新闻中心
氧化铝粉体湿法球磨参数优化
作者:admin日期:2020-06-24阅读
为获取可用于陶瓷膜支撑体烧结的、粒径分布合理的原料粉体,实验中以粒径500M的氧化铝粉体为原料,探索其湿法球磨优条件。在不同球磨时间和球料比条件下进行球磨,对比球磨效果,测定球磨后粉体的粒径及分布并综合考虑成本因素后得出结论。实验结果表明,球料比(9~11)∶1、球磨时间9~10h为优球磨条件。后续实验则表明,在优球磨参数下所得粉体粒径较均一,可直接用于烧结耐高温、高强度的陶瓷膜支撑体。
随着膜分离技术的快速发展,陶瓷膜已在、食品、化工、医药、生物工程等行业得到广泛应用,但对其常见原料氧化铝粉体的湿法制备技术研究未见报道。粉体的粒径、粒径分布、球形度等参数,可直接影响终烧结而成的陶瓷膜支撑体的结构和性能,降陶瓷膜支撑体的制备成本也是近年来陶瓷膜研究的重点之一。因而制备形状、性能符合陶瓷膜支撑体烧结需要的粉体,优化其制备条件并降成本非常重要。
当今陶瓷膜生产中,α-Al2O3是重要的陶瓷膜支撑体制备原料之一[3],而α-Al2O3在多种氧化铝晶体中稳定,晶格能大、熔点高、硬度大,研磨难度大,因此将商品α-Al2O3粉体研磨成为适合粒径的粉体,球磨时间一般在12h以上[4-6],所以该过程能耗高,电耗可占陶瓷膜制备成本的50%左右[7]。所以有必要优化球磨条件,提高生产效率,降能耗,降陶瓷膜综合生产成本,进一步提高陶瓷膜的工业推广可行性。尽管干法球磨后的颗粒球形度优于湿法,但湿法球磨的效率优于干法[14-16],因此本实验采用式湿法球磨技术,聚丙烯酸(PAA)为分散介质[17],优化对影响球磨效果显著[11]的球磨时间、球料比等参数,并通过对比球磨后粉体的粒径、粒径分布等参数进行实验验证。
实验
2.1实验原料
氧化铝粉体购自山东省淄博市某公司,粒径为500M,经测试,粒径分布见表1。
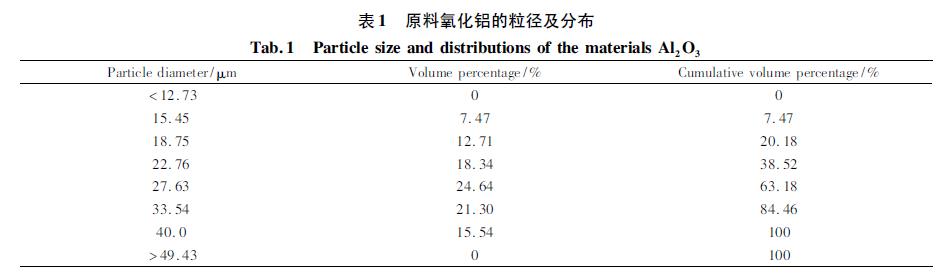
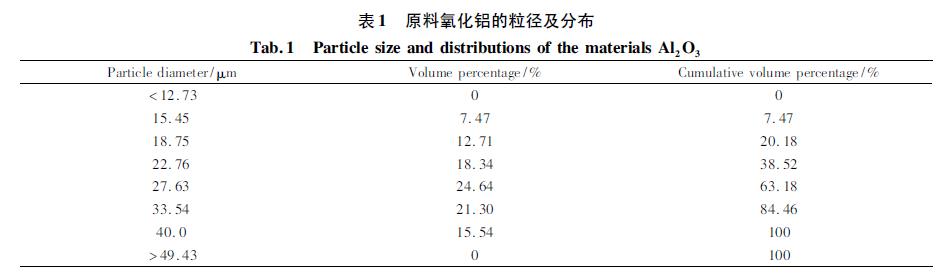
2.2主要实验仪器及设备
①立式球磨机,型号LM-70,总功率5.5kW,无锡市新标粉体机械制造有限公司生产;
②激光粒度分析仪,型号Winner2000S,测试精度0.1~300μm,济南微纳颗粒仪器股份有限公司生产;
③空气压缩机、双气动隔膜泵、烘箱、电子天平等。
2.3实验过程
利用湿法球磨技术,将粒径500M的氧化铝原料粉体,在3∶1、5∶1、7∶1、9∶1、13∶1的不同的球料比(W/W)下研磨为目标颗粒(粒径小于10μm)百分比(wt%)大于90%的、可直接用于制备陶瓷膜支撑体的氧化铝粉体,为球磨污染的影响,研磨介质选用直径6mm的复合锆珠,共研磨15h,在球磨时间为2.5h、5.0h、7.5h、8.5h、10.0h、15.0h时分别取研磨后氧化铝悬浊试样500mL,置于烘箱烘干,用激光粒度分析仪测定其粒径及分布。
3结果及分析
3.1实验结果
经实验测定,不同球磨时间、球料比条件下的研磨结果见表2。
3.2对比分析
(1)球料比对球磨效果的影响
以目标颗粒百分比为纵轴,球料比为横轴,对比研磨相同时间后的效果,分析球料比在不同时间段的影响。图1展示了研磨2.5h、5.0h、7.5h、8.5h、10.0h、15.0h后的目标颗粒完成情况,图1a表明,无论球料比大小,研磨2.5h后,原料颗粒仍处于由10~40μm区间,难以达到目标颗粒粒径;图1b表明,5.0h后,球料比高者可完成目标颗粒达50%以上,球料比较者未检出目标颗粒,说明研磨初期,在0~5.0h内球料比为主要影响因素,球料比越大球磨的效率越高,决定了此时处于目标颗粒生成阶段还是原料破碎初期,但球料比的影响未呈现出较好的规律性变化。
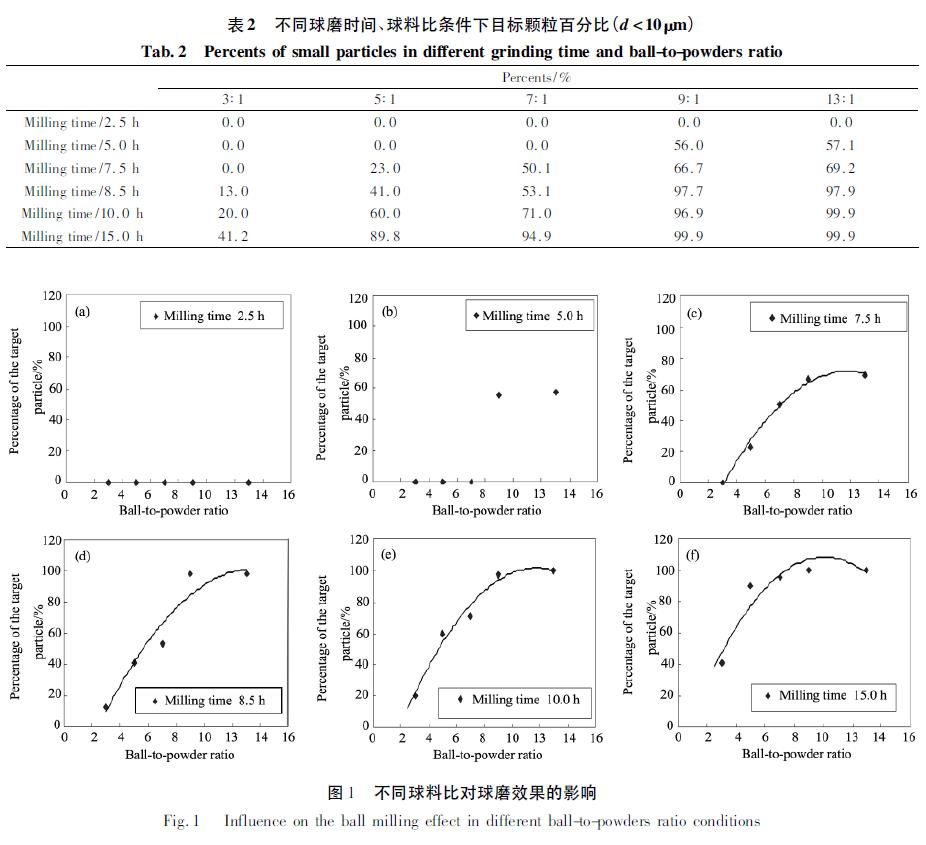
以目标颗粒百分比为纵轴,球料比为横轴,对比研磨相同时间后的效果,分析球料比在不同时间段的影响。图1展示了研磨2.5h、5.0h、7.5h、8.5h、10.0h、15.0h后的目标颗粒完成情况,图1a表明,无论球料比大小,研磨2.5h后,原料颗粒仍处于由10~40μm区间,难以达到目标颗粒粒径;图1b表明,5.0h后,球料比高者可完成目标颗粒达50%以上,球料比较者未检出目标颗粒,说明研磨初期,在0~5.0h内球料比为主要影响因素,球料比越大球磨的效率越高,决定了此时处于目标颗粒生成阶段还是原料破碎初期,但球料比的影响未呈现出较好的规律性变化。
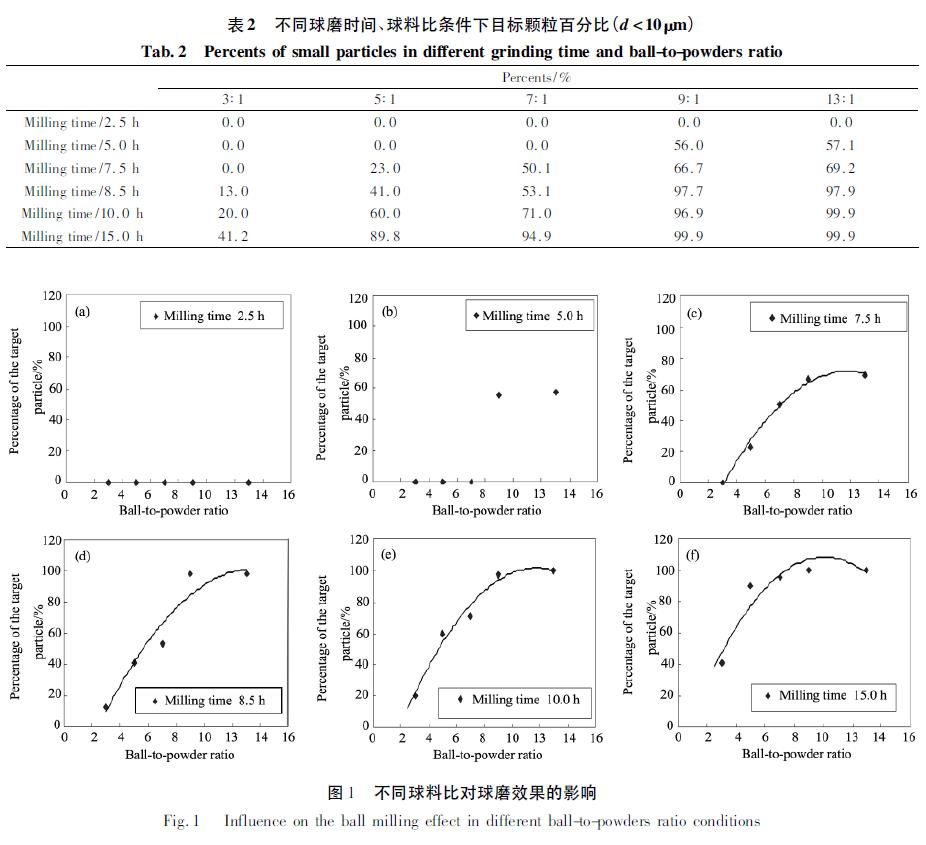
由图1c可见,研磨7.5h后,随着球料比增加,目标颗粒完成比例先连续增加,在球料比高于10∶1时趋于稳定,表明球料比增加到一定值后,不再是主要因素,原料颗粒的破碎、数量激增已成为提高有效碰撞率的主要因素,图1d、e、f则表明球料比较高者在15h结束前已完成研磨过程(目标颗粒百分比大于90%),后期可能出现了“逆研磨”现象,即团聚现象,因而出现球料比高,目标颗粒百分比反而上升变慢的情况。
(2)研磨效果间的变化以目标颗粒百分比为纵轴,球磨时间为横轴,对比同一球料比条件下研磨效果间的变化情况,见图
2,分析研磨过程中颗粒碰撞的规律和特点。
总体来看,随球料比的提高,物料与球磨介质接触的几率,研磨效率同比呈现提高趋势,但由此带来的研磨效果变化趋势有明显变化。图2a、b均表明,球料比时研磨15h,目标颗粒百分比于90%,且呈现加速上升趋势,表明此球料比条件下研磨15h期间,一直处于原料初期破碎(10~40μm之间)和部分目标颗粒生成阶段,还需更多的时间才可能完成研磨目标,能耗高。球料比达7∶1及以上时,目标颗粒百分比的上升趋势不再是加速上升,基本处于直线上升状态,而在球料比9∶1时上升速度逐渐减缓,球料比13∶1时研磨约8h后就达到了球磨目标,大大缩短了研磨时间,降了能耗。所测目标颗粒百分比均未达到表明,尽管颗粒粒径处于微米级,仍然存在团聚现象
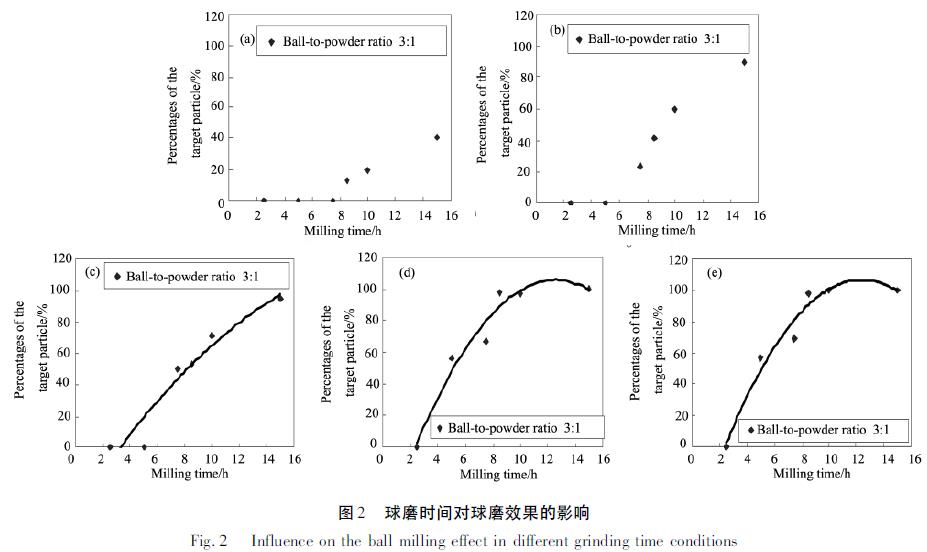
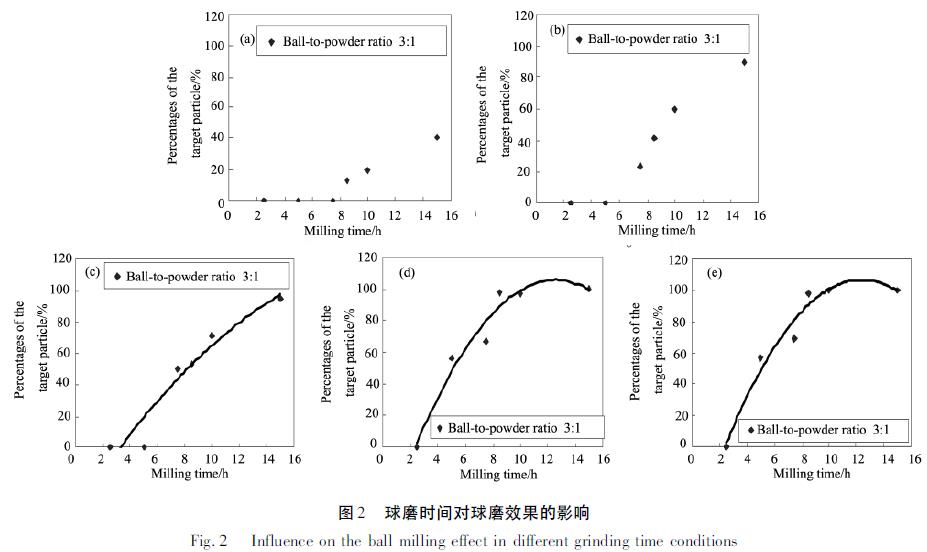
根据研磨目标,即粒径于10μm的颗粒百分比达到90%以上,可由球料比7∶1、9∶1、13∶1三组研磨数据趋势线,进行拟合计算,得到的必须研磨时间分别为13.7h、8.7h、8.5h,表明球料比大于9∶1时,必须研磨时间变化不大,即球料比已不再是控制因素,根据工程惯例,佳球料比为(9~11)∶1,综合图1、图2结果,为降研磨能耗,同时保证研磨效果,佳球磨时间为9~10h。
3.3烧结实验及分析
粉体球形度对陶瓷膜支撑体的烧结有直接影响:规整球形的Al2O3粉料可按球形堆积形式形成支撑体,此时孔隙率较,且球形颗粒间的接触面较小,支撑体强度略;有利的是:球形粉体所形成的孔道形状更为规则,流动阻力降,且支撑体强度整体更均匀。
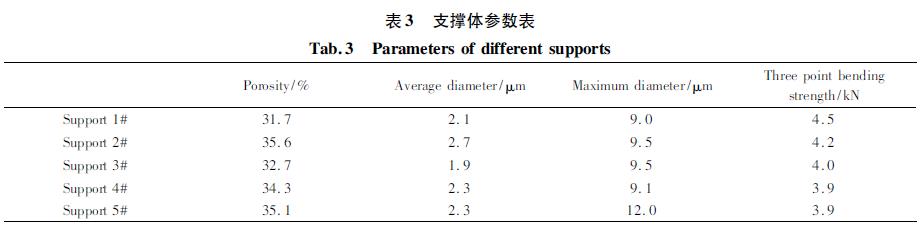
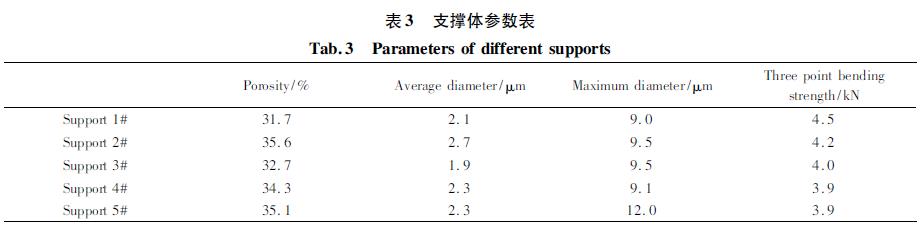
利用球料比9∶1、球磨时间10h所得粉体,按照一定烧成制度进行陶瓷膜支撑体制备,所得陶瓷膜支撑体的孔隙率为31.7~35.6%,大孔径为9~12μm,抗弯强度为3.9~4.5kN,具体参数见表3,达到已工业化的陶瓷膜支撑体的参数水平,表明优球磨条件下得到的粉体满足支撑体制备需求,与丁贯宝等[10]报道的颗粒级配实验结果符合。
4结论
(1)湿法球磨所得粉体球形度较好,满足直接用于烧结法陶瓷膜支撑体制备需要;
(2)实验结果表明,佳湿法球磨条件为:球磨时间9~10h,球料比(9~11)∶1,此时所得粉体粒径小于10μm者累计达到90%以上,球磨时间于有关文献报道的优时间约30%,节能效果明显,粉体制备成本降。