新闻中心
烧结温度对氧化锆陶瓷研磨球性能的影响
作者:admin日期:2020-05-12阅读
自20世纪70年代,澳大利亚Gavrie教授发现了氧化锆陶瓷的相变增韧机理以来,氧化锆陶瓷在多种结构陶瓷和功能陶瓷中获得了其广泛的应用,已经成为次于氧化铝陶瓷,用量处于二位的结构陶瓷材料。氧化锆陶瓷研磨球是氧化锆陶瓷中一类用量很大、应用面很广的产品,被广泛用于陶瓷、建材、化工、涂料、电子、机械、食品、医药、化妆品等许多行业。由于氧化锆材质本身具有优异的高硬度、高强度、高韧性、高耐磨、高耐腐蚀以及体积密度大、研磨效率高等特性,因此氧化锆陶瓷研磨球除了在氧化锆类陶瓷粉体研磨中大量使用外,在其他电子陶瓷粉料,磁性材料粉料、高技术结构和功能陶瓷粉料、日用陶瓷色料和釉料,化工和各类涂料,机械抛光用粉料,医药和食品粉剂的超细研磨中也发挥了为重要的作用,对于减少被研磨物料中杂质引入和提高研磨和分散效果更是其他研磨介质所无法比拟的。同时在一些特殊的超细粉体研磨设备如搅拌磨机、砂磨机、高速振动磨机等新型设备中氧化锆珠已成为可用的产品。尽管其价格很高,但由于其磨耗,对被研磨物料的研磨和分散效果好,无需时常补加料,因此综合使用成本仍相对较,使用领域也不断扩大。在许多领域正在逐渐代替氧化铝、硅酸错、玛瑙等研磨介质球。
烧结工艺是生产陶瓷制品关键的环节之一,对陶瓷材料的微观结构和性能起着重要作用。陶瓷坯体经烧结后其物理、化学性质均发生改变,决定了终制品的性能,而烧结过程中重要的工艺参数是烧结温度的确定”·”。本文重点研究烧结温度对滚制成型氧化锆陶瓷研磨球体积密度和耐磨性的影响。
1氧化锆陶瓷研磨球的制备及其性能测试方法
1.1氧化锆陶瓷球坯的制备
采用中位径为(摩尔分数)3.75林m的亚微米级3%YZO。一z心2(摩尔分数)陶瓷粉体为原料,用滚制成型法制备氧化锆陶瓷研磨球坯体。制备工艺流程为:在劝lm滚球机中先放人一定量的预制氧化锆球核(尺寸小于0.5mm),启动滚球机,使之在or领角下以40:/min的转速连续平稳转动。先向滚球机中球核表面喷洒一定量的0.3%浓度聚乙烯醇水溶液,随后向其中加人一定量的氧化锆粉料,滚动1min,使粉料牢固粘附于球核。此过程使滚球机中的氧化锆球体尺寸逐渐。至球体尺寸增加到约币7mm左右时,喷洒适量水后停止洒粉,继续滚动约30min对球坯体表面进行抛光,停机后即得到表面光滑、圆度良好的氧化锆陶瓷研磨球坯体。将坯体自然干燥24h,再于80℃烘箱中充分干燥。经测定十粒球坯的直径计算其总体积,并称量其总重量,计算出此干燥后球坯体的比重为4.29c/m3。
量,计算出此干燥后球坯体的比重为4.29c/m3。
1.2氧化锆陶瓷球坯的烧结工艺
将氧化锆陶瓷球坯体分成四组,按如下烧结工艺制度烧成:室温至1000℃,升温速率为100℃/h;1000℃至烧成温度,升温速率为50℃/h,四组试样的烧成温度分别定为1450℃,巧00℃,1550℃,1600℃,保温Zh后随炉冷却,得到直径约6mm的氧化锆陶瓷研磨球。
1.3氧化锆陶瓷球性能测试方法
体积密度测定:将烧结后氧化锆陶瓷研磨球在万分之一精度天秤分别测定其干重和在水中的重量,用阿基米德法计算氧化锆耐磨陶瓷球的体积密度。
自磨损率测定:把每组待测定的氧化锆陶瓷研磨球称取1kg左右,记为m:(精确度0.019,以下同),装人内径中220mm、长220mm的聚胺醋罐,加人500mL去离子水,在球磨试验机上以60r/min转速研磨48h。取出样品用水清洗干净、于80℃烘箱中烘干后称重,计为mZ,自磨损率为:(m:一mZ)/(m,*48),单位为10一6/h,(百万分之一/h)。
结果和讨论
烧结温度对氧化锆陶瓷研磨球体积密度的影响图1为采用滚制成型法制得的氧化锆磨球坯体按规定的烧结工艺制度烧成后,利用阿基米德法测得其体积密度随烧成温度的变化曲线。可以清楚地看到,随着烧成温度的提高,氧化锆磨球的体积密度逐渐,在巧oo一1550℃间体积密度急剧增加,而在1450一1500℃,1550-1600℃温度区间曲线平缓。显然,1450℃和1500℃烧结后氧化锆陶瓷研磨球没有完全烧结致密化,体积密度均较,处于5.7一5.759c/而的水平;在1550℃烧结后,氧化锆陶瓷研磨球的体积密度急剧增加,烧结致密化明显,体积密度达到5.919c/耐,即约%.9%的相对密度〔理论密度按6.109c/m3计算)。继续升高温度至1600℃时,虽然体积密度仍略有增加(相对密度达97.2%),但是烧结球体已经基本达到致密化,上升空间非常小。
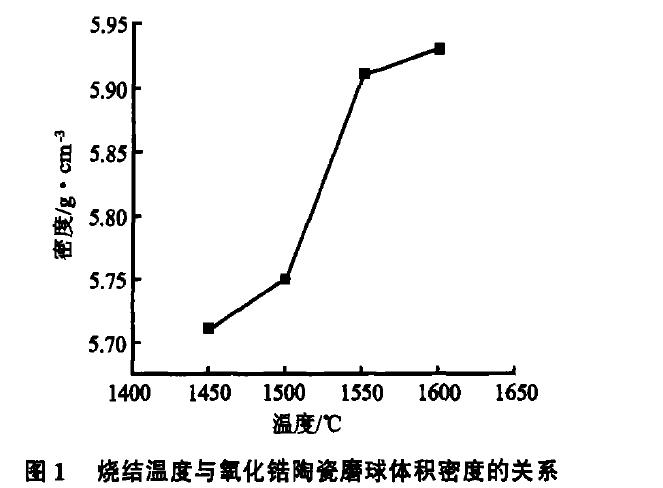

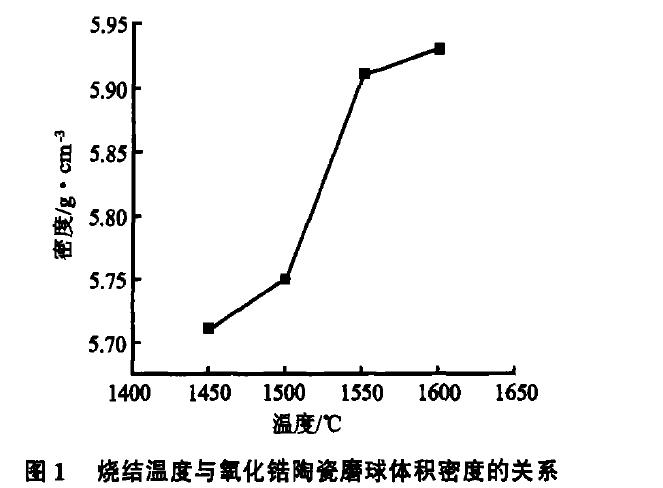

烧结温度对氧化锆陶瓷研磨球自磨损率的影响
图2为氧化锆陶瓷研磨球自磨损率随烧成温度的变化曲线。从图2可以看出,氧化锆陶瓷研磨球的自磨损率随其烧成温度升高呈现先降后上升的趋势,以1550℃烧成的磨球自磨损率。这是因为在于1550℃条件下,瓷体烧结致密化效果较差,此时氧化锆陶瓷研磨球的体积密度(或致密度)是其自磨损率主要的影响因素:球体的致密度越高,晶粒结合越紧密,自磨损率也就越,此时自磨损率随着体积密度的增加而降。烧结温度达到1550℃以后,氧化锆陶瓷研磨球已经基本达到致密化,此时在室温下可发生氧化锆应力诱导相变起增韧作用`4]的四方相氧化锆的含量应该是影响真耐磨性的主要因素:在1550℃时,体积密度虽然不是大,但可发生相变的四方相氧化锆的含量却多,所以此时的自磨损率小。当烧结温度升高至1600℃,氧化锆陶瓷研磨球的体积密度虽然略有增加,但过高的烧结温度导致部分晶粒尺寸异常长大(关于工艺条件对氧化锆陶瓷微观结构的影响将在另文中描述)。
由于氧化锆陶瓷的晶粒尺寸控制着部分稳定四方相氧化锆相变的可能性!,’,当晶粒尺寸超过四方相氧化锆转变为单斜相氧化锆的相变临界值时,那些大晶粒四方相氧化锆在冷却至室温的过程中便会发生相变转变为单斜相,导致室温下氧化锆陶瓷球体中可发生相变增韧的四方相氧化锆的含量减少,耐磨性有所下降,因此自磨损率又开始升高
结论
(l)利用滚制成型法制备了氧化锆陶瓷球坯,该球坯具有表面光滑、圆度良好、体积密度高的特点。在1550一1600℃保温Zh烧结条件下可获得相对体积密度达到97%左右的瓷体
(2)氧化锆陶瓷研磨球的耐磨性主要受其体积密度和可发生相变的四方相氧化锆含量的影响。本试验条件下,滚制法成型的氧化锆陶瓷球坯体在1550℃烧成,可以得到佳的耐磨性,其自磨损率为2.6、10一`/h。