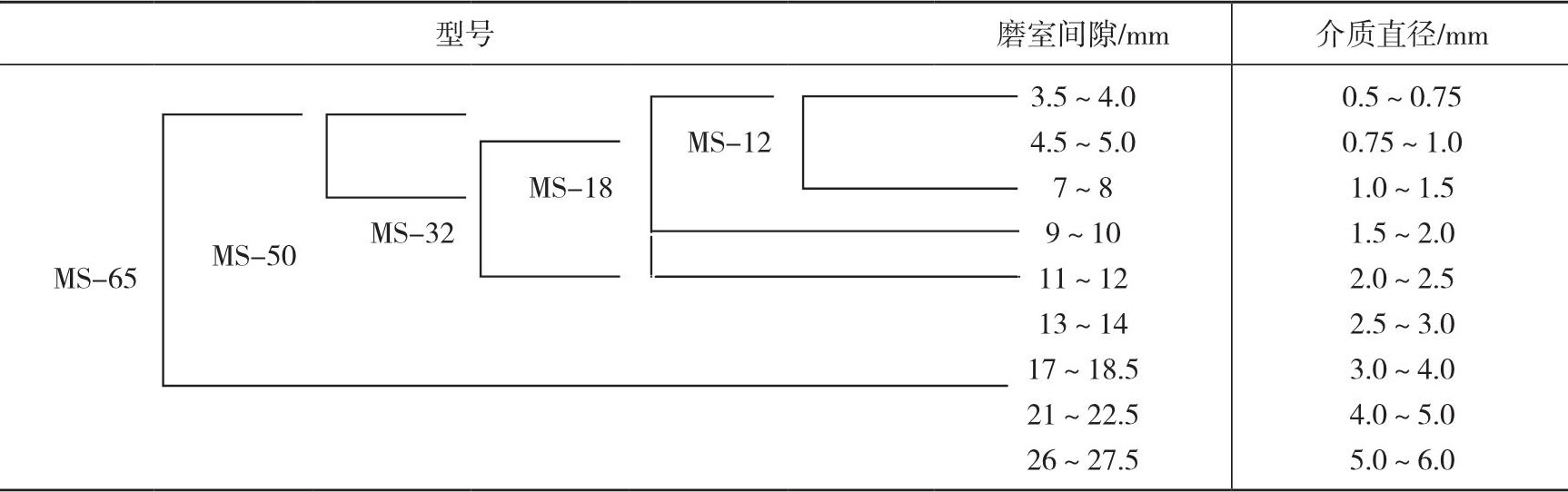
注:表中虚线表示参考值。
3. 介质填充率
本砂磨机的研磨介质可以用强化玻璃珠、钢珠及氧化锆珠等。介质填充率为理论磨室容积的60%~80%,见表2-6。
表2-6 砂磨机与研磨介质的参数
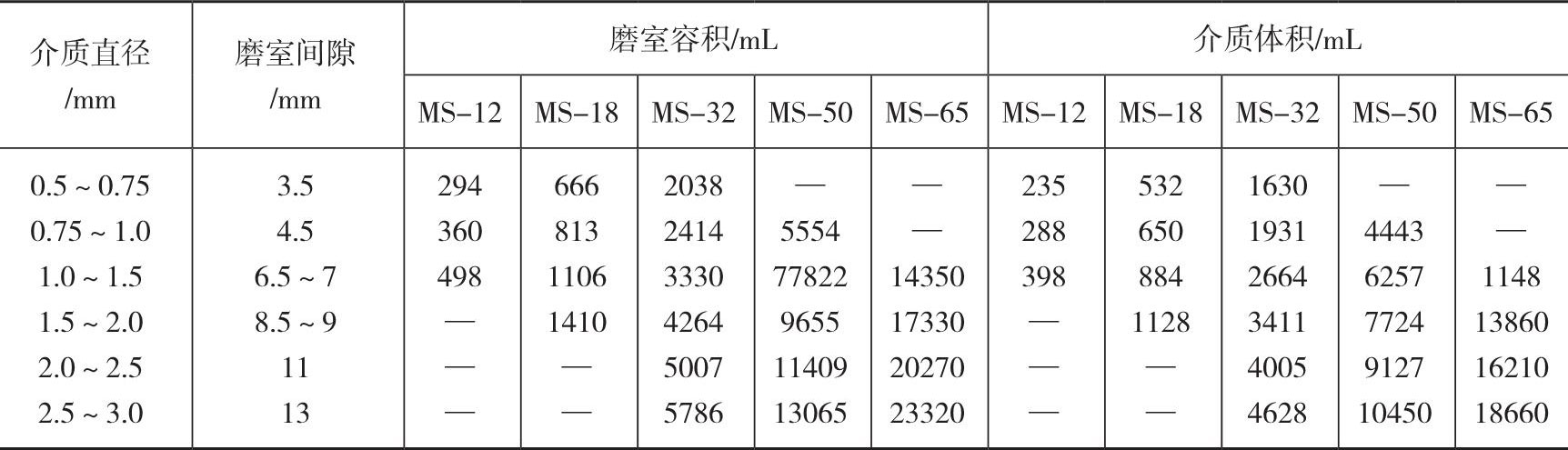
4. 砂磨机转子转速
砂磨机转子的线速度是影响研磨效率的主要因素,Coball Mill砂磨机采用无级调速的方法,可根据物料温度情况调节转子转速,见表2-7。
表2-7 Coball Mill砂磨机主要技术参数

(三)Coball Mill砂磨机的特点
1. 密度高
一般砂磨机主要缺点是密度不均匀,不会造成更多的能源浪费,也会造成产品的粒度分布宽。Coball Mill砂磨机利用锥形研磨区域,对被研磨物料所施加的研磨在从进口至出口的全过程中逐步增加,不密度高,而且效率也很高,使产品粒度分布窄。图2-15是该砂磨机与普通砂磨机分布的对比。
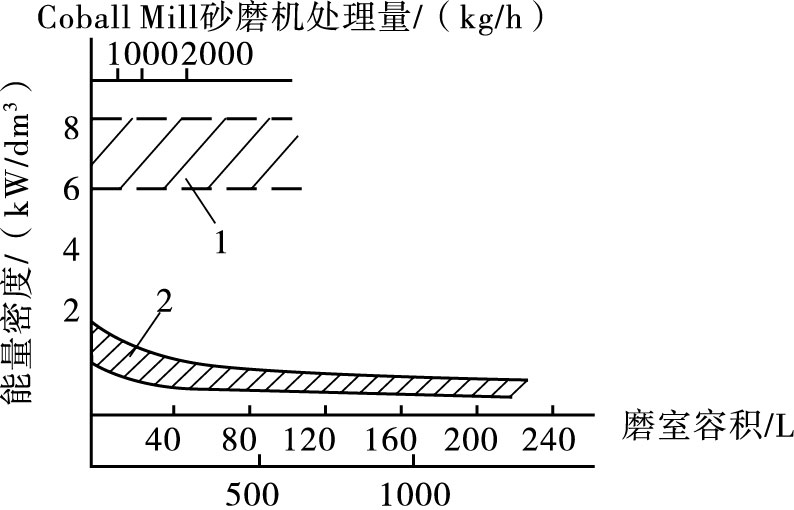
图2-15 密度沿径向分布的对比
1—Coball Mill砂磨机;2—普通砂磨机
2. 生产能力大
在相同处理量的情况下,普通砂磨机磨室容积比Coball Mill砂磨机要高3~5倍,因而后者节省研磨介质,降了研磨介质的用量,也降了操作费用,并减少物料中杂质含量。
3. 冷却性能好
是热敏性物料,研磨介质的相互摩擦要产生大量热量,致使悬浮液温度上升,这些热量不及时排出会造成重新凝聚,使粉碎无法进行。Coball Mill砂磨机比其他砂磨机有更大的冷却比表面积(冷却面积与磨室容积之比),可以控制物料研磨时的工作温度,图2-16是Coball Mill砂磨机与普通砂磨机冷却面积与磨室容积的比值曲线。
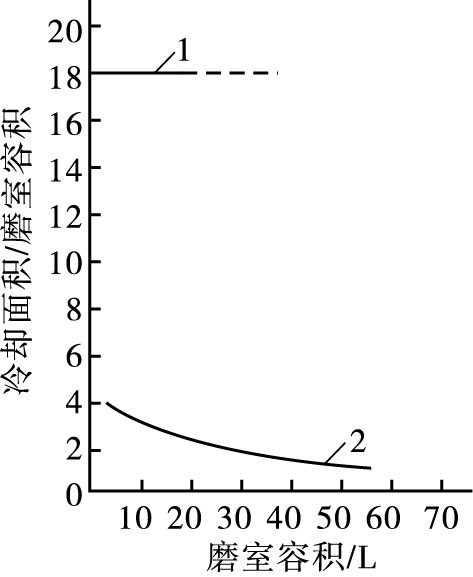
图2-16 冷却
1—Coball Mill砂磨机;2—普通砂磨机
八、PM-DCP型砂磨机
PM-DCP型砂磨机由原联邦德国的Drais公司制造(国内称砂磨机)。该砂磨机适用于多种精细化学品的湿式粉碎,能够将200µm的物料粉碎到1~2µm,是当今世界上较理想的湿式粉碎设备之一。
1. 砂磨机的结构
同前面几种砂磨机一样,PM-DCP型砂磨机也是由转子、定子、分离装置、液压系统及控制系统组成。转子是一个倒置的筒形结构,在筒壁的内外两侧有序排列许多圆柱形销棒,向介质和物料传递。定子呈双层筒型结构,两个相对内壁也排列销棒,位置与转子交错布置。分离装置在砂磨机的定子内侧上方中心出料口处,以使悬浮液和介质分离。转子把定子分成内外两个环形空间,故形成了内研磨室和外研磨室。两研磨室在底部及上部设有通道,进料口在外研磨室上方。图2-17是该砂磨机的结构图,图2-18是该设备的外形图。
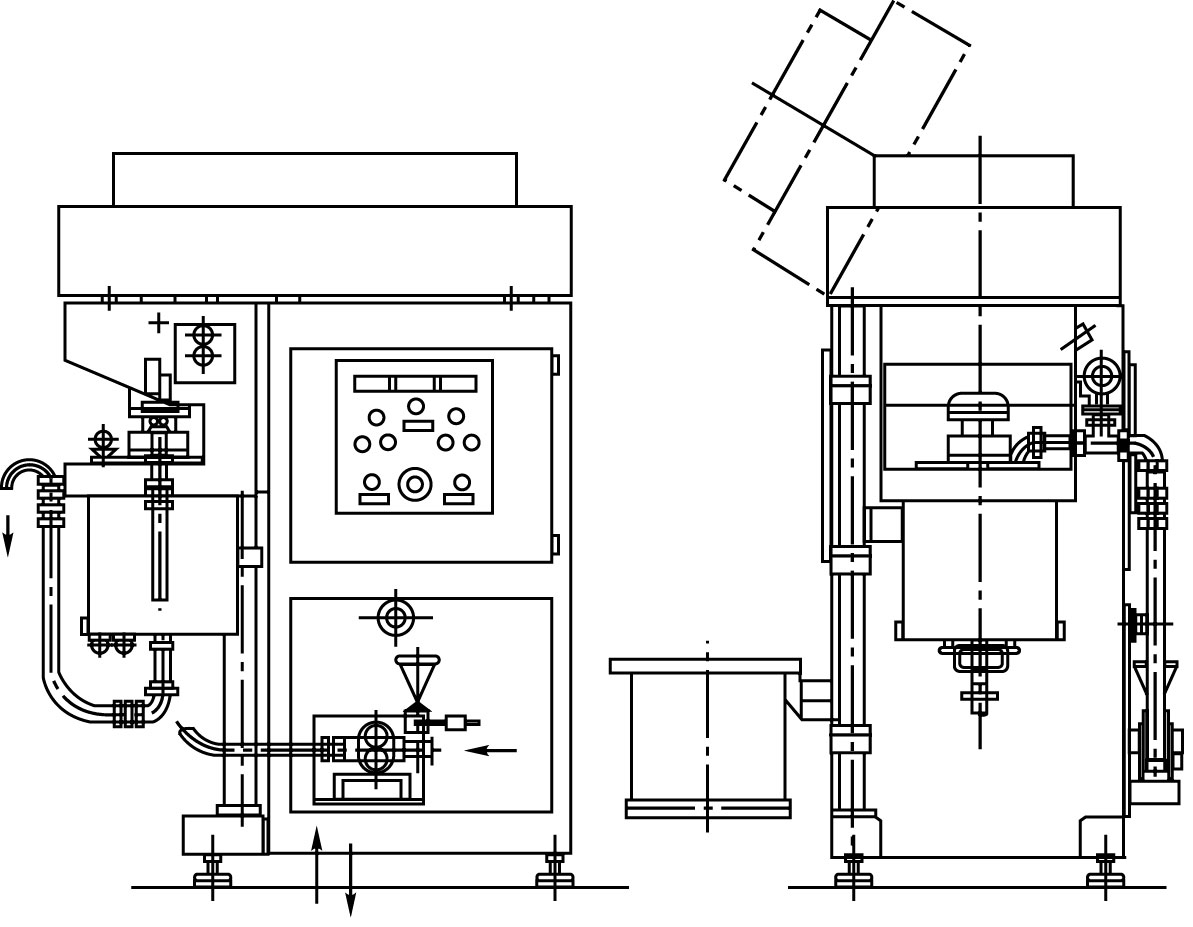
图2-17 PM-DCP型砂磨机结构图
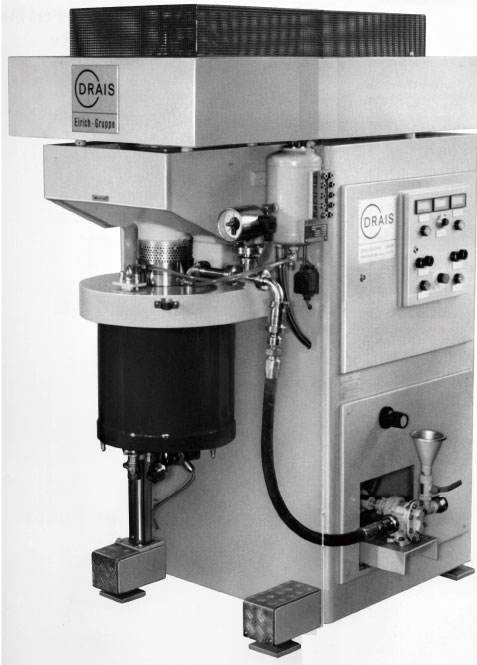
图2-18
2. 工作原理
悬浮状物料与研磨介质在磨室中混合,转子、定子的销棒强烈冲击研磨介质,介质产生高速紊乱的运动造成撞击,相互剪切、撞击和摩擦使物料被粉碎。物料从外研磨室由上向下经底部通道进入内研磨室。在内研磨室自下向上流动,后经分离器与介质分离后排出砂磨机外。研磨介质主要集中在外研磨室,因此外研磨室是粉碎的主要区域,图2-19是该砂磨机的工作原理图。
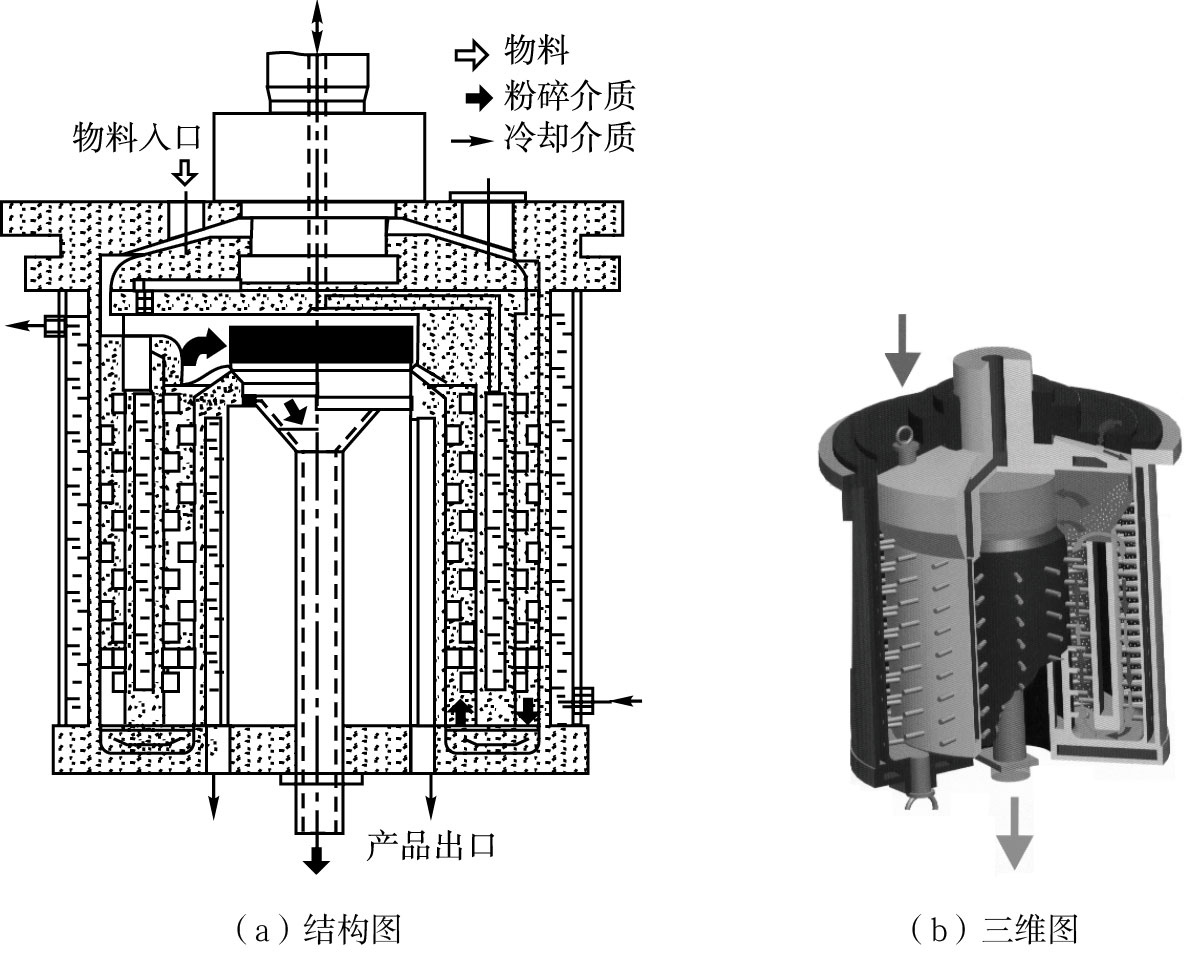
图2-19 PM-DCP型砂磨机工作原理图
3. 设备特点
PM-DCP型砂磨机有如下特点:
① 砂磨机巧妙地运用了离心力作用,排出来的物料很少带出研磨介质。
② 密度高,产品粒度分布窄。
③ 物料经过由外室向内室的外上→外下→内下→内上的运动,延长了物料在机内的运行路径,使设备结构紧凑,生产能力大。一台容积有6L的PM-DCP型砂磨机,生产能力与一台250L的普通砂磨机相当。
④ 定子由液压系统控制,可以进行升、降、转动,操作方便。
九、间隙式砂磨机
谋求更高的密度、更大的冷却比表面积是开发新型砂磨机的目的之一。对更高颗粒细度的要求导致使用更小的研磨介质,并因此产生更高成本的分离装置。
20世纪80年代出现于市场的新型间隙式砂磨机便是专门满足工业上这些高设计要求的。使用更小的研磨介质并使之处于更高的离心力场中。因此具有下列优点:
① 提高了惯性,尽管研磨介质质量更小,也能明显改善研磨效果。
② 改善了分离效果,这是因为有更高的离心力作用于研磨介质,使之更易脱离被研磨的物料。
间隙式砂磨机的特点在于其有一个以研磨室内两壁为界的特定的狭窄间隙,在此间隙里研磨介质和物料相互平均以10~16m/s的剪切速度运动。借助于0.2~3mm的研磨介质先可利用其处于运动状态的表面对物料进行碾压,其次还可借助搅拌销棒或凸轮加强研磨效果。研磨室的任何一段位置都能满足这一要求,即两壁之间的小距离应比研磨介质的平均直径大4~5倍。这是研磨介质挤压和挤碎的必要条件。这种间隙式砂磨机的特点是其研磨介质小、耐磨强度高、利用率高,图2-20示出其结构。
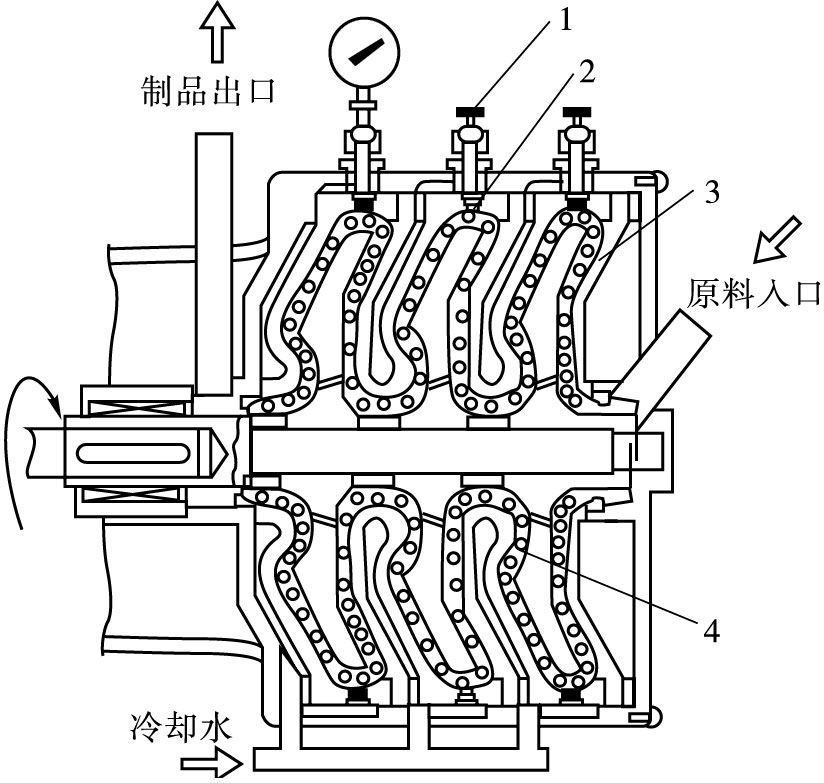
图2-20 多室间隙式砂磨机结构
1—孔盖; 2—研磨介质; 3—定子; 4—转子
这种新型间隙式砂磨机是在窄的间隙中进行研磨操作的,并在其每个粉碎室中都设有一个研磨介质的内返混通道。操作时离心力阻止了研磨介质,并锁闭分离装置。设置在每一粉碎室中的研磨介质内返混通道在研磨时可将大部分随物料曳走的研磨介质重新输送回原先的研磨区域。
同时,作用于返混通道的离心力还了研磨物料由前研磨区域向磨机出口运动时的短路现象,致使物料强制通过被称为间隙的研磨区域。环绕整个研磨区域的冷却室可将研磨过程产生的热量完全散发掉,因此对一些热敏性物料也可以进行粉碎加工。
该磨机在一个整体中设置了多个研磨室并以相同的动力传动操作。标准型是三个研磨室,故其粉碎的经济性也得到提高。根据颗粒尺寸的减小和黏度的增加,每一单体研磨室可以配置直径尺寸各不相同的研磨介质,并选择不同的研磨介质充填率进行操作,具体指标如下:
一研磨室:研磨介质直径 φ 1.5mm,充填率65%;
二研磨室:研磨介质直径 φ 1mm,充填率60%;
三研磨室:研磨介质直径 φ 0.5~0.75mm,充填率50%。
这种设计思想可使每个研磨室均有其表面光滑的界面,这样就可使磨机无须因更换物料而拆卸清洗。只要转动整台磨机,通过接口就可注入或排出清洗液体。
同样,有选择地使较大颗粒截流在这一研磨区域内并通过返混道与研磨介质一起进行回流,同时可起到分离的作用。
间隙式砂磨机有如下特点:① 该砂磨机有较大的冷却面积,可以控制磨室温度,特别适用于等热敏性物料的研磨粉碎;② 磨机清洗方便,适用于需经常更换品种的操作;③ 三个磨室配以不同直径、不同装填量的研磨介质,使操作更合理,降了能耗;④ 磨室为间隙式,密度高而且分布均匀,产品粒度分布窄,从而保证了产量。