行业知识
悬浮剂湿粉碎的影响因素
湿粉碎的影响因素
的粉碎是在液相中进行,也说是所谓的“湿式粉碎”。粉碎前后的粒子状态见图2-23。这不是简单的物理粉碎过程,在粉碎过程中,有时伴有化学变化或机械力化学变化的产生,影响因素繁多,因此,单从物理学的角度去研究的湿粉碎是不够的。根据中外学者的研究结果,总结了影响湿式粉碎效率的主要因素,见图2-24。
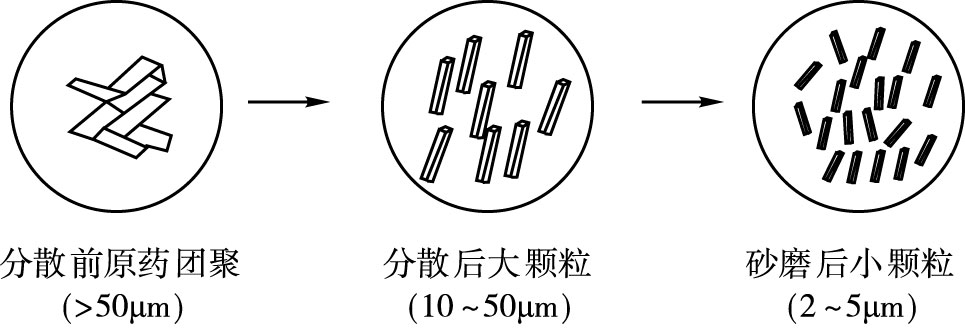
图2-23 湿粉碎过程中粒度变化
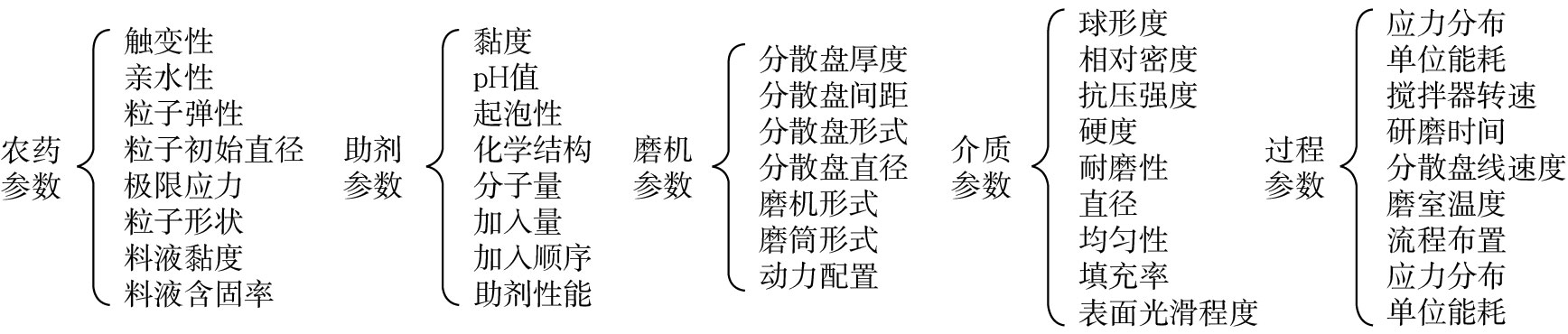
图2-24 砂磨机粉碎效果的影响因素
从图2-24中可以看出,影响粉碎效率的因素达几十项,主要响影因素有十多项。认清各因素在粉碎过程中所起的作用有助于提高的粉碎质量,降能耗。在影响粉碎效果的诸多因素中,有许多因素是相互依存、相互转化、相互矛盾的关系,所以在处理这些关系的时候不能顾此失彼。另外,每一个因素本身都有一定的允许范围,超出或达不到所要求的指标会起相反作用。基于上述原因,对这些因素进行探讨很有必要。
一、参数
1. 含固率
湿粉碎应把与助剂配制成浆状物料。如果物料的含固率过,单位体积料液中固体颗粒少,介质研磨到粒子的机会就少,磨效反而降。如果含固率过高,使之间的内摩擦加剧,耗能也会增加。一般情况下,在具有一定流动性的情况下,含固率尽可能高一些。
2. 初始粒径
砂磨机对主要是以研磨介质对其进行摩擦、剪切等形式完成粉碎。悬浮液往往是由、助剂、填料和水组成,这就难免有一些原药的团块或大颗粒。粒子所受的力与粒子的粒径成反比,见表2-10。
表2-10 粒子粒径与受力关系
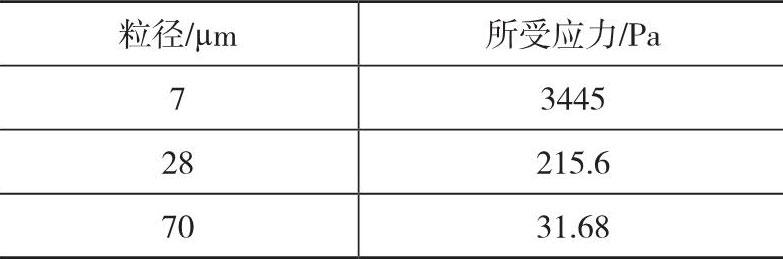
这就是说,在同一个应力场中,7µm粒子所受应力是70µm粒子的100倍左右。由于砂磨机结构的限制,对小粒子的粉碎效率较高,所以在进入砂磨机前悬浮液应进行预分散。预分散可以用高速打浆机,也可以用各种乳化机,预分散能够有效提高砂磨机的生产能力。当进入砂磨机的粒径小于50µm时粉碎效率明显提高,经验证明,进入砂磨机的粒子粒径在50µm以下比较合适。
用砂磨机粉碎时研磨介质的直径应为原始物料粒径的10~20倍。例如,进入砂磨机的原药大粒径为100µm,研磨介质直径应为1~2mm。
二、助剂参数
物质的分散度越大,比表面积也越大,相应的表面自由焓也越大。当把边长为1cm的立方体粉碎到边长为1×10 - 7 cm时,其表面积由6cm 2 增加到几百万倍,具有很高的表面自由焓的高度分散系统是热力学不稳定的,它必然会引起系统内物料的理化性质的变化。
为了降系统的表面自由焓,使其稳定,就要降系统的比表面积,因此已被粉碎的微粉将有重新聚结为大粒子的趋势。分散与聚结在超微粉碎过程中同时存在,并且后达到动态平衡。为了使粉碎向正方向移动,就要加入分散剂等物质,以其聚结。的湿粉碎离不开分散剂,分散剂的性能对研磨效率有直接影响。
1. 助剂的起泡性
助剂多为表面活性剂,易起泡是表面活性剂的性质之一,但加入悬浮液中的助剂起泡,使空气进入悬浮液中,泡沫对研磨介质的撞击起到一定的缓冲作用,降了撞击力,因此降研磨效率。起泡性也是选择助剂时控制的一个重要因素,如果选用的助剂易起泡沫,好使用(立式)密闭式砂磨机或卧式砂磨机,必要时还要加入消泡剂。分散剂是助剂的一种,在所加入的助剂中,分散剂一般都占较大的比例,所以分散剂的起泡性对磨效的影响大,表2-11是国外木质素类分散剂的起泡情况。
表2-11 木质素类分散剂的起泡情况 单位:mm
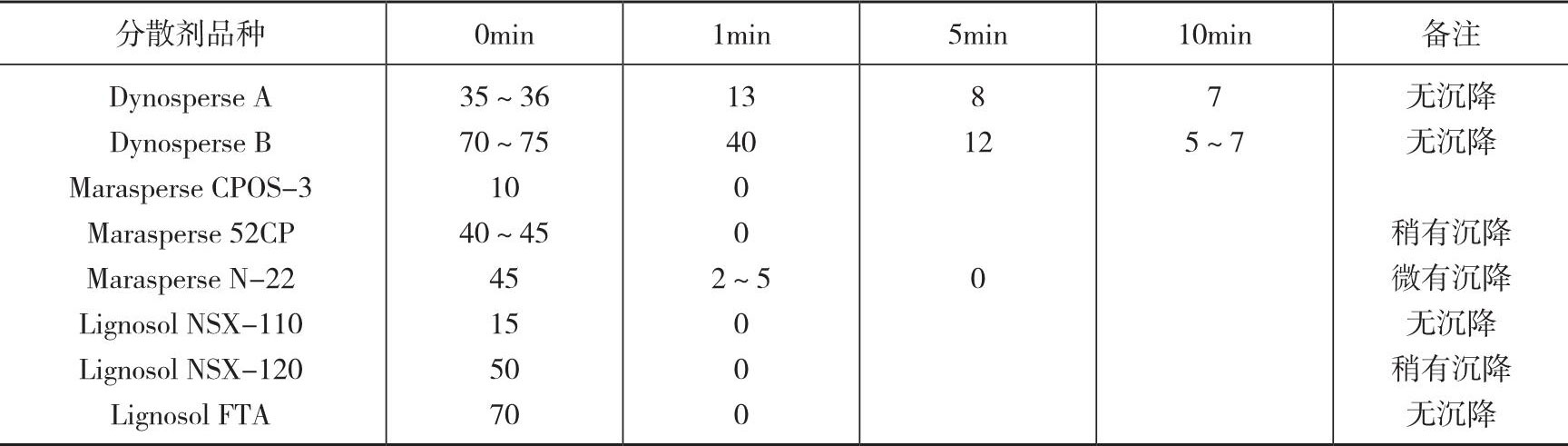
2. 分散剂加入量对磨效的影响
分散剂的助磨机理人们已经熟知,加分散剂是湿式粉碎的必要条件。也就是说,没有分散剂的加入几乎不可能达到所要求的粒度。分散剂在颗粒的表面包围一层电荷保护层,粉碎后再凝聚。随着粉碎的进行,颗粒的比表面积迅速。当分散剂不能全部包围颗粒表面时,已经被磨碎的颗粒就有重新凝聚的趋势。当这个可逆过程向负方向移动时,粉碎速率下降。但是,过多地加入分散剂会使表面形成较厚的保护层,一些未被吸附的分散剂不能溶解而形成团块,输入的大部分都消耗在粉碎分散剂的团块上。另外,介质在较厚分散剂的表面上滑动并不能有效研磨粒子,所以研磨效率反而不高。分散剂的加入量应该控制在一个合适的范围。
3. 木质素分散剂的磺化度
如果制剂中有木质素类分散剂,其磺化度对研磨效率的影响是不可忽略的问题。一般情况下,分子量小、磺化度高的分散剂溶解性能好,黏度,助磨性能好,研磨效率高;而分子量大、磺化度的分散剂溶解性能差,黏度高,泡沫多,研磨效率。
木质素类磺酸盐在水中生成大量的负电荷,包围在粒子的表面,一般情况下,阴离子型分散剂能供给的电荷越多,分散体的稳定性就越好。所以,高磺化度木质素分散剂的研磨效率就较高。
三、砂磨机参数
众所周知,湿粉碎是高耗能过程,的有效利用率在0.01%~0.8%内波动,见图2-25。所以研究粉碎规律有较大的经济意义。
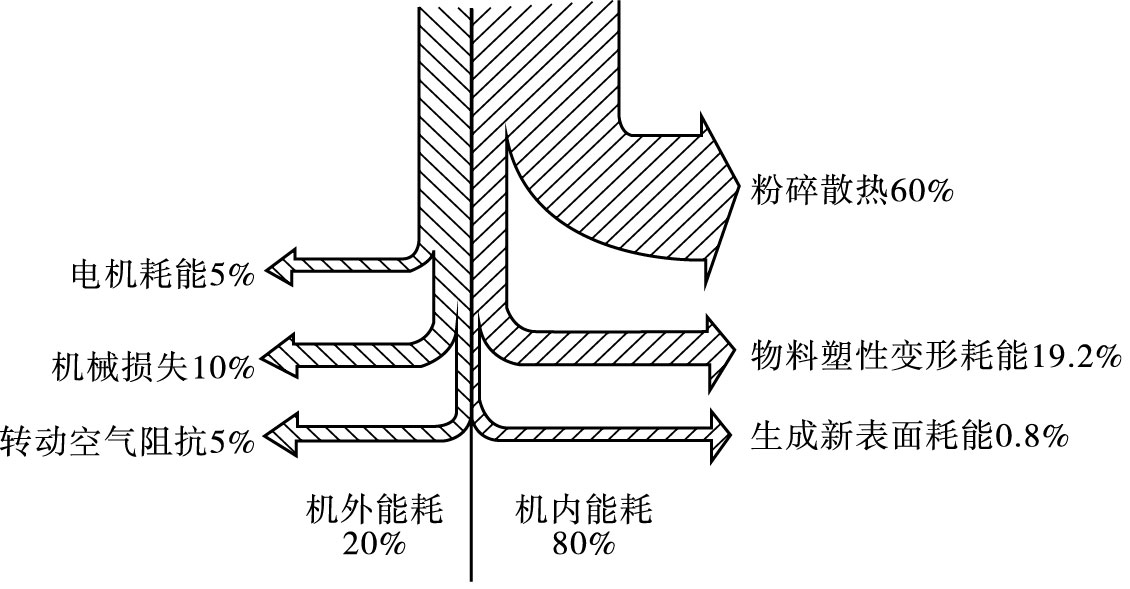
图2-25 砂磨机的分配
1. 砂磨机几何关系
砂磨机的动力是由主轴带动分散盘传递给研磨介质,研磨介质受分散盘的离心力作用向磨室壁运动,使介质沿径向有一定的密度变化。主要集中在分散盘和磨室筒壁处,见图2-26。
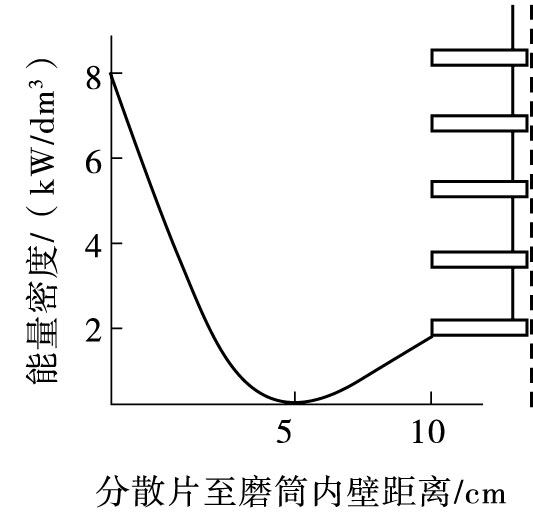
图2-26 砂磨室
从理论上讲,分散盘到磨室壁的距离越小越好。这个距离越小密度越高,粉碎效率越高。但是,这个距离越小越加剧研磨介质的磨损,工业用砂磨机都把这个间隙控制在一定范围内。各砂磨机制造企业都有自己的企业标准。
2. 分散盘型式
国内外砂磨机的分散盘已经有多种形式,如开口圆盘形、沟槽圆盘形、风车形、偏心盘形、棒状形、布孔圆盘形、环形、螺旋形等。为了地进行传递,希望研磨介质获得更大的径向力,减少轴向流动。实践证明,研磨操作出现轴向流动会降剪切力,削弱传递,加宽粒度分布。分散盘的结构形式有的复杂有的简单,结构过于复杂除不便加工外,还会加快分散盘的磨损。在各种分散盘中,圆盘形能够有效降轴向流动,避免介质和物料出现“短路”现象,目前使用较多的是圆盘形分散盘。
3. 磨室容积
通常认为,砂磨机的生产能力随磨室容积的增加而增加。按理论计算,砂磨机的生产能力与磨室容积成正比。日本的试验结果表明,砂磨机磨室容积在2~30L,生产能力与容积基本成正比。而60L以上的砂磨机情况略显不同,实际生产情况与理论值差距较大,生产效率随磨室容积的而降。所以选择砂磨机时应从生产能力和研磨效率的角度综合考虑。
四、研磨介质参数
砂磨机对物料的粉碎靠研磨介质实现,将机械能传递给研磨介质,通过介质间产生的各种机械力对物料进行粉碎。因此,研磨介质的理化指标以及应用方法将直接影响砂磨机的使用效果。
1. 介质直径对磨效的影响
砂磨机的粉碎是通过介质之间的挤压、摩擦和剪切而实现的。两介质球体间接触产生一个区域,粒子进入这个区域内才有可能被粉碎,这个区域称为“区”,见图2-27。
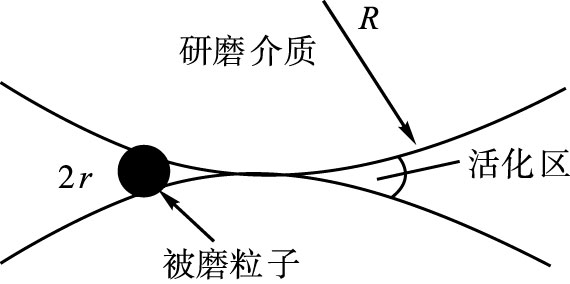
图2-27 研磨介质的
如果加入相同体积的研磨介质,小直径要比大直径磨效高,因为小直径介质相比大直径介质区。
曾经做过一个实验,分别用 φ 1mm和 φ 2mm氧化锆珠介质在200mL的微型砂磨机中研磨除草剂,研磨到 d 97 =3.3μm的时间分别为3h和5h,实验的结果也证明了这一结论的正确性。但是,使用的研磨介质不能太小,介质太小摩擦产生的热量多,会使料液升温。是热敏性物料,当料液达到一定温度时,的热运动加剧造成重新凝聚,磨效反而降。介质直径与原药初始直径有如下关系:
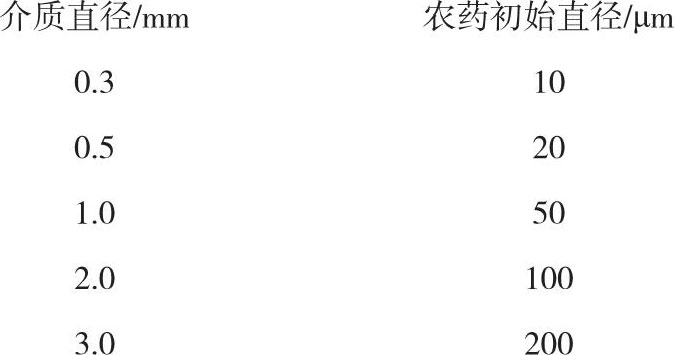
根据进入砂磨机原药的粒度,砂磨机使用的介质直径应在1~2mm,砂磨锅使用的介质直径应为3~5mm。
2. 研磨介质的均匀度
球形研磨介质也有均匀度(粒度分布)问题,对这个问题也有两种说法,这两种说法的结论恰好相反。一种从动力学的角度解释,认为研磨介质的直径尽可能要一致。以两个球形介质为研究对象,如果球径相等,它们的质量也相等,即 m 1 = m 2 ,在高速旋转分散盘的带动下能够产生相同的速度,那么, m 1 v 1 = m 2 v 2 。也就是说,两个等径介质可以获得相等的动量。相撞时,产生相同的挤压力和剪切力。如果两球不等,相撞时造成大球追小球的局面,磨效会下降。另一种说法从几何学的角度考虑,认为如果大球和小球混装,小球会充填大球的空隙,增多了介质的接触点,可以提高研磨效率。据介绍,德国的Drais公司在设备的使用说明书中要求将几种不同粒径的介质按一定比例混装。实践证明,在具有一定的抗磨、抗冲击性能的前提下,介质采取混装效果颇佳。主要原因是在研磨的初始阶段,料液中有较大的固体团块,需要较大的撞击力才能将其分散,大研磨介质能够提供足够的。当进入超微粉碎阶段,需要利用介质的研磨特性,小介质可以起到这个作用。不同粒径的研磨介质混装,使不同粒径的介质在不同阶段发挥各自的优势,能够达到预期目的。
3. 研磨介质的相对密度
对于同一种料液,介质的相对密度不同则磨效也不同。相对密度大的介质撞击也较大,应该有较高的磨效。但事实并非如此,相对密度大的介质容易沉积到磨室的底部,介质之间的接触点减少。从这个角度分析,追求介质的相对密度也不一定有的研磨效果。一般认为,研磨介质的相对密度应与料液的黏度和砂磨机的型式相适应。高黏度料液选择大相对密度介质,黏度选择小相对密度介质。立式砂磨机选择相对密度小的研磨介质。料液的黏度在0.04~0.08Pa·s,用高强度的玻璃珠(真相对密度在2.4~2.7)比较合适。相对密度超过3.0的研磨介质易沉积到底部,磨效反而降。但当采用卧式砂磨机时,选择相对密度大于等于3.75的氧化锆介质好,如硅酸锆珠效果很好,各种研磨介质的应用条件见表2-12。
表2-12 各种研磨介质的应用条件
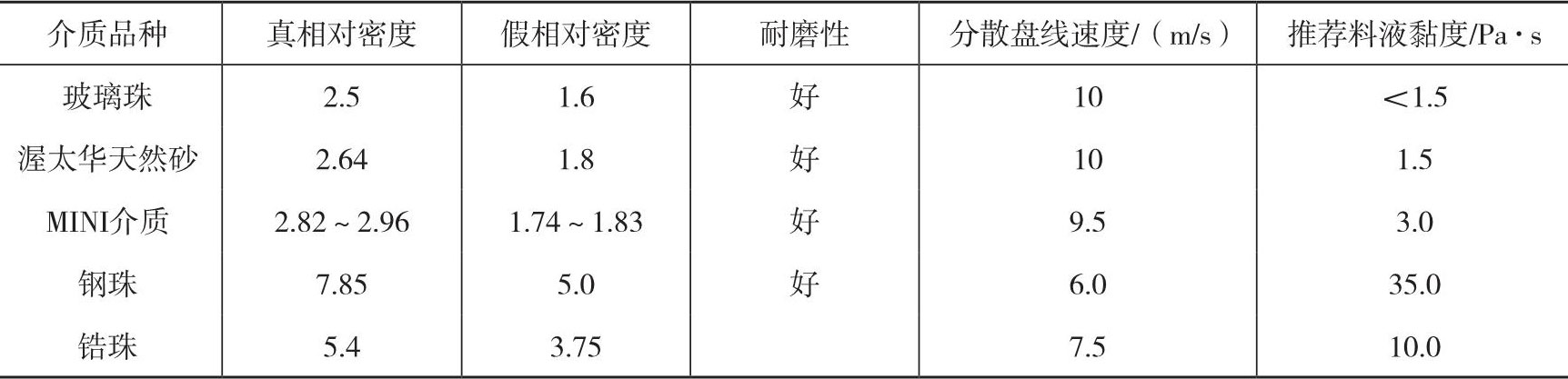
4. 介质的球形度
介质在磨室中既有随分散盘的公转也有本身的自转。显然,自转速度越高,产生的附加动能也就越大。如果球形度不好,自转运动受阻,附加动能也就减小,在一定程度上影响了磨效,因此球形度越高越好。
5. 介质填充率
在各种能够影响磨效的因素中,介质的填充率影响为显著。也就是说,它是影响磨效的主要因素。介质填充率不能过大,否则会产生大量的热量,造成已经被粉碎的粒子重新凝聚。介质的填充率前面已有介绍,卧式砂磨机填充率要高于立式砂磨机。
6. 介质表面光滑度
由于研磨介质生产方法不同,表面的光滑程度也不同。在介质粉碎物料的同时,本身也有一定的磨损。被研磨下来的介质材料就混入料液中,用通常的方法很难分离,对产品造成污染,这是生产者所不希望的。相同材料的研磨介质,磨耗率与表面光滑程度有关,表面光滑的介质耐磨性较好,所以选择介质时一定认真观察,表面有气泡或有凸凹不平表面的介质好不用。
7. 介质的机械强度
介质的机械强度主要是指在正常工作情况下介质抗压、抗冲击能力。对于金属类介质一般不存在此类问题,而非金属类介质机械强度的指标非常重要。国产玻璃介质的机械强度较差,1985年以来,生产企业改进了研磨介质生产工艺,试制成功了高强度玻璃珠,抗压强度比普通玻璃珠提高了3.5~8倍,改善了介质的使用寿命。
五、过程参数对磨效的影响
1. 砂磨机的线速度
在其他几何参数不变的情况下,分散盘应具有一定的线速度。假设在分散盘边缘有一个质量为 G 的球形介质,以12m/s的线速度做圆周运动。如果分散盘的半径为100mm,则产生的离心力是本身重力的147倍。实践证明,试验用半工业砂磨机的线速度为3~6m/s,工业用砂磨机的线速度为10~16m/s。
2. 料液温度
砂磨机有60%的转化为损失掉,在产生大量热量的同时也提高了料液温度。料液温度升高加剧了粒子的布朗运动,造成已被粉碎的粒子再凝聚。所以应控制料液温度,注意冷却效果。一般料液温度在35~50℃时磨效较高。砂磨机内温度分布见图2-28。
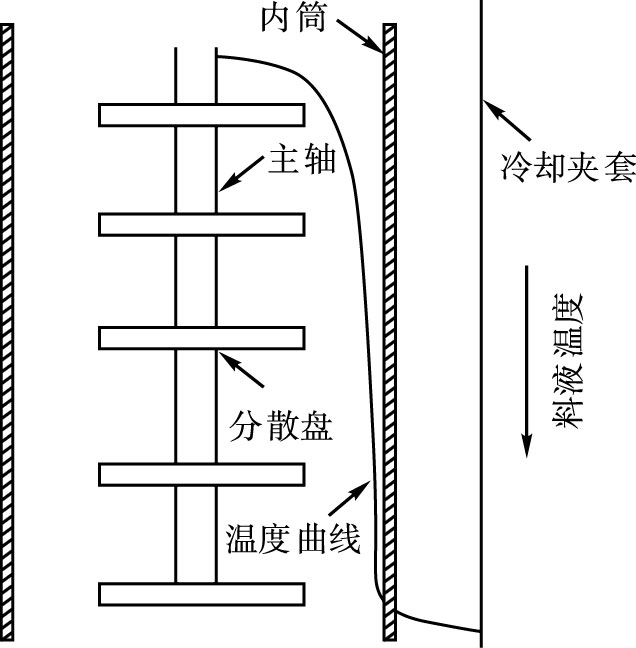
图2-28 砂磨机内温度分
3. 研磨时间
随着研磨时间的延长,粒子逐渐变小,当达到一定粒度时,再延长研磨时间已无实际意义,见图2-29。图中分别代表三种不同性质物料在研磨时表现出的规律,所以一定要恰当把握研磨终点时间,否则事倍功半, a 、 b 、 c 分别表示对三种物料操作的佳终点时间。
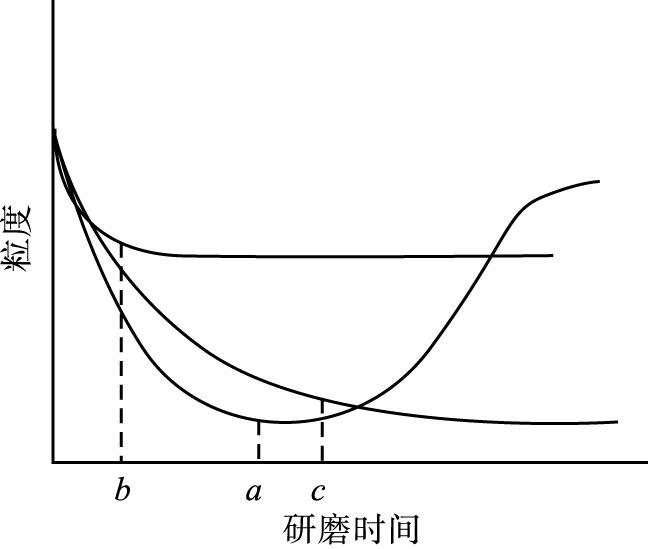
图2-29 的佳研磨时间
4. 砂磨机的流程设置
砂磨机是连续性研磨设备,通过一遍砂磨不能达到要求的粒度,这就要求多次通过砂磨机。通常采取的方法有两个,一个方法是多台串联[见图2-30(c)],另一个方法是一台[见图2-30(a)、(b)、(d)]。
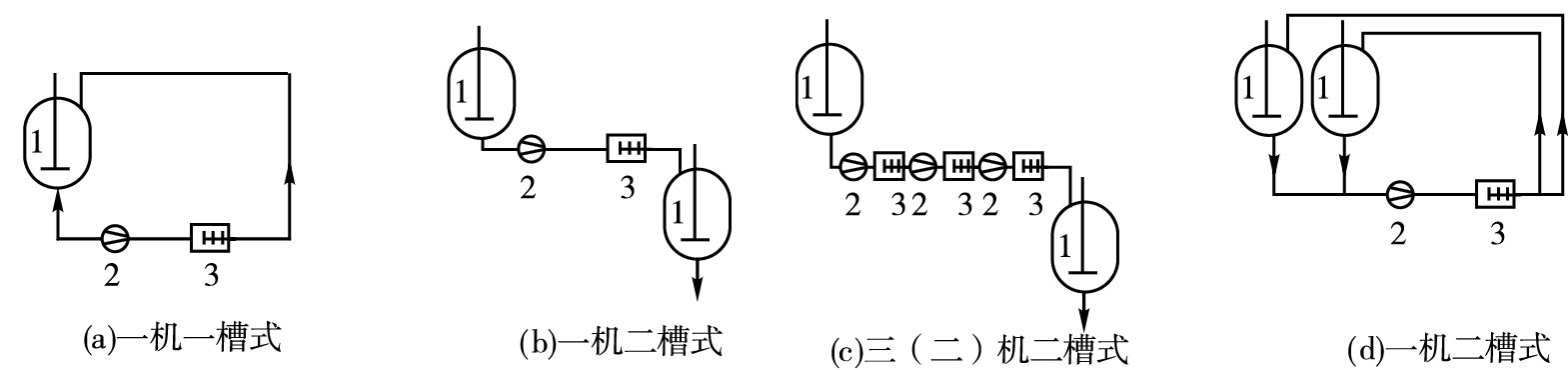
图2-30 砂磨机的流程设置
1—料槽;2—输料泵;3—砂磨机
相对应的粒度分布见图2-31。
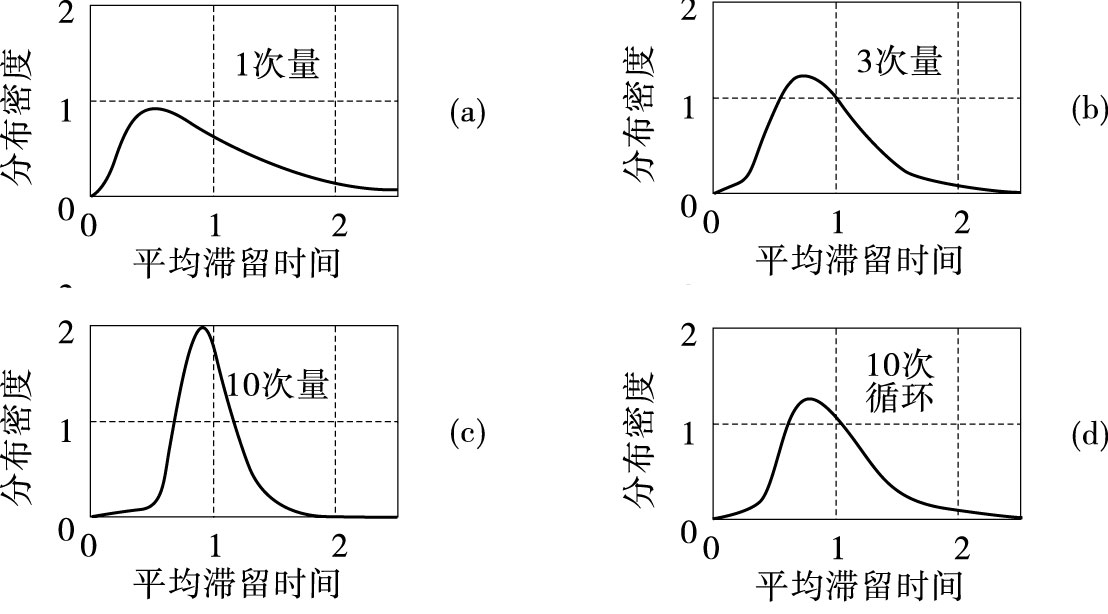
图2-31 砂磨机相对应的粒度分布
当采用多台砂磨机串联的工艺流程,按照物料经过的先后顺序,装入的研磨介质的直径依次减小。物料经过一遍研磨就可以达到要求的细度,三机串联流程见图2-32。
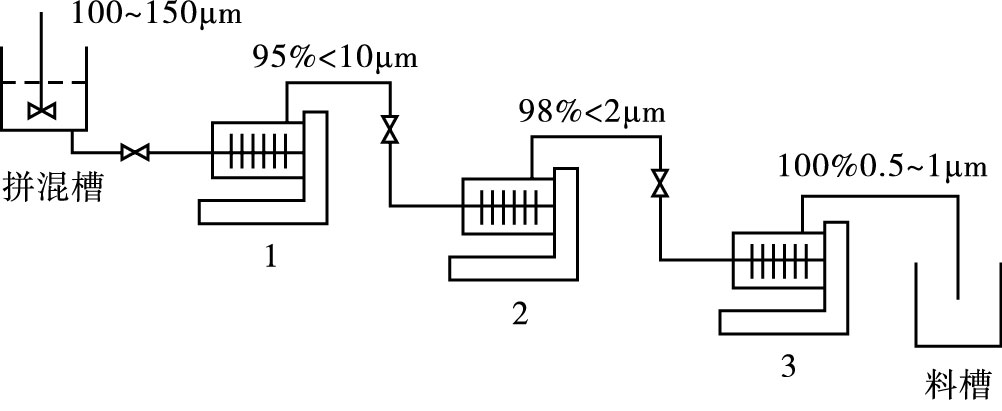
图2-32 三机串联流程图
三机串联流程中的一台砂磨机介质直径为2.5~2mm;二台为1.8~1.2mm;三台为1.0~0.8mm。如果一台转速为 v 1 ,二台为1.15 v 1 ,三台为1.25 v 1 。料液通过三台砂磨机总停留时间为5~12min,颗粒直径可以达到5~1.0μm。
图2-33、图2-34为湿式粉碎常采用的设备的布置流程。
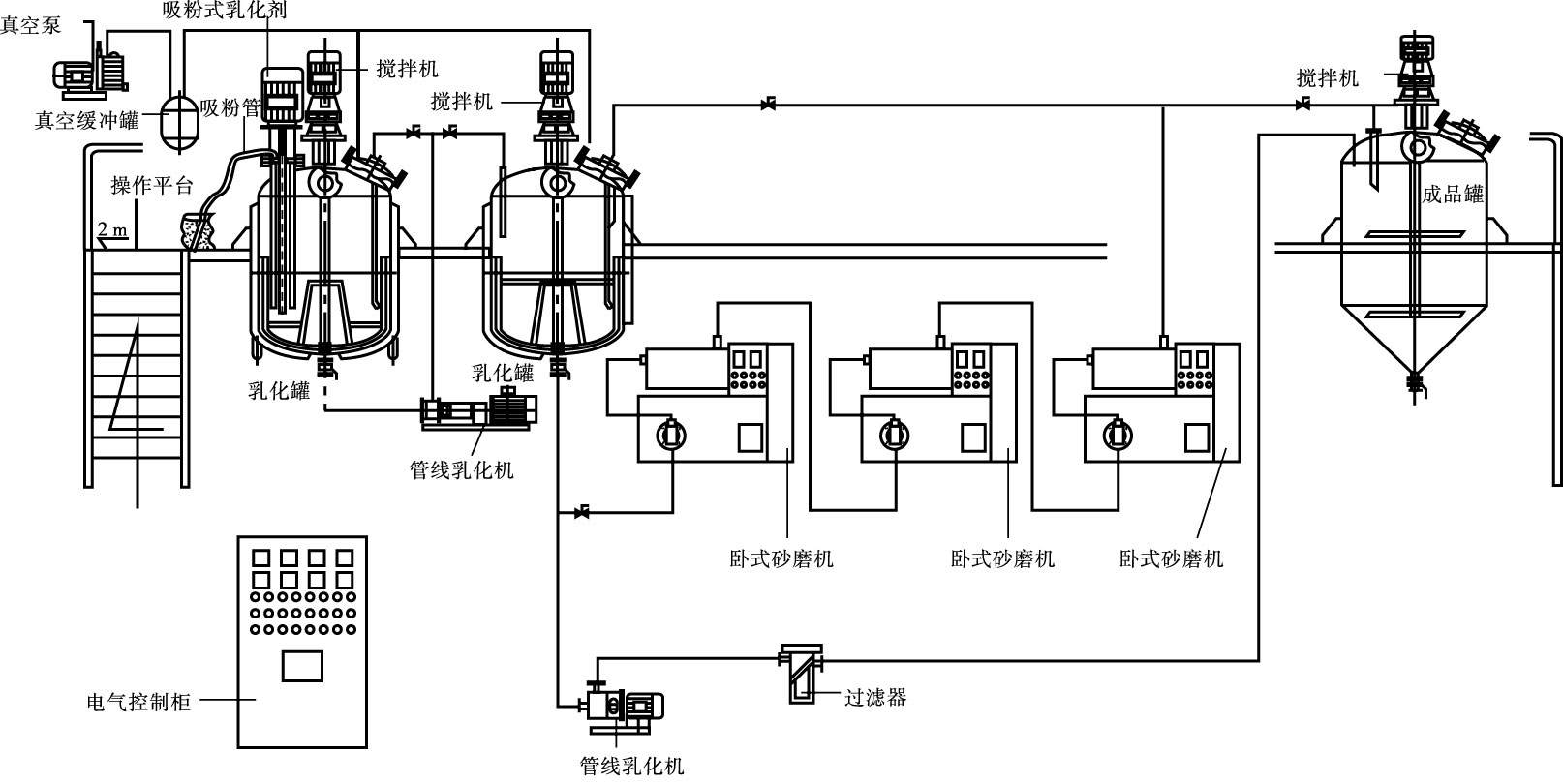
图2-33 三机串联砂磨机布置流程
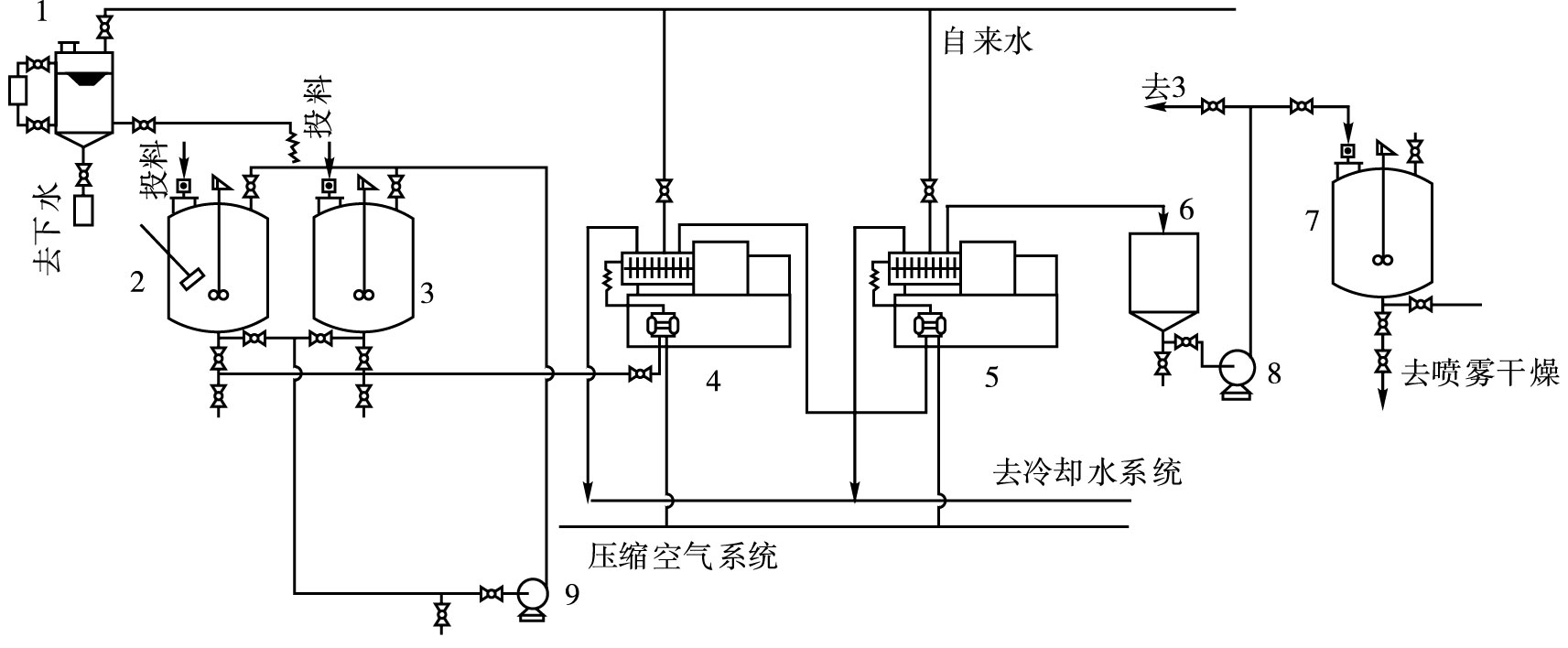
图2-34 双机串联砂磨机加工悬浮剂布置流程
1—水计量槽;2—投料釜;3—贮料釜;4—一级砂磨机;5—二级砂磨机;6—位槽;7—成品料槽;8,9—输料泵
悬浮剂的质量主要由加工的组成、湿粉碎工艺及干燥工艺决定。这些质标有产品的商业质标、和应用质标。表2-13列出了湿式粉碎中易出现的问题和解决方法。
表2-13 湿式粉碎中易出现的问题和解决方法
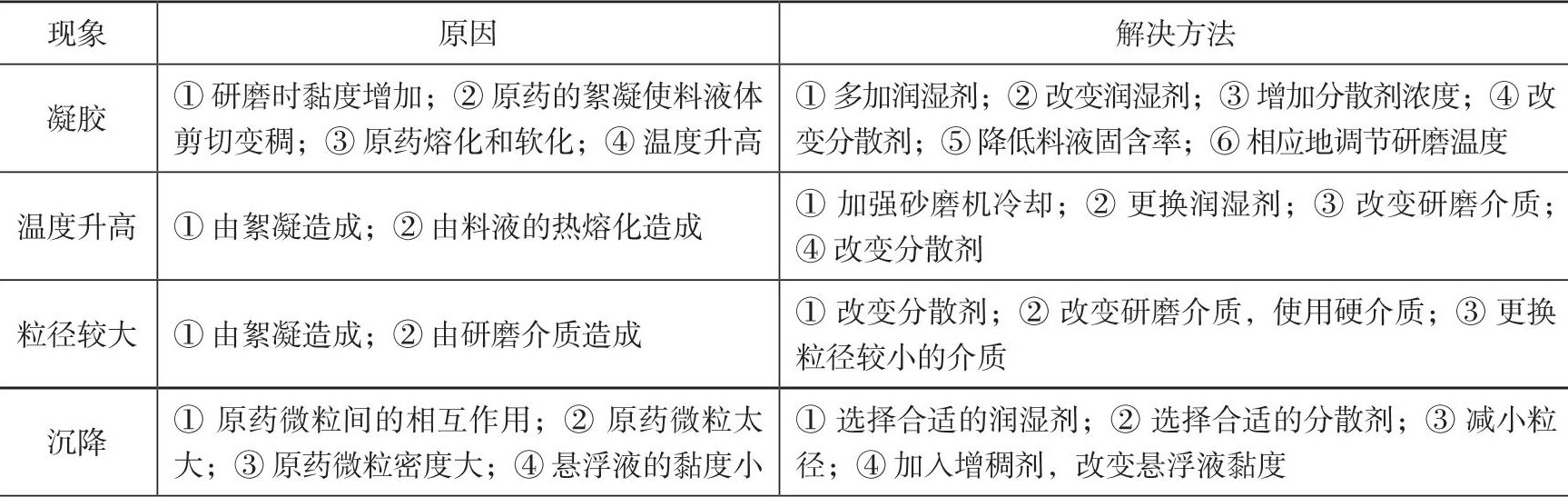
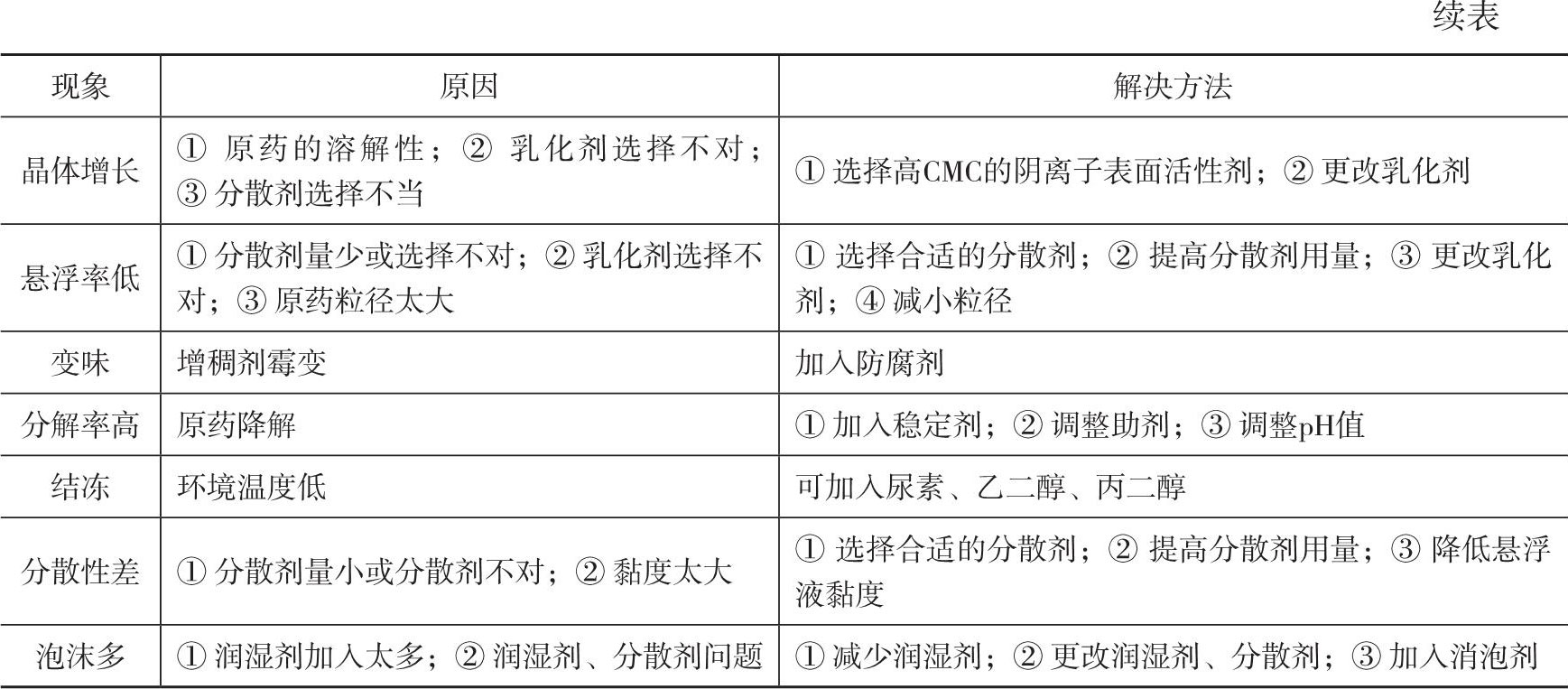