行业知识
超细分散蓝291的制备
作者:admin日期:2020-07-22阅读
以分散蓝291为研究对象,考察了球磨工艺,球磨一高压均质工艺和再沉淀一高压均质工艺对分散染料粒径的影响.在球磨工艺中,分散剂的复配比m(Reax一85A):优(MF)一2:1,m(分散蓝291):m(分散剂)一1:1,m(分散蓝291):m(Φ1 mm氧化锆珠)一1:20,溶剂为水和少量乙二醇,球磨8 h,得到染料悬浮液,经激光粒度仪检测,D。。≤163 nm,D。。≤824 nm,粒径分布不均一.
在球磨一高压均质工艺中,染料经上述球磨工艺处理后,在120 MPa下均质4次,染料D。。≤164 nm,D。。≤216 nm,粒径分布均一.在再沉淀一高压均质工艺中,分散蓝291经再沉淀后,在
120 MPa均质压力下均质4次,制备得到超细化分散蓝291,染料的D。。≤112 nm,D,。≤184 nm,粒径分布均一,较前面两种工艺更有效地减小了染料粒径.
分散染料主要用于以涤纶为主的合成纤维的染色[1],随着涤纶印染技术的不断发展和细旦涤纶纤维的出现,对分散染料的超细研磨要求越来越高[2].我国分散染料发展迅速,目前普遍采用机械球磨工
艺对分散染料进行后处理加工,但是得到的染料液体颗粒粒径大,粒径的分布范围广,粒子形状不规则,商品化质量差口].因此,迫切需要能制备出粒径小,分布窄的分散染料的新工艺.近几年,高压均质机应用于分散染料的超细粉碎后处理加工中,解决了分散染料粒径分布、扩散性能、以及生产周期长等重要技术关键[4].但是,经高压均质工艺处理的染料颗粒的粉碎程度主要依赖于颗粒本身的性质,当颗粒的内作用力较小时,颗粒就容易粉碎;反之,就比较困难.再沉淀法是将目标物的助剂溶液注入到另一种溶解性较差的溶剂中,由于环境的突变而产生纳米颗粒[5。6].Nakanishi等口1次用再沉淀法制备出茈纳米晶体,彭洪尚等[81利用再沉淀法制备出小尺寸铕配合物荧光纳米颗粒,卢建军等凹1利用再沉淀法制备聚酰亚胺纳米粒子,这种方法操作简
单,灵活,成为制备纳米颗粒的方法.笔者以分散蓝291为研究对象,考察了球磨工艺,球磨一高压均质工艺和球磨一再沉淀工艺对分散染料粒径的影响.终制备出的超细化分散蓝291产品D。。≤112 nm,D。。≤184 nm.
1 实验部分
1.1仪器与试剂
Ax搅拌球磨机(无锡市海波干燥机械设备厂);NSl001L高压均质机(意大利Niro Soavi公司);Nicomp 380/ZLS;粒度分析仪(美国Particlesizing Systems公司);DI。sB一3005温冷却泵(杭州大卫科教仪器有限公司);分散蓝291染料滤饼(浙江闰土有限公司);分散剂:木质素磺酸钠Re—aX-85A(浙江闰土有限公司);甲基萘磺酸钠MF(浙江闰土有限公司);球磨介质:≠1 mm氧化锆珠(进
口);消泡剂(杭州包尔得硅公司);无水乙醇(安徽安特生物化学有限公司);乙二醇(无锡海研生物有限公司);DMF(如皋市金陵试剂厂).
1.2料液制备
1.2.1球磨工艺
m(分散蓝291):m(分散剂)一1:1,m(染料):m(≠1 mm氧化锆珠)=1:20.在球磨机中加入30 g染料滤饼、30 g分散剂(其中m(Reax一85A):m(MF)一2:1)、100 mL水、少量消泡剂、少量乙二醇、600 g氧化锆珠,在搅拌速度500 r/min下,球磨8 h,得到染料悬浮液,取样分析粒径.
1.2.2球磨一高压均质工艺
m(染料):m(分散剂)一1:1,m(分散蓝291):m(声1 mm氧化锆珠)一1:20.取30 g染料滤饼,按上述球磨工艺处理后,得到染料悬浮液,然后加到高压均质机中,在120 MPa压力下,均质4次,对得到的染料浆液取样分析粒径.
1.2.3再沉淀一高压均质工艺
m(分散蓝291):m(≠1 mm氧化锆珠)一1:20.在球磨机中加入30 g染料滤饼、200 mLDMF和少量无水乙醇、600 g声1 mm氧化锆珠,在搅拌速度500 r/min下,球磨8 h,得到乳状染料液.
在另一球磨机中加入15 g分散剂(其中m(ReaF85A):m(MF)一2:1),100 mL水和600 g≠1 mm氧化锆珠.取上述乳状染料液50 mL,500 r/min转速搅拌球磨下缓慢滴加到球磨机中,滴完后继续球磨4 h,得到染料悬浮液.然后将得到的染料悬浮液添加到高压均质机中,在120 MPa压力下均质4次,对得到的染料浆液取样分析粒径.
2结果与讨论
2.1球磨工艺
2.1.1球磨时间对粒径的影响
实验选取不同时问取样分析粒径,结果见图1.
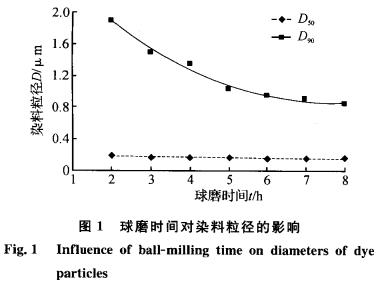
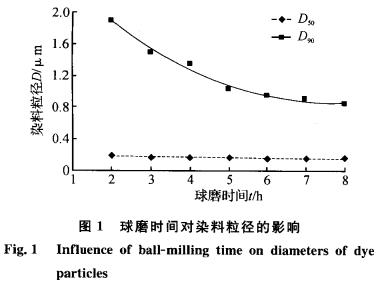
由图1可得:随着球磨时间的增加,D。。变化不大,而D。。在球磨开始的4 h内下降速度非常快,随着球磨时间的增加,粒径减小的速度逐渐放缓,到8 h后,染料粒径几乎不变.此时,染料的分散和团聚呈现动态平衡,粒径减小达到限值,球磨效率明显下降.若继续进行球磨,不增加球磨的费用,而且使生产效率降,因此,实验选用的球磨时间为8 h.
2.1.2 分散剂复配比例对粒径的影响
在球磨工艺中,加入分散剂,能够起到湿润,破碎和稳定染料颗粒的作用[1⋯.目前,染料用的分散剂主要有木质素类分散剂和萘磺酸类分散剂两大类.木质素类例如Reax 85A高温分散性好,可以提高分散体系的热稳定性.但加入木质素会使染料液的粘度,在搅拌过程中产生大量的液泡和热量,降分散效率.萘磺酸类例如MF分散剂结构小[1“,不易起泡,助磨性和润湿性都很好,但是高温分散性不佳.因而采用Reax一85A和MF复配分散剂,通过实验确定分散剂的复配比例.由下表可得,在实验条件下,分散剂的佳复配比例为m(Reax85A)。m(MF)一2:1.
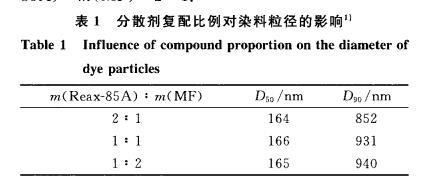
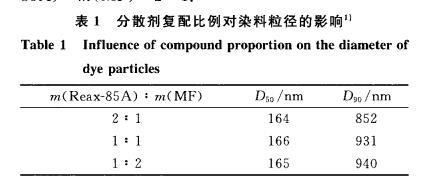
注:1)m(分散蓝291):m(分散剂)一1:l,m(分散蓝291):m(≠1 mm氧化锆珠)一1:20,球磨8 h,固含量30%.
2.1.3 染料滤饼与分散剂的比例对粒径的影响
染料滤饼与分散剂的比例也会对染料粒径产生影响.分散剂的使用量过少,分散开的染料颗粒会发生再次团聚,粒径变大;分散剂的使用量过多,覆盖在大颗粒染料上,可能会造成球磨介质在染料颗粒表面的滑移,降球磨效率.实验结果见表2,确定染料与分散剂佳质量比例为1:1.
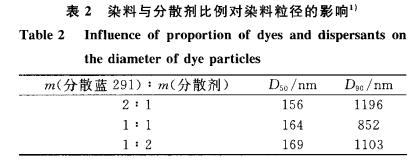
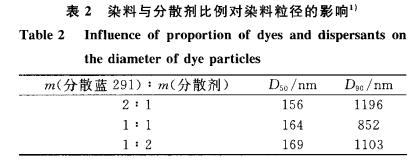
注:1)m(Reax一85A)2 m(MF‘)一2:1,m(分散蓝291):m(≠1 mm氧化锆珠)一1:20,球磨8 h,固含量30%.在球磨工艺中,一般加入一些溶剂如乙二醇等,能起到浸润作用,进而提高球磨效率[12I.由于乙二醇比较粘稠,使得染料液在球磨过程中发泡现象严重,同时产生大量的热量,因而球磨时中还应加人适量的消泡剂.加入适量乙二醇和消泡剂,按相同条件球磨8 h,终得到的染料悬浮液聩。≤163 nm,D90≤824 nm.
2.2球磨一高压均质工艺
高压均质机的工作原理[1胡是物料在通过均质阀的过程中,在高压下产生强烈的剪切,撞击和空穴效应,把原先比较粗糙的悬浮液,加工成细微、均匀、稳定的液一固分散物.因为压力在均质阀中产生的并不均匀,高压均质机均质一次具有一定的破碎颗粒概率.理论上染料液经均质6次后,染料颗粒几乎完全被破碎口⋯,可得到粒径分布均一,染料颗粒分散性小的染料液.由于普通机械球磨效率,一些染料颗粒不能与球磨介质,球磨罐和其他染料颗粒发生频繁的有效碰撞,因而难以磨碎,终导致球磨粒径大小不一,染料颗粒粒径分布离散性很大,如图2所示.图2中染料滤饼经球磨后,D。。≤163 nm,D。。≤824 nm,粒径分布图上有两个峰,表明染料液粒径分布不均一,还有少量粒径较大的染料没有被磨碎.而将球磨后的染料悬浮液在
120 MPa下高压均质4次后D。。与均质前相比变化不大,而D。。显著减小,粒径分布图上单峰,粒径分布较窄,说明少量大颗粒粒子得到了有效的破碎,见图3.
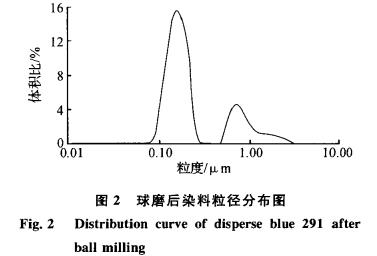
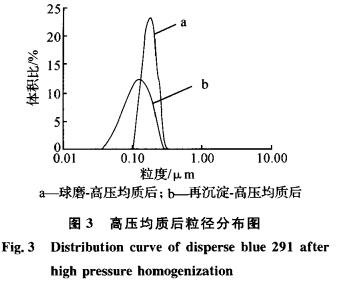
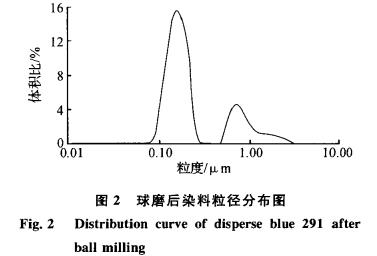
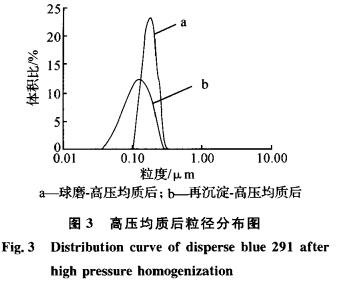
高压均质机具有占地面积小、价格时间短、操作简便、节约能源等优点[15|,将球磨工艺与高压均质工艺联用,得到的染料液的粒径小,分布均一.由于染料颗粒的粉碎程度主要依赖于颗粒本身的性质,染料经高压均质后D。。≤164 nm,D。。≤216 nm,可能已经达到物理分散的限.如要使染料粒径进一步变小,需要探索新的后处理工艺.
2.3再沉淀一高压均质工艺
再沉淀一高压均质工艺将球磨工艺、再沉淀工艺和高压均质工艺有效地串联起来,其中心思想是将分散染料溶解于溶剂中,然后注入到另一种溶解性较差的溶剂(水)中,由于环境的突变使分子产生沉淀生成分散染料微粒,再经高压均质得到超细化的分散染料.DMF对分散蓝291有一定的溶解能力,但在短时间内也不能完全溶解.因此先须经过长时间的球磨,使得较硬的染料粒子在不断地溶解和结晶过程中软化或使染料晶形破坏.然后进行再沉淀,其中染料分子由于溶剂相的突变而析出形成染料粒子,粒子不断变大,后在分散剂作用下稳定,大部分形成粒径较小的染料粒子和粒子团簇,分散在染料液中.后通过高压均质机的均质作用,粉碎粒径较大的染料颗粒,得到粒径小,分布均一的染料液,结果见表3,染料液的粒径分布图见图3中的线b(2号样品).
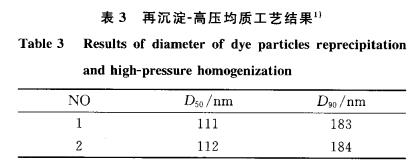
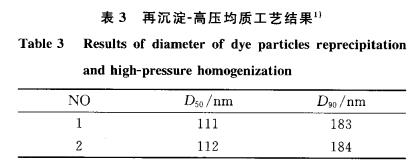
注:1)m(Reax一85A):m(MF‘)一2:l,m(分散蓝291):m(≯1 mm氧化锆珠)=1:20,200 mI。DMF,球磨8 h,进行再沉淀,后在120 MPa下均质4次.
再沉淀高压均质法优点在于染料粒径不受物理分散限的约束,可通过在再沉淀步骤中加入分散剂来控制粒径的大小,操作灵活,能有效地减小染料粒径,得到均一稳定的染料液.综合考察三种后处理工艺对染料粒径的影响,结果见表4.较球磨工艺,后两种工艺中的染料悬浮液经高压均质后,D。。显著减小,说明少量未被球磨磨碎的大颗粒染料已破碎.此外,可以看出再沉淀一高压均质工艺较其他两种工艺能明显减小粒子粒径.
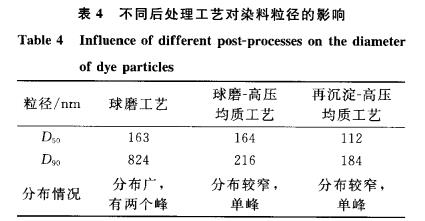
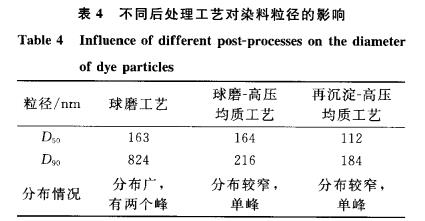
3 结 论
以分散蓝291为研究对象,探索了球磨、球磨一高压均质和再沉淀一高压均质三种后处理工艺对分散染料粒径的影响,得到了球磨佳工艺条件为:分散剂的复配比m(Reax 85A):m(MF)一2:1,m(分散蓝291):m(分散剂)一1:1,m(分散蓝291):m(≠1 mm氧化锆珠)一1:20,球磨8 h.采用再沉淀一高压均质工艺,将球磨工艺、再沉淀工艺和高压均质工艺结合,可进一步减小染料粒径,得到的染料的D。。≤112 nm,D。。≤184 nm,粒径小,分布窄.由于不同粒径的分散染料在织物上的染色性能有一定的差异,要染成相同的色泽,粒径越细的染料,其用量较小,利用率较高,因而超细化分散染料的制备可大大提高其商品化质量.