行业知识
搅拌磨中氧化锆球大小对氧化锌超细研磨的影响
作者:admin日期:2020-05-29阅读
采用2种直径分别为0.4~0.6、0.8~1.0mm的氧化锆球,研究研磨介质大小对湿法研磨过程中氧化锌粒径的影响,并利用粉磨动力学模型分析研磨过程中的破碎机理。结果表明,采用直径为0.4~0.6mm的研磨介质研磨30min时,氧化锌粒径可达到小,即d50为0.9μm,d90为2.41μm;研磨介质直径为0.4~0.6mm时的破碎速率明显大于直径为0.8~1.0mm时的破碎速率,且破碎颗粒分布在较小的粒径范围内;在研磨过程中冲碎和摩擦破碎同时存在,研磨介质直径为0.4~0.6mm时摩擦破碎的比例大于直径为0.8~1.0mm时的比例。
作为一种具有高附加值的新材料,超细氧化锌具有小尺寸效应、表面与界面效应,从而具有紫外屏蔽、、阻燃等优异的性能,可以广泛应用于橡胶、印刷、纺织、高效光催化等领域。超细氧化锌粉体虽然可以通过化学合成的方法制备,但成本过高,至今未能广泛应用于工业化生产;而机械研磨方法产量大,成本,工艺简单,在目前的实际工业生产中应用为广泛[1-2]。
作为一种具有高附加值的新材料,超细氧化锌具有小尺寸效应、表面与界面效应,从而具有紫外屏蔽、、阻燃等优异的性能,可以广泛应用于橡胶、印刷、纺织、高效光催化等领域。超细氧化锌粉体虽然可以通过化学合成的方法制备,但成本过高,至今未能广泛应用于工业化生产;而机械研磨方法产量大,成本,工艺简单,在目前的实际工业生产中应用为广泛[1-2]。
搅拌磨具有超细、高效等性能,成为污染制备高性能、高纯度、超细粉体的主要设备。搅拌磨与普通球磨机的不同点在于研磨过程中通过输入功率直接高速推动研磨介质,外部的通过研磨介质的冲击和摩擦研磨来完成对物料粉碎[3-4],因此,搅拌磨中介质直径直接影响粉磨效率和产品细度。在搅拌磨中,颗粒破碎的方式主要有2种:1)冲击。较小的颗粒被研磨介质或大颗粒碰撞或挤压,整体破碎成小颗粒,这种破碎方式产生的较高,破碎形成的颗粒粒径分布较广。2)摩擦。颗粒与颗粒或研磨介质之间发生摩擦削磨而使颗粒减小,这种破碎只作用于颗粒表面,破碎产物的粒径比原始颗粒小得多。
本文中主要研究在搅拌磨湿法研磨过程中研磨介质直径对氧化锌粒度的影响,并借助粉磨动力学研究研磨过程中的破碎速率、破碎分布函数,分析研磨机理。
实验原料
氧化锌,d50=4.08μm,d90=21.69μm(d50、d90分别为累积体积分数为50%、90%时所对应的颗粒粒度);六偏磷酸钠,分析纯,国药集团化学试剂有限公司。
2.2实验设备
SDF型实验搅拌磨,山东莱州新宏达化工机械有限公司;氧化锆球,直径分别为0.4~0.6、0.8~1.0mm;NSKC-1型粒度仪,南京工业大学;BS423S型分析天平,德国赛多利斯集团。
2.3实法
称取40g氧化锌粉体放到分散机的砂磨罐内,用量筒称取360mL蒸馏水置于罐中,配制固相质量分数为10%的氧化锌水悬浮液;添加质量分数为1%的六偏磷酸钠,再加入240g氧化锆球,使得球料质量比(简称球料比)为6∶1,调节转速2000r/min,分散60min,制备氧化锌浆体;每隔5min测试浆体的粒径。
3结果与讨论
3.1研磨介质直径对氧化锌粒径的影响图2所示为研磨介质直径对氧化锌粒径的影响。由图可知,颗粒粒径随着时间的延长逐渐减小,直径为0.4~0.6mm的研磨介质在研磨30min后,粒径达到小,d50为0.9μm,d90为2.41μm,继续研磨,粒径基本不变;直径为0.8~1.0mm的研磨介质在研磨
50min后,d50为0.9μm,d90为3.76μm。由此可知,研磨介质直径越小,产品的粒径越小且研磨时间越短。在搅拌磨中,研磨初期的氧化锌颗粒较粗,受研磨介质的作用力大,颗粒粒径减小相对较快。随着研磨的进行,细颗粒慢慢积累,这时研磨介质所产生的作用力已不足以使颗粒破碎,所以继续研磨粒径基本不变;同时因为被研磨氧化锌颗粒的粒径比研磨介质小很多,此时的研磨方式主要为摩擦破碎,摩擦破碎的作用力主要作用在颗粒表面,所以研磨介质越小,与颗粒的接触面越大,作用在颗粒表面的摩擦作用力越大,得到的产品粒径越小。
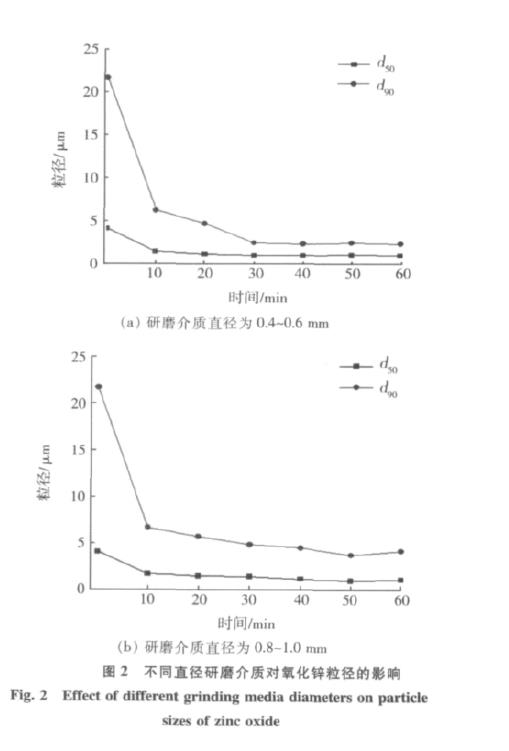
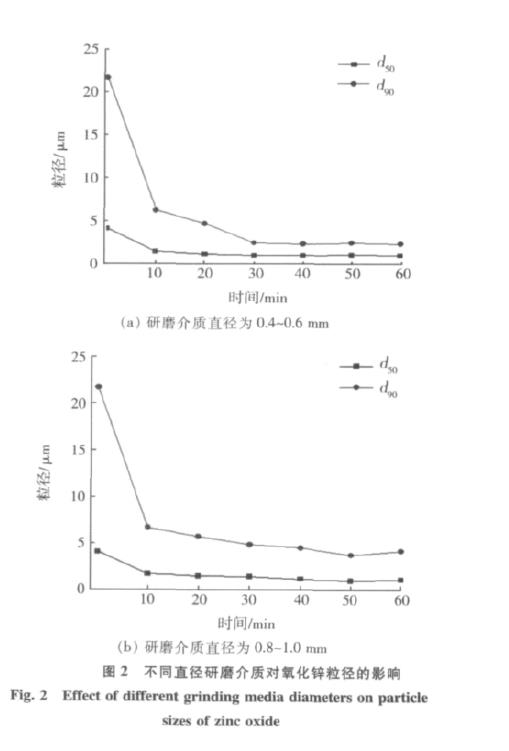
氧化锌的破碎速率
将颗粒分为10个粒级,在粒级的划分中,每个粒级的上、下限之比为姨2,用每一个粒级的粒径下限来表示该粒级的粒径,如表1所示。图3所示为根据式(4)对各粒级的累积筛余分数进行的一级Kapur系数线性拟合。图4所示为不同直径研磨介质的破碎速率。由图可知,颗粒粒径越小,破碎速率越小,相反研磨介质越小,破碎速率越大。这是因为小颗粒中的结构缺陷比大颗粒的少,使得其破碎所需的比大颗粒的大,所以颗粒越小,破碎速率越小,越难研磨;另一方面,由于小的研磨介质表面积大,与颗粒的接触面大,所以作用在颗粒表面的摩擦作用力比大研磨介质的大,破碎速率比大研磨介质的大。

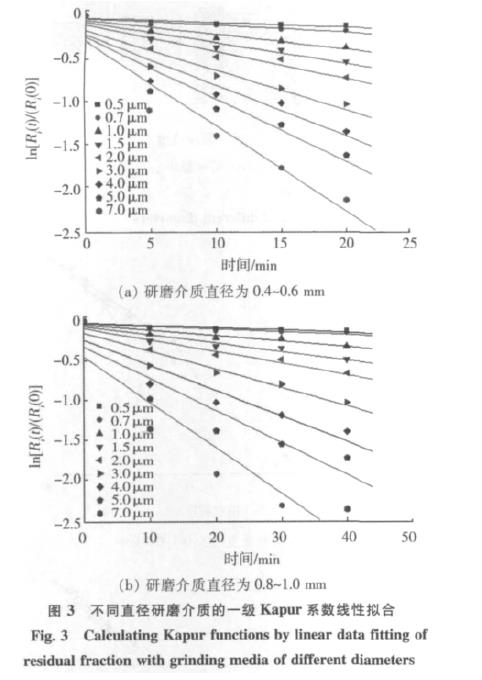
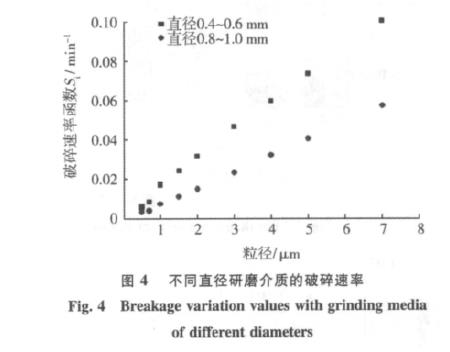

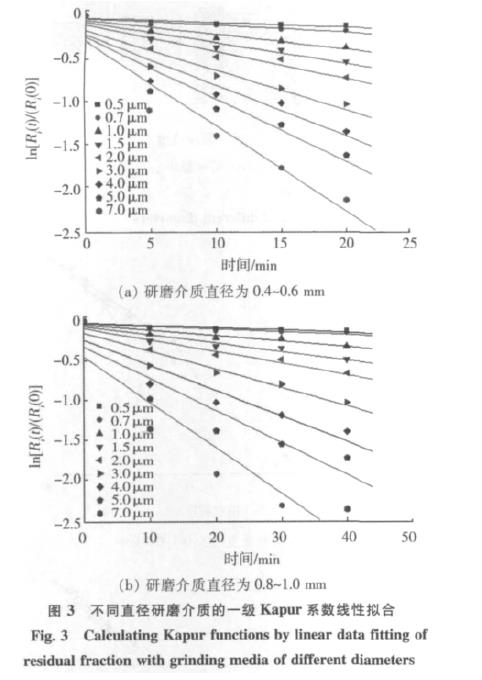
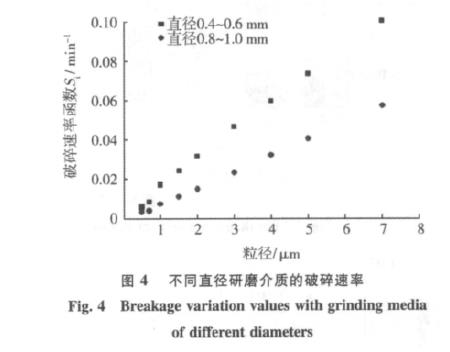
氧化锌的破碎分布函数
图5所示为1—4粒级颗粒的破碎分布函数。由图可知,氧化锌颗粒经不同直径研磨介质研磨后,破碎产物主要分布在5级及以上级粒级,较少部分产物进入6级及以下级粒级。从图5(a)、(b)可以看出,2—4粒级,研磨介质直径为0.8~1.0mm时的破碎分布函数大于研磨介质直径为0.4~0.6mm时的,即经直径为0.8~1.0mm的研磨介质研磨后,分布在这些粒级的破碎产物多于研磨介质为0.4~0.6mm时的,而从5粒级开始,情况则相反。图5(c)、(d)也说明颗粒破碎后,在相对较大的粒级,研磨介质为0.8~1.0mm时的破碎产物要多于研磨介质为0.4~0.6mm
时的,而在较小粒级则相反。以上情况说明与研磨介质为0.8~1.0mm时相比,研磨介质为0.4~0.6mm时的破碎产物分布在较小的粒径范围内,但在研磨介质一定时,颗粒是有研磨限的,不可能被研磨到无限小。
3.4氧化锌的累积破碎分布函数
图6所示为不同直径研磨介质下1粒级的Bij=f(xi/xj)曲线。对比图1、6可以看出,在氧化锌研磨过程中2种破碎方式共存,但是由于小研磨介质的表面积比较大,与氧化锌颗粒的接触面大,所以摩擦破碎的比例比大研磨介质的大。图7所示为不同直径研磨介质下不同粒级的Bij=f(xi/xj)曲线。可以看出,氧化锌颗粒粒径越小,摩擦破碎的作用越小,这可能是因为颗粒越小,破碎所需越大,而摩擦破碎源于强度的局部表面应力,提供的不足以满足小颗粒的破碎,所以对小颗粒的作用较小。
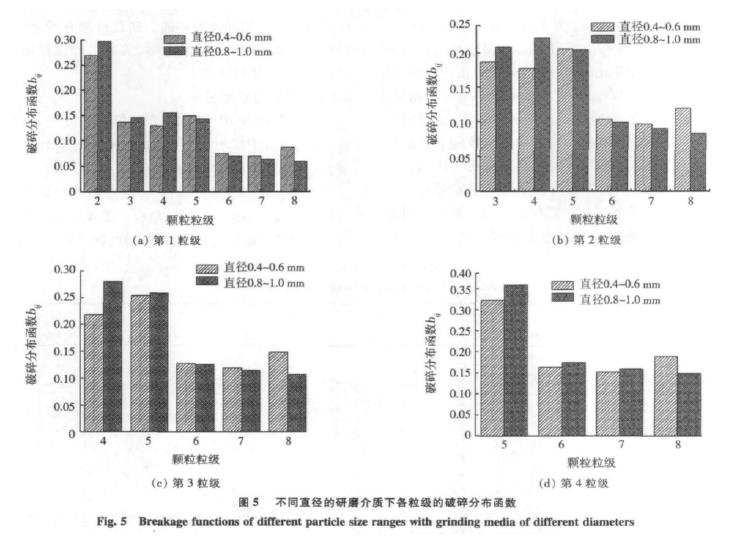
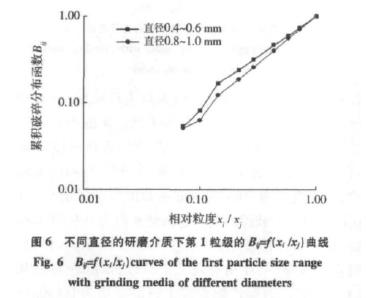
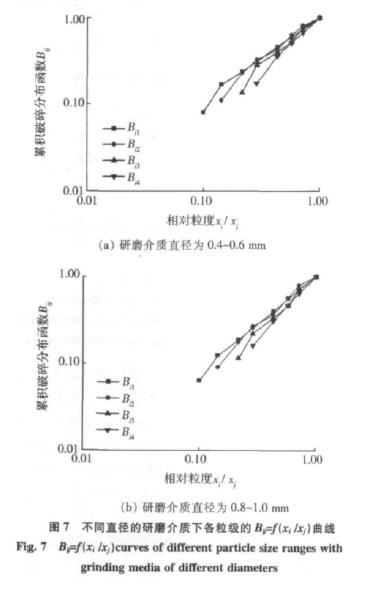
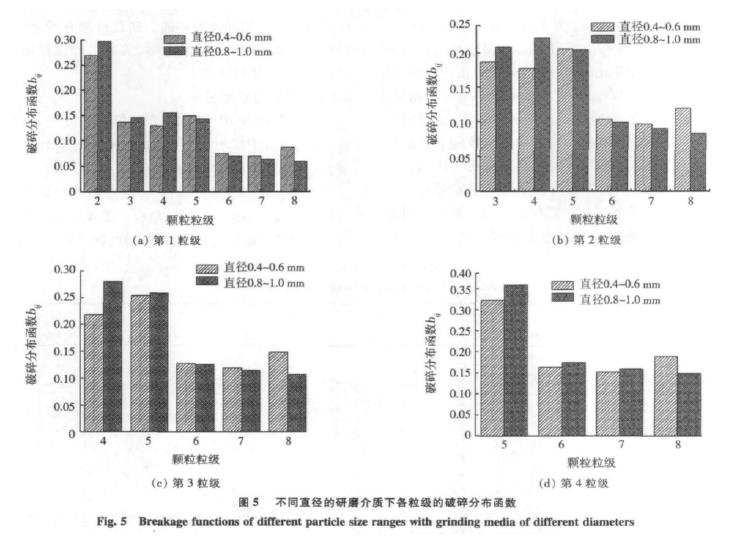
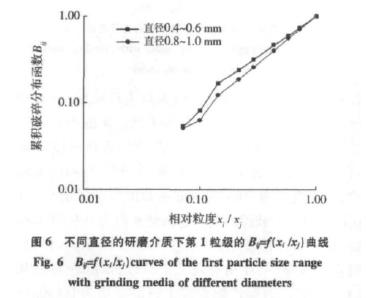
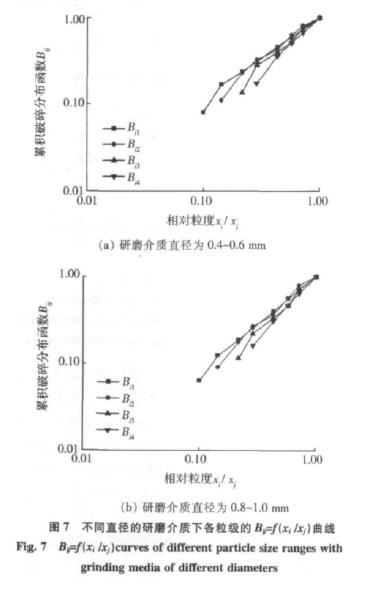
结论
1)当研磨介质直径为0.4~0.6mm,研磨30min时,氧化锌粒径即能达到小,即d50为0.9μm,d90为2.41μm。
2)研磨介质直径为0.4~0.6mm时的破碎速率明显大于0.8~1.0mm,且氧化锌颗粒越小,破碎速率越小,越难研磨。
3)相比于研磨介质直径为0.8~1.0mm,研磨介质直径为0.4~0.6mm时的破碎产物分布在较小的粒径范围内,但在研磨介质一定时,氧化锌颗粒是有研磨限的,不可能被研磨到无限小。
4)在研磨过程中冲碎和摩擦破碎同时存在,对比2种直径研磨介质的Bij=f(xi/xj)曲线,研磨介质直径为0.4~0.6mm时摩擦破碎的比例大于直径为0.8~1.0mm时的,氧化锌颗粒越小,摩擦破碎对其作用越小。