行业知识
用机械研磨法制各超细高氯酸铵AP粉体
作者:admin日期:2020-09-25阅读
实验采用机械研磨法制各超细AP粉体,所用设备为LG.1型立式搅拌球磨机,研磨介质球为直径为o.6mm的氧化锆球,具体实验步骤如下:
1.称取一定质量的工业微米级AP,然后向其中加入量取好的一定体积的非溶剂溶液,配制成悬浮液,加入适量卵磷脂作为表面活性剂,搅拌几分钟使其分散均匀。
2.1哿氧化锆小球事先洗净并烘干,按比例称重后缓缓加入球磨机罐内,加入少许上述分散介质对氧化锆球进行润洗。
3一各上述AP浆料倒入球磨机的磨罐内,在此过程中要保证所加的液体浆料要没过氧化锆球。开启冷却水,在速下开机运行一段时间,使球与物料混合均匀,然后设置球磨转速、研磨时间等开始研磨实验。
4.在研磨过程中,要定期取样进行粒度、SEM等测试,进行粒度测试的样品不经过干燥,取几滴浆料加入到乙酸乙酯中,加入吐温.80使样品分散开,然后超声5.10分钟用马尔文纳米粒度仪、微米粒度仪等测粒度。若发现研磨过程中液体没有完全没过小球,要补加液体分散介质。
5_各过筛后所得产物一部分做粒度、SEM以及TEM测试,剩余部分进行沉降后倒去上清液,后进行真空冷冻干燥。机械研磨法制备亚微米AP的流程图如下:
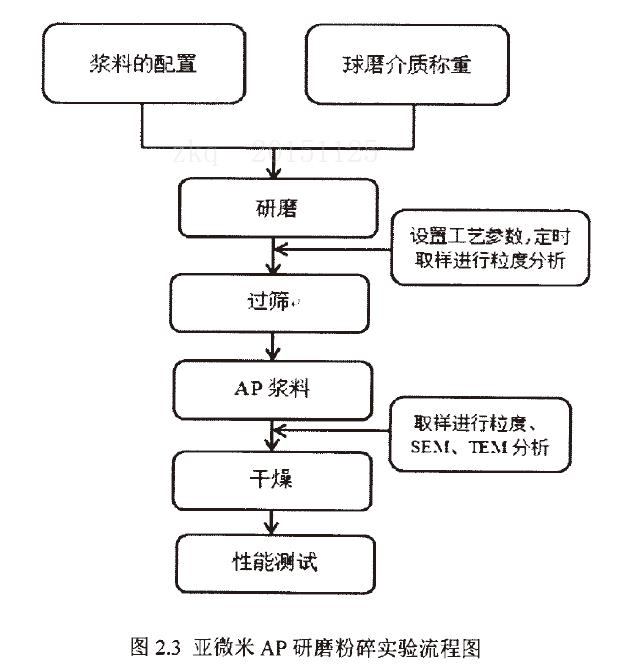
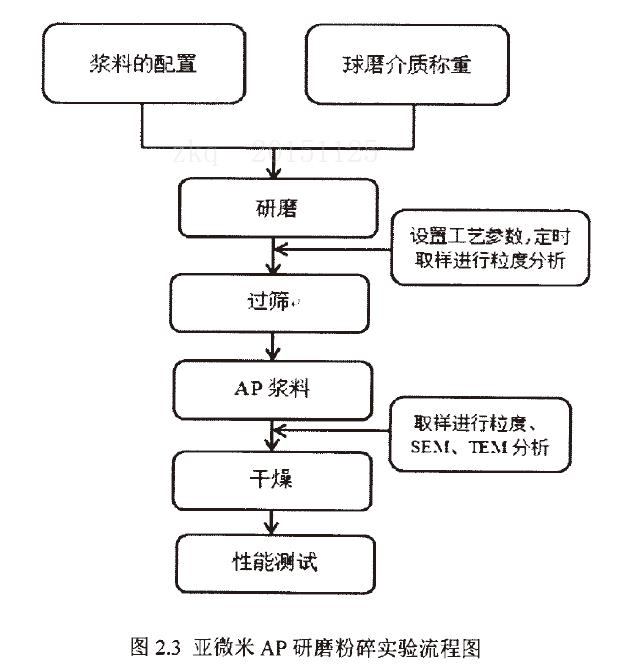
2.3.1研磨分散介质的影响
这里所说的分散介质就是湿法研磨所使用的非溶剂,为了考查不同非溶剂对AP研磨效果影响,选取了正己烷,乙酸乙酯,异丁醇、仲丁醇、混合分散介质1(乙酸乙酯与异丁醇,体积比1:1)和混合分散介质2(乙酸乙酯与仲丁醇,体积比1:1)等几种对AP溶解度较小的分散剂作为湿法研磨的分散剂,研究了不同非溶剂对AP研磨效果影响,实验初始过程中控制研磨转速为600rpm,浆料浓度为8%左右,球料比为80:1,控制研磨时问为7小时,然后每隔1小时取样,使用马尔文3000HAS型纳米激光粒度分析仪和MasterSizer微米激光粒度仪对制备的AP样品进行粒度分析,其结果如下图所示:
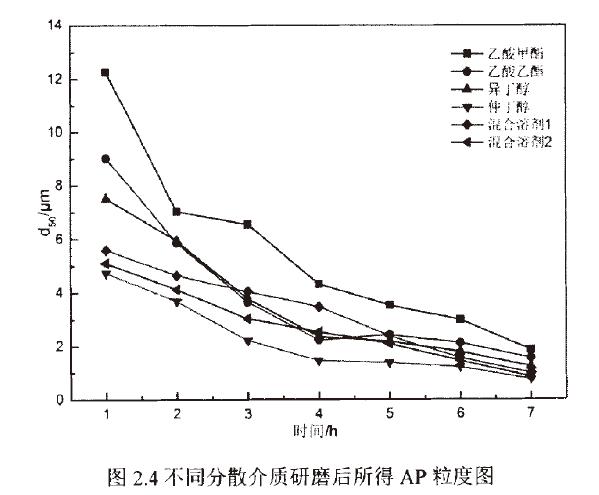
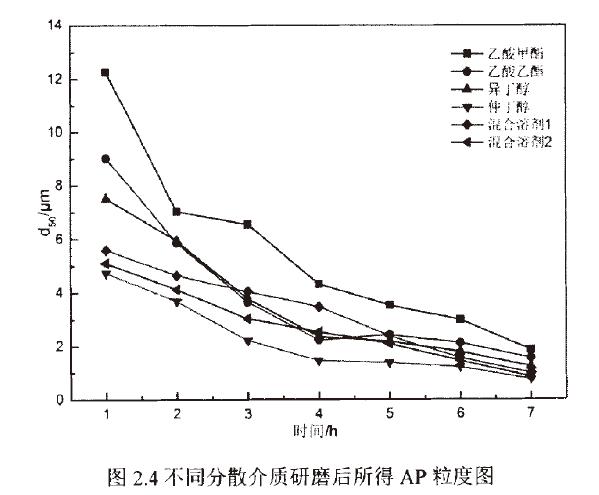
由以上图示可以看出,在0—1小时内几乎所有的分散介质均能有效的使AP粒径快速减小10pm以下,随后随着研磨时间的延长,不同分散介质对AP粒度减小的程度不同,但是共同点是粒度减小的幅度均变得缓慢。研磨4小时以后正己烷,乙酸乙酯,异丁醇、混合分散介质1和混合分散介质2等几种分散介质中AP粒度均大于21.tm,仲丁醇做分散介质的AP粒度在1.5“m左右且终所得产物粒度小,通过对比上述几种分散介质,使用仲丁醇作为分散剂时,研磨所得AP的产物粒度减小快、粒度小。
2.3.2研磨转速的影响
通过前面1.3.2.3小节对球磨过程中介质球的运动状态分析可知,对物料进行超细化时并不是转速越高越好,所以需要通过测定不同研磨转速下所得AP粒径的大小的变化来探索制备亚微米AP的佳转速,这样不能避免转速过AP粒径达不到亚微米级,同时也了转速过高带来的的浪费以及机器与介质球的损耗。同样控制其他变量一致,浆料浓度8%,球料比为80:l,填充率60%,研磨分散介质为仲丁醇,研磨时间控制为7小时,试验不同转速条件下对AP样品粒度的影响情况,其粒度随转速和时问的变化规律如下图:
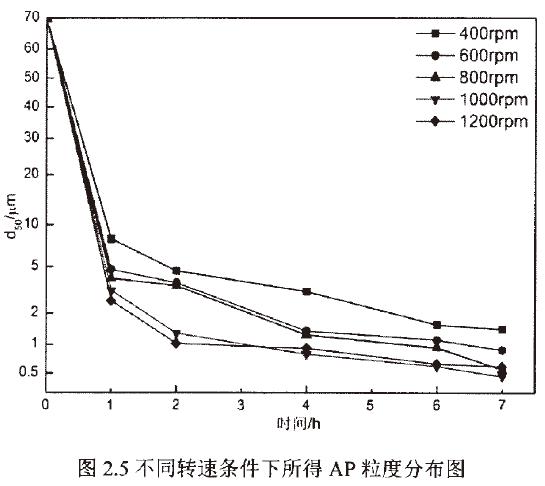
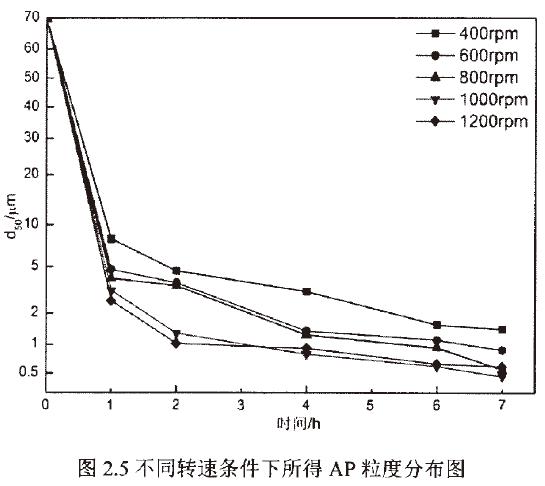
图3.4是在不同转速条件下AP的粒径d50间的变化情况,从图上我们可以看出转速从400rpm提高到1000rpm的过程中,AP粒径减小的非常迅速,然后从1000rpm到1200rpm过程中,AP的粒径减小变缓,甚至在4小时候后AP粒径的大小比1000rpm时的粒径大,这说明此时发生了一个“逆研磨”的过程,即说明AP粒子在研磨过程中发生了团聚,从而出现了粒度长大现象。由二章的综述我们知道,当转速过高时搅拌磨简体内的介质球的运动是在强大的离心力下整体沿筒壁做圆周运动,介质球之间没有发生相对位移,所以介质球之间的的摩擦力和剪切力很小,不能起到继续粉碎AP颗粒的作用,由于超细AP具有很大的比表面积,AP颗粒越细,浆料黏度越大,颗粒间开始团聚导致粒径反而变大。从图上结果可以看出在1000rpm条件下AP的d50小达到了0.52微米,达到了亚微米级别,因此选择研磨的转速为1000rpm。
2.3.3研磨时间的影响
以仲丁醇为研磨分散介质、转速1000rpm,球料比80:1,浓度8%,主要考查研磨时间对AP粒度的变化情况,AP产品粒度间变化的关系如下图2.6所示,从图2.6上可以看出,在佳转速1000rpm条件下,1.4小时内AP的平均粒径d50由3.17微米下降到0.79微米;4小时到7小时AP的粒径继续减小,减小趋势变缓,粒径减小的幅度不再明显,由0.79到0.55微米;7小时以后AP粒径出现缓慢长大现象,这说明AP粒径并不是随着研磨时间的延长一直减小下去的。
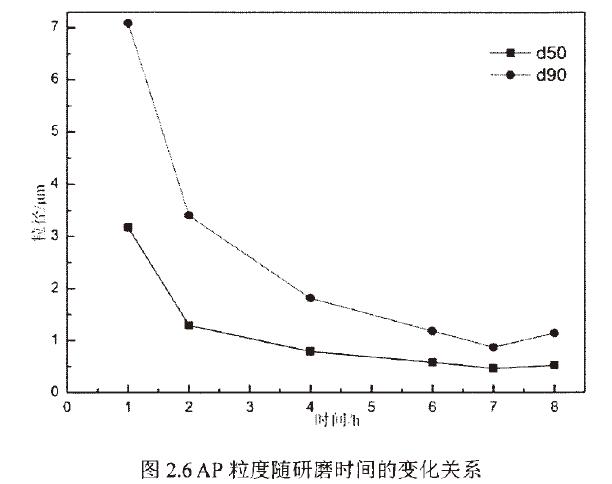
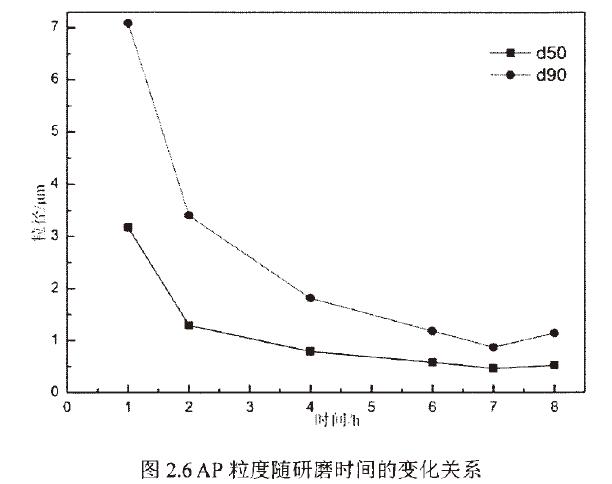
根据综述部分我们知道,当物料的颗粒越来越小时,细化物料所需要的能耗也会越来越高,在本实验条件下7小时候以后仍然在恒定转速下研磨时,超细AP颗粒会在体系中出现团聚与细化的平衡,AP颗粒已经达到其粉碎限,粒径不在减小,故在7-8小时时问段内继续延长研磨时问AP粒径基本保持不变,故本实验中选择佳研磨时间为7小时。
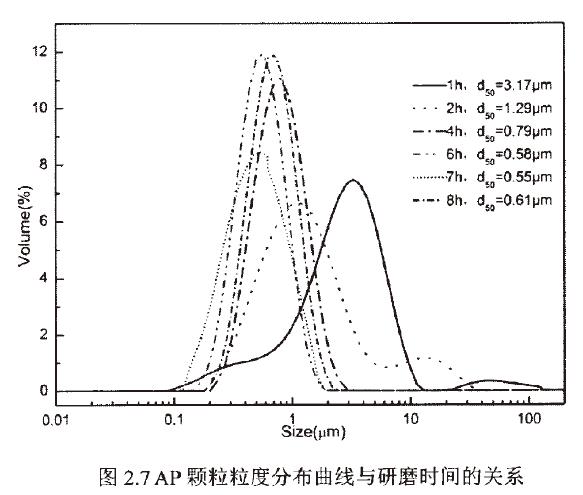
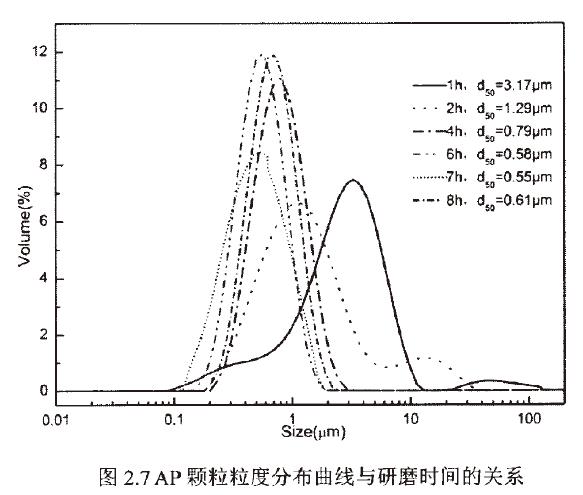
图2.7是研磨时间与超细AP的粒径分布之间的关系图,从粒度分布图上可以看出,在1.2小时内所得AP粉体的粒径较大在微米级,分布范围为O.1微米一100微米之间,说明开始阶段研磨不充分。4—7小时内粒径分布变窄达到亚微米级,7小时AP的粒度达到小值,说明随着时间的延长,AP在介质球的摩擦力和剪切力作用下持续被粉碎细化。8小时后AP粉体的粒径没有继续减小,说明此条件下AP颗粒达到了团聚与粉碎之间的动态平衡,所以AP粒径不会继续随着时间增加而继续减小。
2.3.4浆料浓度的影响
在湿法研磨实验中浆料浓度对产物粒度的影响也是一个不可忽略的因素,此处的浆料浓度为AP在非溶剂中所占的质量分数,为了获得理想的粉碎效果,在其他条件一定的情况下,我们对AP研磨过程中浆料浓度对AP粒径的影响进行了探索,选取了5%、8%、10%、15%、20%等几个不同浓度,下图是AP粒径与浆料浓度的变化关系图:从图2.9中可以看出,产物粒径随着浆料浓度的变化规律是先减小后的趋势,从5%一10%之间粒径几乎呈直线递减,AP平均粒径由1.31微米降到了0.49微米;但在10%.20%之间粒径又急剧,说明浓度超过10%后AP产品的d50随着浆料浓度的增加而变大,不利于物料的粉碎,所以本制备实验中AP的浆料浓度应该控制在10%左右为宜。
对于不同的物料来说,浆料的相对粘度不同,这跟物料自身的性质以及分散体系均有关系。从流变学理论上来分析,浆料的相对粘度随着物料浓度的而:在初始阶段,物料的相对粘度随着浓度的增加的比较缓慢,当超过某一临界浓度时,该物料的相对粘度会急剧。
根据Woodcock公式,在浆料中固体颗粒间的距离会随着物料浓度的而减小:


从式中可以看出当固相含量西一定时,h和d成正比,颗粒粒径越小,颗粒间距离越小,范德瓦耳斯力,颗粒间相互接触几率,了悬浮液层问的运动,浆料的流动性变差
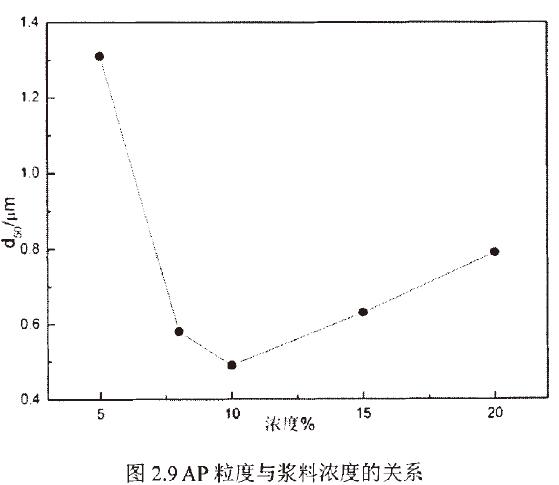
在研磨的过程中,如果浆料浓度太,大部分介质球问没有物料存在,这种现象为“空研”现象,即磨球之间的相互作用,这样的话不粉碎效率较,而且还容易使磨球受到磨损,浪费而且也会对产品造成污染。但如果浆料浓度过高的话,颗粒间距离变小导致浆料的流动性降以及粘度,研磨介质球的运动阻力就会,减少了磨球与物料的有效碰撞,磨球对物料的研磨概率减小。此外,浆料浓度过高也会导致颗粒问的团聚,特别是随着研磨的持续进行,颗粒越来越细,其表面能也越来越高,更容易发生团聚现象。
2.3.5球料比的影响
球料比是磨球与物料的质量比,在研磨试验中球料比也是一个比较重要的参数,它对物料的粉碎细化也有较大的影响。不同研究者对球料比做了大量研究,控制其他条件为上述佳分散介质、研磨时间、研磨转速、浆料浓度等,球料比分别为40、60、80、100、120、180进行试验,获得了不同球料比时AP产物的粒径分布结果,如下图所示:从图2.10上可以看出,当球料比从40到100时,AP的平均粒径快速减小,d50由1.24微米减小到0.46微米,d90为0.99微米,此时得到的AP粒度小;当球料比由100增加到120时,d铀几乎没有减小;当球料比增加到180时,AP粒径不没有继续减小,反而稍微有所增加;在球料比为100时可以看出此时产物粒度较细,此时比较适中,一方面满足了AP终产物的粒度要求,另一方面也减小了磨球对机器的磨损以及磨球与磨球之间的损耗。因此本实验中我们认为球料比为100时比较合适。
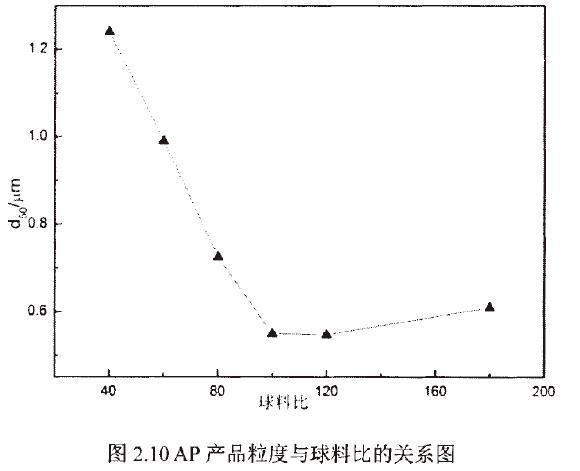
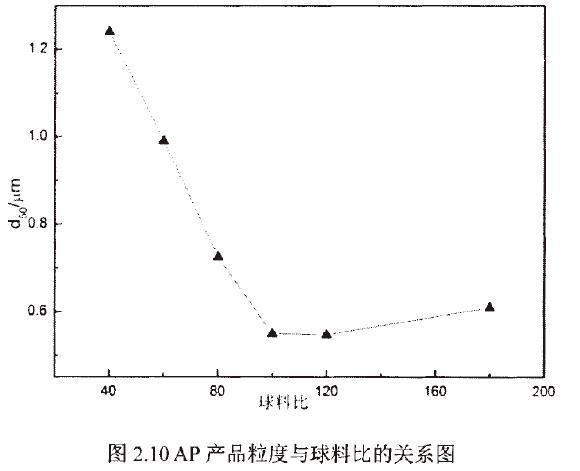
根据综述部分理论分析我们知道,在立式搅拌球磨机中,粉碎物料主要的作用力来自于磨球之间的挤压力和剪切力,球料比对物料粒度大小的影响其实就是介质球之间与物料之间接触机会多寡的直接反馈:当球料比小时,磨球与磨球之间的距离较大,在研磨过程中与物料作用的机会较少,因此不能够较有效的降物料的粒度;当球料比过大时,磨球与磨球之间的距离较小,研磨过程中与物料接触机会较多,迅速减小了物料的粒度,由于物料的粒度越来越细,那么其比表面积就越大,物料之间的距离小于自身的粒径那么就容易团聚,影响了研磨的效果。此外,在球磨过程中,物料的粒径越小,那么使其继续粉碎所需要的也越高,在转速一定的情况下,随着球料比的增加不能够继续提供物料细化所需的,研磨效率降,所以物料细化的效果就不会明显。通过控制变量法对以上几个工艺参数的探索,现在基本确定了制备亚微米AP的佳工艺条件,使用仲丁醇作为研磨AP的分散介质,研磨转速为1000rpm,研磨时间7小时,浆料浓度为10%,球料比为100,终所制备的粒度小的AP产物粒度为ds020.469m,d90=0.999m。