新闻中心
纯水型凹印油墨生产技术
作者:admin日期:2020-07-17阅读
纯水型凹印油墨是以水为溶剂制备而成的液体状油墨,其大特点是不含挥发性溶剂,具有、无刺激性气味等优点,节能减排,环境污染小,近年来逐渐受到人们的青睐,被广泛应用于绿色包装产业中,尤其是在呼声日益高涨的今天,已经成为一种新型的“绿色”印刷耗材,具有广阔的市场前景。将实验室成功研发的纯水型凹印油墨[4—5]进行产业化,需要对油墨生产工艺的关键技术进行研究,以确保生产的油墨质量。油墨的生产质量主要取决于分散性,针对凹印油墨生产使用多的卧式砂磨机,为了得到分散性能良好的油墨,要使砂磨机达到理想的运动形式,这与油
墨生产的预分散工艺、研磨基料颜基比(生产基墨时颜料和连接料的质量比)、进料速度、砂磨机的研磨次数密切相关。干燥性是水性油墨亟待解决的问题,为提高水性油墨的干燥性,需要在油墨中添加干燥剂,但干燥剂的加入不能影响油墨的质量,还需要有合适的干燥剂添加工艺。
1 实验
1.1 材料和仪器
实验使用颜料为联苯胺黄、艳红6BW、酞菁蓝、碳黑、钛白粉,实验使用树脂为丙烯酸树脂AZR,S-2916,S-2919,实验使用的助剂为分散剂、消泡剂、流平剂、蜡乳液,等,实验使用的溶剂为去离子水。主要仪器:JB2 高速搅拌机、SMZ 20-1 型卧式砂磨机、SMB-0.75 篮式研磨机(上海索维机电设备有限公司)、Microtrac S3500 激光粒度分析仪(美国Microtrac 有限公司)、3 号察恩杯、氧化锆珠做为研磨介质。
1.2 测试方法
1.2.1 油墨分散性
油墨的分散性通过其粒径大小及其分布来表征,使用激光粒度分析仪进行测试。文中以95%油墨分布的大粒径来表示油墨粒径,粒径分布图横坐标表示粒子大小(μm),左边纵坐标表示累积分数(%),右边纵坐标表示频度分数(%)。
1.2.2 油墨粘度
使用3 号察恩杯测量油墨粘度(s)。
1.2.3 油墨干燥性
采用GB/T 13217.5—2008 测试油墨干燥性,即使用压痕法的方式,使用刮板细度计进行测试,得出油墨的初干性(mm)、彻干性[6](s)。
1)初干性的测量:在温度为25 ℃,相对湿度为(65±5)%的环境中,取适量油墨于刮板细度仪槽的100 mm 处,迅速刮下,立刻按下秒表,经30 s 后用一张与刮板细度仪同宽的铜版纸条,其上端与刮板细度仪的上端对准,平贴凹槽上,用另一块刮板迅速刮一下,揭下纸,测量墨迹消失处到0 mm 处未粘墨迹的长度,即初干性。
2)彻干性的测量:在温度为25 ℃,相对湿度为(65±5)%的环境中,取适量油墨放置于刮板细度仪100 mm 处(墨量以刮满槽为准),迅速刮下,立刻用一张铜版纸盖在其上,用另一块刮板刮下,从揭下纸开始,用手指触摸纸条的100 mm 处,墨迹不粘手后结束,所用时间则为彻干性。
1.2.4 油墨附着力[7]
采用规格为20 mm×20 mm 的3M 胶带粘贴在印刷品上,样品下面放一张规格为10 mm×10 mm 的100个面积为1 mm2 的方格纸,用大小恒定的力将胶带从塑料表面以90°的方向撕下,计算剩余油墨所占方格纸格子数目的比例来评价附着力。纯水型塑料凹印油墨的附着力指的是在BOPP 塑料薄膜上的附着力。
1.2.5 油墨VOCS 含量
纯水型凹印油墨VOCs 含量依据GB26395—2011 进行测试。
1.2.6 油墨重金属含量
纯水型凹印油墨重金属含量依据 EN 71-3:2013进行测试。
1.2.7 油墨大印刷速度
在普通凹版印刷机上,烘箱温度为80 ℃时,印刷品完全干燥不粘连的快开机速度即为大印刷速度。
2 实验结果与分析
文中的研究方法与过程以纯水型凹印塑料青油墨为例进行说明,其他颜色油墨的研究方法相同。
2.1 预分散条件对油墨性能的影响
纯水型凹印油墨生产过程的1 步就是将原料按一定比例配制的混合物进行预分散,目的是将各种油墨的组分初步的混合,为后续的研磨工序做准备。预分散的时间和速度对油墨的分散性和粘度等性能有一定的影响。
2.1.1 预分散速率
油墨生产时预分散多使用高速叶轮分散机[8—9],采用不同转速分别对同一质量分数的油墨原料进行预分散,预分散时间为30 min,经过相同研磨条件生产基墨,再添加相同的成膜树脂后配制成墨,分别取样进行油墨分散性和粘度的检测,结果见图1。由图1 可以看出,基墨预分散时随着所采用的高速叶轮分散机转速的增加,生产出油墨的粒径有逐渐变小的趋势,且粒径分布也逐渐变均匀,当转速为500 r/min时,95%的油墨粒径分布在1.53 μm 以内,粒径分布范围较宽,粒径分布不均匀,当转速为2000 r/min 时,95%的油墨粒径分布在0.51 μm 以内,且粒径分布狭窄且均匀。转速从1500 r/min 开始,油墨粒径减小和粒径分布变窄的趋势减缓,趋于稳定。预分散可帮助连结料对颜料的润湿,为了使油墨具有良好的分散性,要求研磨前连结料应充分润湿颜料[10]。颜料和连结料在叶轮高速的剪切之下,随着转速的增加,颜料被连接料润湿得越来越充分,在后续的研磨过程中,连结料对颜料形成更加均匀的分散体系,分散性越好,因而产出的油墨分散性能更佳,粒径分布也更为合理。
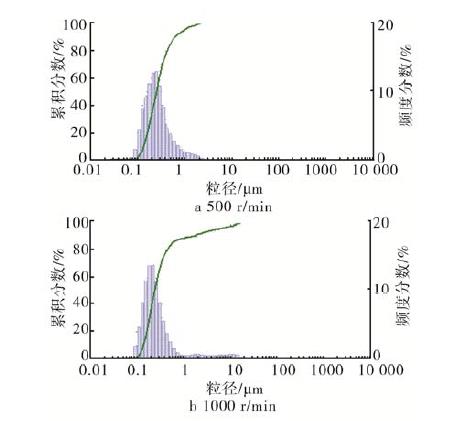
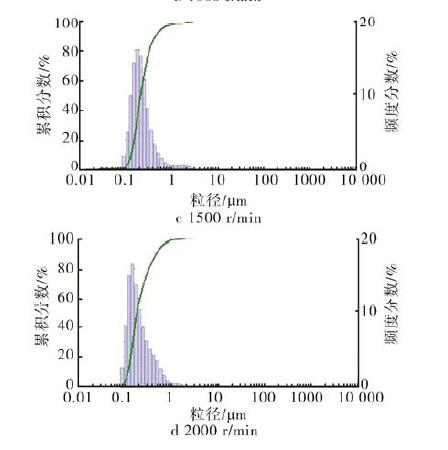
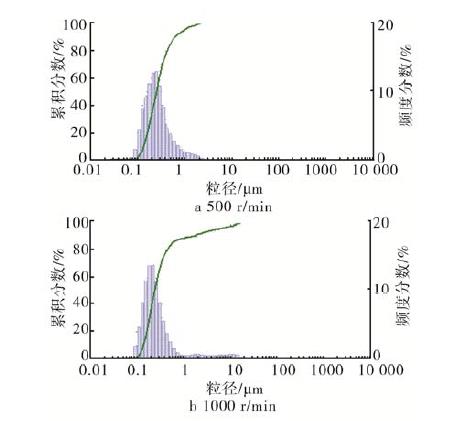
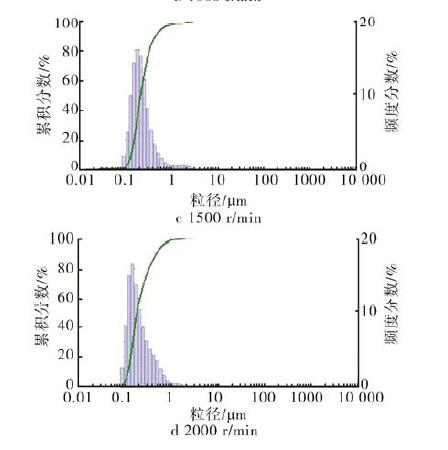
不同预分散速度下的油墨粒径和粘度见图2,随着预分散时所采用的高速叶轮分散机转速增加,生产出油墨的粘度逐步下降,但从1500 r/min 开始,油墨的粘度趋于稳定。当转速为500 r/min 时,油墨粘度为25 s,转速在1500~2000 r/min 时,粘度接近20 s。生产油墨的粘度与分散性相关,分散性好的体系的粘度于分散性差的体系。由图2 可知,当转速达到1500 r/min 时,所生产的油墨的粒径可达到0.51 μm,分散性良好,满足纯水型凹印油墨印刷工艺的要求,因此,可将1500 r/min 确定为油墨生产预分散时高速叶轮分散机的转速。
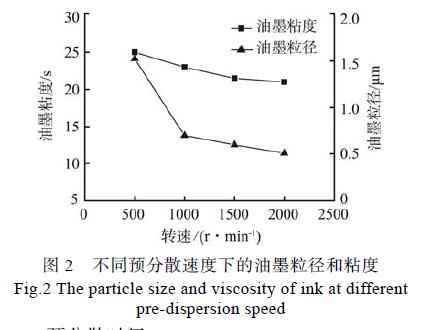
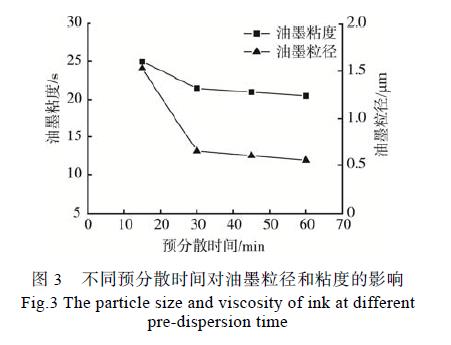
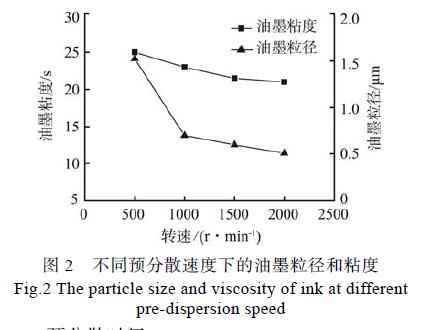
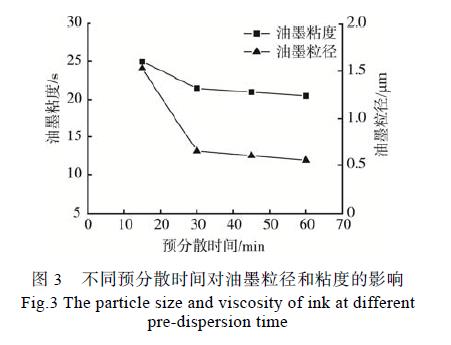
2.1.2 预分散时间
预分散时间对生产油墨的分散性也有较大影响,控制高速叶轮分散机的转速为1500 r/min,改变预分散时间对同一质量分数的油墨原料进行预分散,经过研磨生产基墨,添加调稀树脂之后配制成墨,分别取样进行油墨粒径分布和粘度的测量,见图3。
从图3 可以看出,基墨随着预分散时间的增加,油墨的粒径和粘度逐渐减小,但从30 min 开始,尤其在45 min 以后,生产的油墨粒径趋于稳定,粘度变化较小,说明油墨分散性达到良好状态。预分散时间决定了连结料对颜料的润湿程度,为了使连结料充分润湿颜料,保证生产油墨的分散性,需要有足够的预分散时间。预分散时间为30 min 时,可以使生产的纯水型凹印油墨具有良好的分散性。
2.2 研磨条件对油墨分散性的影响
将搅拌均匀和充分预分散的料浆放置在砂磨机中进行研磨。研磨是油墨生产的重要过程,其主要目的就是将颜料聚集体分散于连结料中,使之形成细颗粒的分散体,这也是油墨生产的主要目的[11]。为了生产分散性良好的油墨,必须使原材料处于佳研磨状态,并被充分研磨,这与研磨原料的颜基比、研磨时间有关。
2.2.1 颜基比
颜基比是指生产基墨时颜料和连接料的质量比,不同的颜基比生产的油墨性能差异较大。控制高速叶轮分散机的转速为1500 r/min,分散时间为30 min,对不同颜基比的基墨进行预分散,然后用相同研磨条件生产基墨,再添加相同的成膜树脂后配制成墨,分别取样进行油墨分散性和粘度的检测,见表1。
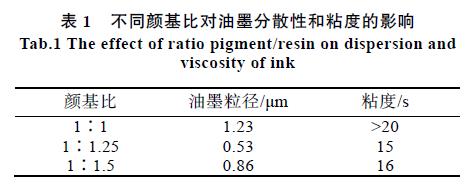
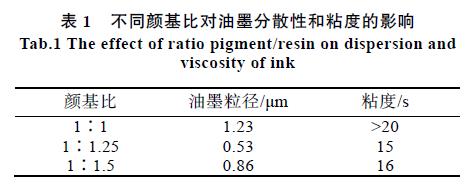
从表1 可以看出,采用不同颜基比研磨生产的油墨的粒径和粘度有较大差别,这是由于基墨生产实质是将颜料通过研磨的方式分散在连结料中,分散的过程实际上也是流动过程,达到佳流动点,油墨研磨时才能获得有效的剪切作用,分散才能达到佳状态。颜基比的改变意味着研磨树脂含
量发生变化,即研磨体系的粘度发生变化,使得剪切作用也不同[11]。为了使生产的油墨有良好的分散性,应采用佳颜基比来研磨生产基墨。在该生产条件和使用材料的情况下,采用1∶1.25 的颜基比来研磨生产纯水型凹印油墨,所得到的油墨粒径和粘度小,分别为0.53 μm 和15 s,说明分散效果达到佳。
2.2.2 进料速度
在纯水型凹印油墨研磨过程中,预分散好的混合物通过一个气动隔膜泵被压入研磨腔内,与研磨介质充分混合,进而被剪切和打碎,完成研磨过程。气动隔膜泵的工作气压决定了研磨机进料的速度,工作气压越大,进料速度越快。固定油墨生产的其他条件,改变气动隔膜泵的工作气压,即改变研磨
机进料速度来研磨生产基墨,并添加相同的成膜树脂配制成墨,测试油墨的粒径分布和粘度,见图4。
从图4 可以看出,随着隔膜泵工作气压的逐渐,即进料速度越来越大,油墨的分散性越来越差,进料速度小时,95%的油墨粒径分布在0.72 μm 以下,而大进料速度研磨出的油墨,95%的油墨粒径分布在1.68 μm 以下,分散性较差。进料速度越大时,油墨在砂磨机中被研磨的有效时间就越短,导致油墨的分散性欠佳,为了生产分散性良好的油墨,进料速度不能过高,即隔膜泵工作气压不能太大。
从图4 可以看出,随着隔膜泵工作气压的逐渐,即进料速度越来越大,油墨的分散性越来越差,进料速度小时,95%的油墨粒径分布在0.72 μm 以下,而大进料速度研磨出的油墨,95%的油墨粒径分布在1.68 μm 以下,分散性较差。进料速度越大时,油墨在砂磨机中被研磨的有效时间就越短,导致油墨的分散性欠佳,为了生产分散性良好的油墨,进料速度不能过高,即隔膜泵工作气压不能太大。
2.2.3 研磨次数
油墨原材料经过研磨机一次研磨往往不能得到良好的分散效果,需要多次研磨。将预分散好的浆料通过气动隔膜泵压入研磨腔内进行研磨,共研磨4次,测试每一遍研磨后的油墨的粒径分布,见图5。
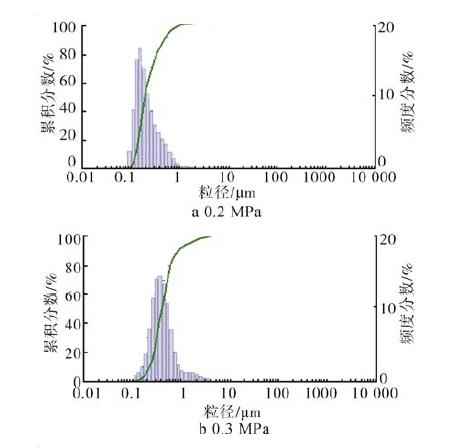
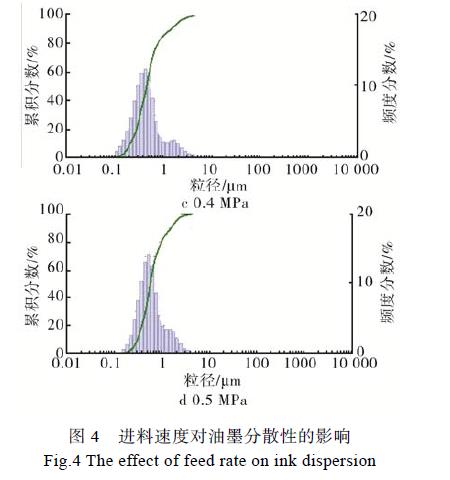
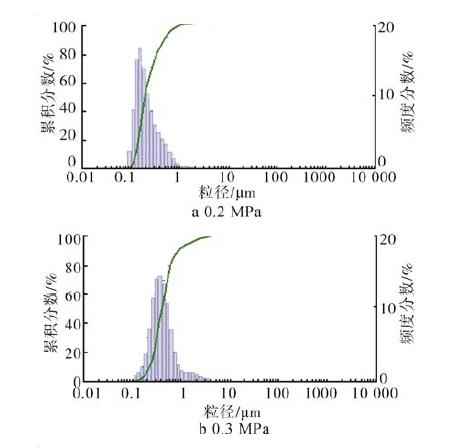
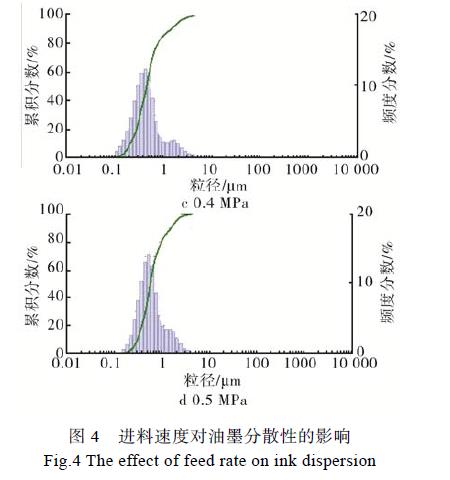
由图5 可以看出,随着研磨次数的增加,油墨的粒径逐渐减小,粒径分布的范围逐渐变窄。研磨次数越多,油墨原材料被研磨的时间越长,颜料被连结料分散得越充分,分散性越好。经过4 遍研磨后,95%的油墨粒径分布在0.99 μm 以下,分散性良好。
2.3 干燥剂添加工艺对油墨性能的影响
纯水型凹印油墨的溶剂是纯水,水的比热容较大,挥发速度不及醇类、酯类等溶剂,油墨被转移到承印材料表面时不易干燥,使得油墨在印刷时印刷机速度较慢,大地限制了印刷厂的生产效率,这也在很大程度上限制了纯水型凹印油墨的研发和推广[12—14]。为解决纯水型凹印油墨的干燥性问题,研制出能提高油墨干燥速度的干燥剂,该干燥剂为固体粉末[15]。在初期的实验中,直接将干燥剂加入纯水型凹印
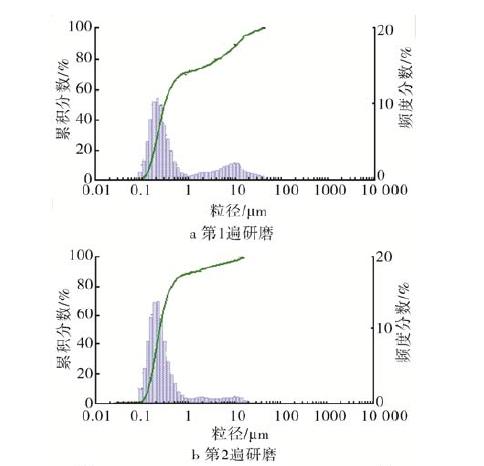
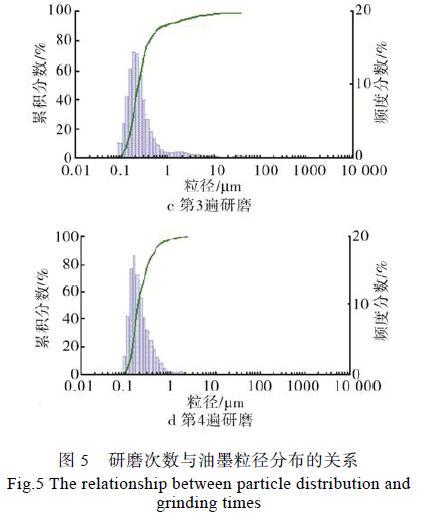
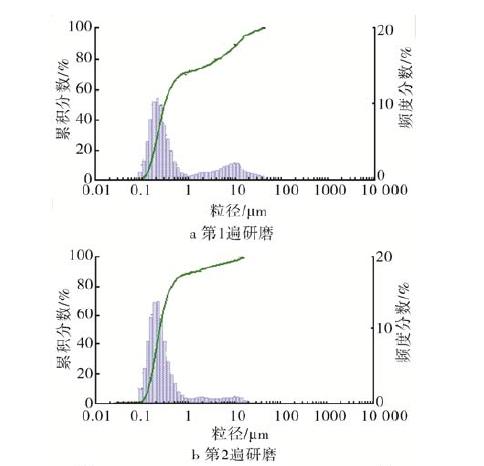
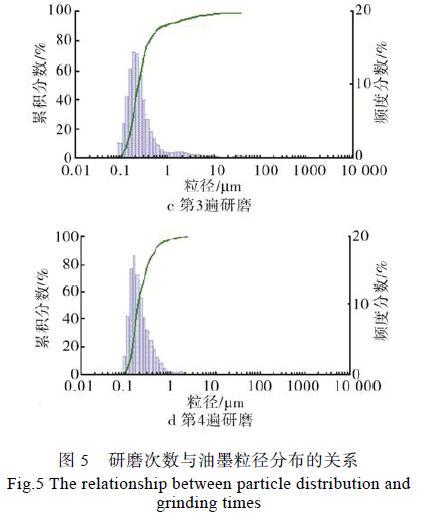
油墨中,所制备的干燥剂密度非常小,同时颗粒度很小,使其表面能较高,干燥剂非常容易漂浮在油墨表面,不能与油墨体系互溶,因此,将干燥剂粉末加至含有表面活性剂的水性丙烯酸乳液中。由于干燥剂是固体粉末,加入后易使油墨粒径变大,油墨转移性能变差,从而影响油墨的印刷质量。为了使干燥剂能很好地分散在油墨体系中,需要探讨其添加方式及工
艺。
2.3.1 干燥剂添加方式
采用2 种方式将干燥剂加至丙烯酸乳液:采用搅拌机将干燥剂分散在丙烯酸乳液中,分散时间为30 min;对预分散的干燥剂乳液采用篮式研磨机研磨30 min,转速为1000 r/min。将2 种方式制备的干燥剂乳液加入油墨中,测试油墨粒径分布,见图6。
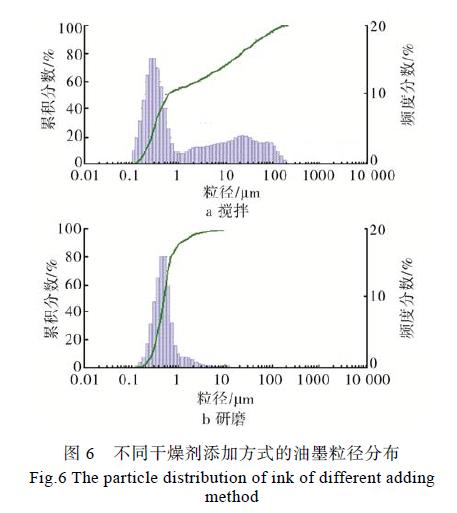
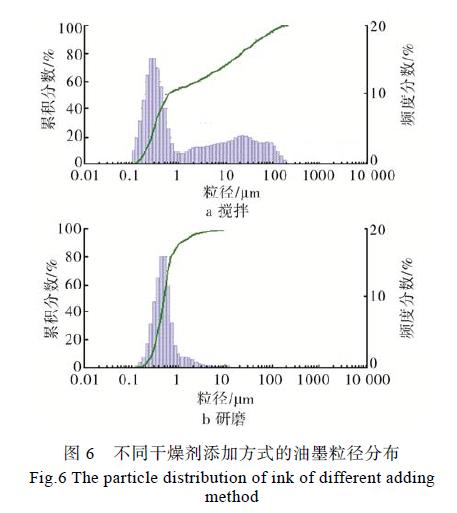
由图6a 可以看出,在油墨中添加采用搅拌方式制备的干燥剂乳液,会造成油墨颗粒大,95%的粒径分布在88 μm 以下,严重影响印刷质量,油墨转移性能差。由图6b 可以看出,在油墨中添加采用研磨方式制备的干燥剂乳液,95%的粒径分布在8.4 μm以下,颗粒明显减小,满足凹版印刷油墨转移的要求,可保证印刷质量。这是因为研制的干燥剂是固体粉末,用搅拌机将其与乳液混合,只能使乳液润湿干燥剂,干燥剂聚集体并没有得到很好的分散,必须在有效的剪切力作用下,即通过研磨,才能使干燥剂在油墨中有良好的分散性。
2.3.2 研磨时间
采用研磨方式分散干燥剂,与颜料分散类似,其分散性也与研磨时间有关。对预分散的干燥剂乳液采用篮式研磨机研磨,转速为1000 r/min,测试不同研磨时间所制备的干燥剂乳液的粒径分布,见图7。
从图7 可以看出,随着研磨时间的增加,干燥剂乳液的分散性越好,研磨时间为15 min 时,分散性很差,95%的粒径分布在40 μm 以下,且粒径分布范围较宽;经过60 min 的研磨后,95%的粒径分布达到3.67 μm 以下,已经接近生产油墨的粒径分布。研磨时间越长,分散剂被分散得越充分,分散性越好。将经60 min 研磨的干燥剂乳液加入油墨体系中时,与油墨有良好的互溶性。
2.4 生产油墨的主要性能
根据上述研究结果,采用佳生产工艺生产出纯水型凹印油墨,测试其性能。黄、品、青、黑、白的纯水型塑料凹印油墨的初始粒径分别为1.5,2,0.8,2.5,2 μm,粘度为20~25 s,初干性分别为10,11,10,11,10 mm,彻干性为70 s,附着力为90%~,大印刷速度为120 m/min,VOC 和重金属排放均符合标准;黄、品、青、黑、白的纯水型水松纸凹印油墨的初始粒径分别为1.5,2,0.8,2.5,2 μm,粘度为12~15 s,初干性分别为12,11,11,11,10 mm,彻干性为70 s,附着力为,大印刷速度为150 m/min,VOC 和重金属排放均符合标准。可以看出,采用文中的生产工艺生产出的纯水型凹印油墨性能良好,印刷速度较快,能满足凹版印刷要求,且油墨无VOC、重金属,属于油墨,可在我国包装
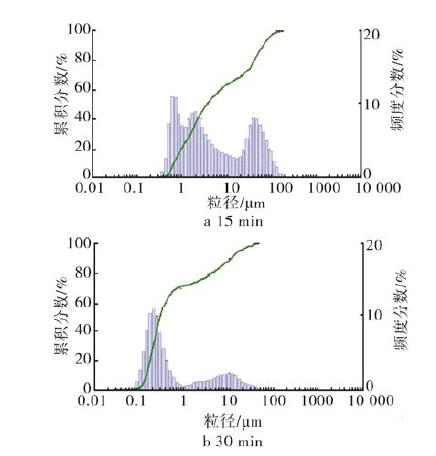
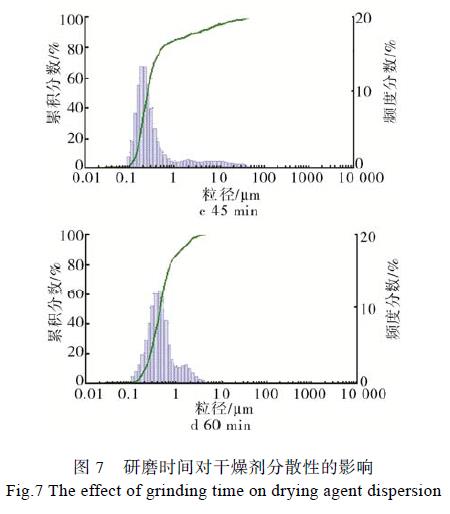
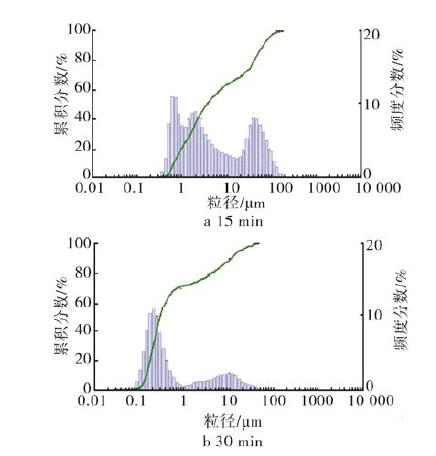
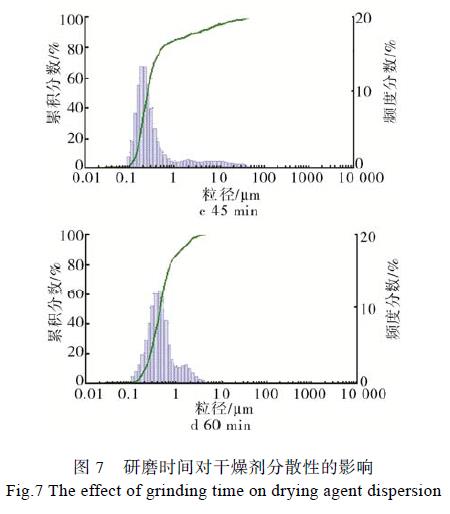
印刷行业全面推广,改变我国目前凹版印刷产生大量VOC 的现状。
3 结语
根据上述研究,针对实验室研制成功的纯水型凹印油墨的,利用现有的油墨生产设备,得到以下结论:为了生产出性能良好的纯水型凹印油墨,先应控制高速叶轮分散机转速为1500 r/min,对基墨浆料进行预分散,时间为30 min,基墨的颜基比为1∶1.25;然后对基墨采用卧式砂磨机进行研磨,控制进料速度的隔膜泵工作气压为0.2 MPa,经过4 遍研磨即可;干燥剂可用来提高纯水型凹印油墨的干燥性,先用搅拌机将其预分散至丙烯酸乳液中,然后用篮式研磨机在转速为1000 r/min 下研磨60 min 制备成干燥剂乳液,后添至油墨中;所生产的纯水型凹印油墨性能良好,可满足凹版印刷的要求。