新闻中心
球磨法氧化锆制备超细氧化铝
作者:admin日期:2020-09-24阅读
超细氧化铝具有耐高温、耐腐蚀、抗磨损、、高强度、高硬度、表面积大和绝缘性能好等特性,广泛应用在生物陶瓷、表面防护层材料、化工催化剂和催化剂载体、集成电路芯片、航空航天、红外吸收材料以及湿敏性传感器等方面。球磨法是常见的制备超细氧化铝粉体的方法,操作简单,成本廉,产量高。本章以工业级氧化铝粉体为原料,采用球磨法制备超细氧化铝粉末。通过控制变量确定不同尺寸氧化锆球的配比。通过正交实验确定球磨时间、球料比、球磨转速、助磨剂等影响因素对产物粒度的影响。
实验试剂
实验中所用试剂的规格和来源如表
2.1 所示。实验所用到的氧化锆球如图 2.1 所示,研磨介质用,氧化锆球(复合锆球)尺寸分别为 10mm、6mm、4mm、2mm。
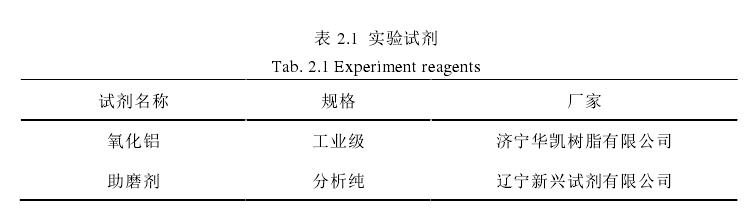
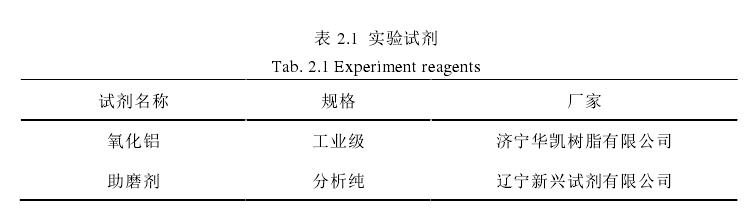
2.2.2 实验仪器
实验中所用的主要仪器和来源如表 2.2 所示。
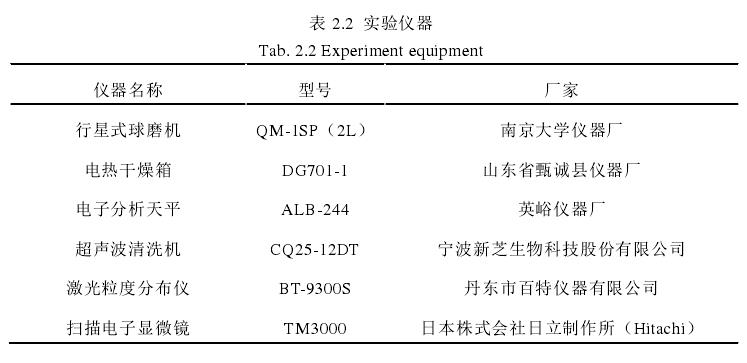
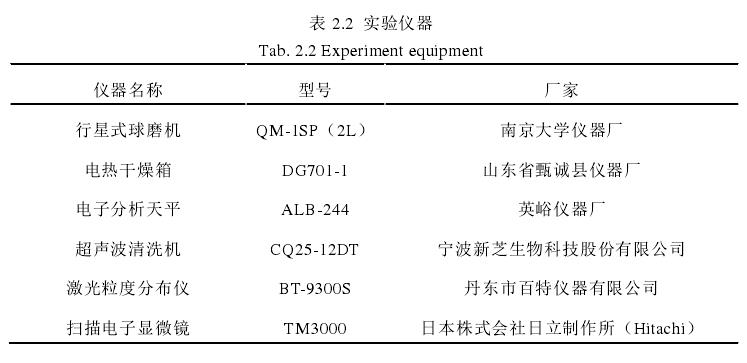
2.2.3 实验过程
(1)确定氧化锆球的配比称取平均粒径 79.26µm 的工业级氧化铝 7g,称取氧化锆球 28g,装入刚玉磨罐中,控制球料比为 4:1,球磨转速为 500r/min,球磨时间为 30min,在行星式球磨机中进行球磨。分别采用不同尺寸的氧化锆球,10mm、6mm、4mm、2mm,改变氧化锆球的配比,
(1)确定氧化锆球的配比称取平均粒径 79.26µm 的工业级氧化铝 7g,称取氧化锆球 28g,装入刚玉磨罐中,控制球料比为 4:1,球磨转速为 500r/min,球磨时间为 30min,在行星式球磨机中进行球磨。分别采用不同尺寸的氧化锆球,10mm、6mm、4mm、2mm,改变氧化锆球的配比,
考察产物粒径。
(2)正交实验
称取平均粒径 79.26μm 的工业级氧化铝 7g,称取氧化锆球 4mm 和 2mm(质量比为 1:3),装入刚玉磨罐中,控制一定的球磨时间、球磨转速和球料比,在行星式球磨机中进行球磨。通过改变球磨时间,球磨转速和球料比,设计正交实验,考察产物粒径。正交实验因素水平表如表 2.3 所示。
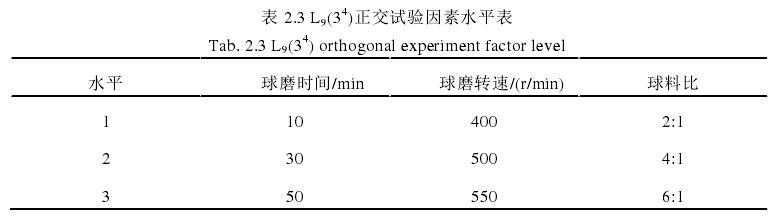
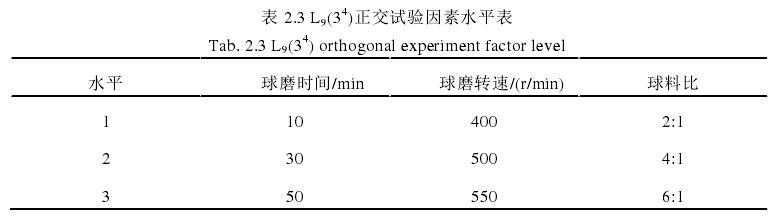
(3)湿法球磨
称取平均粒径 79.26μm 的工业级氧化铝 7g,称取氧化锆球 4mm 和 2mm(质量比为 1:3),装入刚玉磨罐中,球磨时间为 30min、球磨转速为 500r/min,球料比为 6:1,在行星式球磨机中进行球磨。通过改变助磨剂加入量,考察其对产物粒径和形貌的影响。
2.2.4 实验表征
(1)扫描电镜分析(SEM)
使用日本株式会社日立制作所(Hitachi)生产的 TM3000 型扫描电子显微镜,在标准模式加速电压 15kv 条件下,对氧化铝粉体的微观形貌拍摄照片,进行形貌分析。
(2)激光衍射粒度分析
使用丹东市百特仪器有限公司生产的 BT-9300S 型激光粒度分析仪,对不同工艺条件下球磨的粉体进行粒度分析,可同时得到中位径、粒度分布、比表面积等数据。测试条件为:测试范围为 0.1-716μm,重复性误差<1%,遮光率范围为 10-15%,选取的分散介质为水,采用连续测定,取 3 次测定结果的平均数。
2.3 实验结果与讨论
2.3.1 氧化锆球的配比对产物的影响
1)氧化锆球的尺寸图 2.2 是未经球磨的工业级氧化铝粉末的粒度分布图。从图 2.2 中可以看出,球磨前的工业级氧化铝粉末的粒度分布范围窄,粒度大,其平均粒径达到 79.26µm,说明球磨前的工业级氧化铝粉体主要由一些大粒径的团聚体组成。
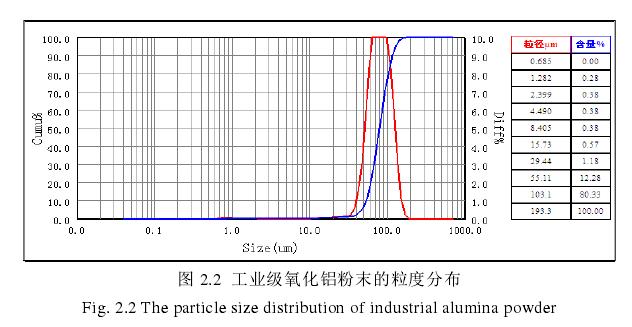
1)氧化锆球的尺寸图 2.2 是未经球磨的工业级氧化铝粉末的粒度分布图。从图 2.2 中可以看出,球磨前的工业级氧化铝粉末的粒度分布范围窄,粒度大,其平均粒径达到 79.26µm,说明球磨前的工业级氧化铝粉体主要由一些大粒径的团聚体组成。
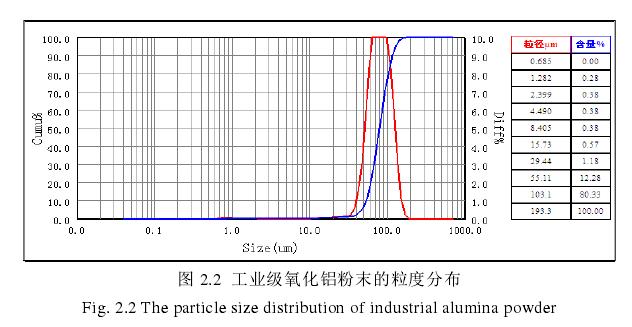
图 2.3 是在球磨转速为 500r/min、球磨时间为 30min、球料比为 4:1 的情况下,采用不同尺寸的氧化锆球研磨工业级氧化铝粉末的粒度分布图。球磨后的粉体粒度分布范围宽,粒度比较小。由图 2.2 和图 2.3 进行比较可以得出,经过氧化锆球研磨过的工业级氧化铝粉末比未经处理过的粉末的团聚体要小很多,粉末的粒度大幅度的减小,大部分团聚体已经打开,粉末颗粒得到了有效的细化。
从图 2.3 中也可以看出,随着氧化锆球尺寸的减小,小尺寸的颗粒逐渐增多,粒度逐渐减小,粉末颗粒的细化程度加大。但是随着氧化锆球尺寸的进一步减小,细化速度明显降,粉末粒度开始趋于稳定。当氧化锆球尺寸减小到 2mm 时,样品的大粒径反而。这是由于当氧化锆球尺寸过度减小时,其质量也将减小,对工业级氧化铝粉末的撞击力减小,从而降了样品的细化程度。
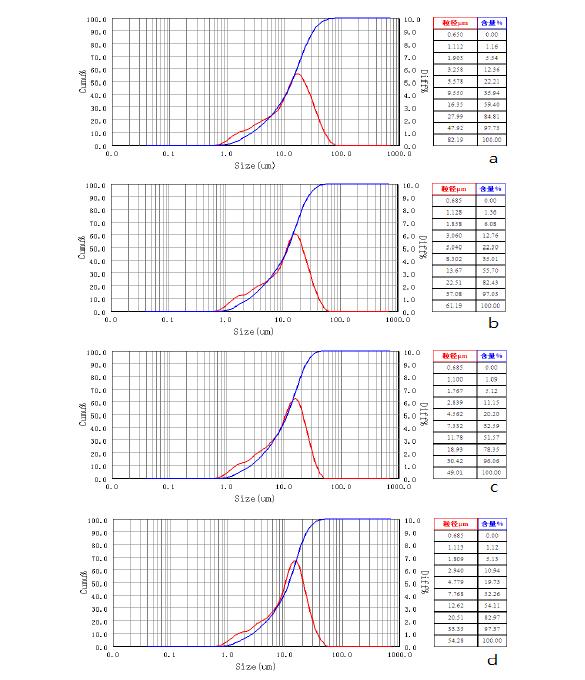
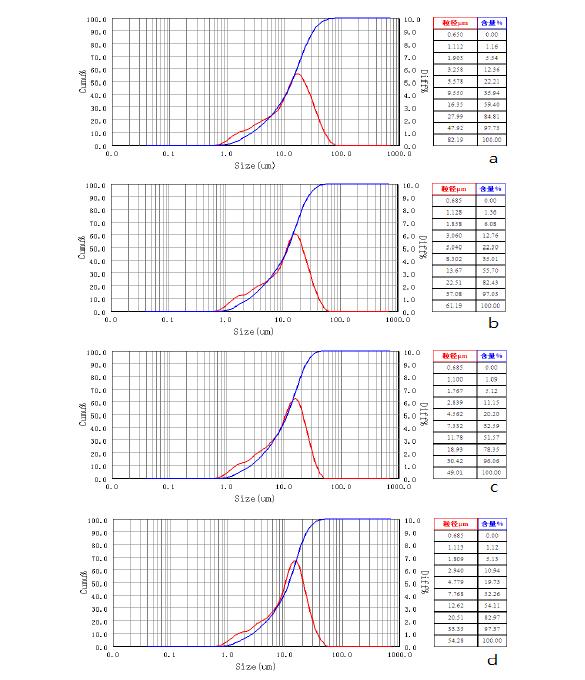
在球磨转速为 500r/min、球磨时间为 30min、球料比为 4:1 的情况下,以单独一种尺寸的氧化锆球所获得的产物中位径数据如表 2.4 所示。从图中可以直接看出不同尺寸的氧化锆球对产物中位径的影响,使用不同尺寸的氧化锆球球磨后获得的工业级氧化铝粉末的粒径不同,随着氧化锆球尺寸的不断减小,工业级氧化铝粉末的中位径也在不断减小。当采用 4mm 氧化锆球进行球磨时,所获得的工业级氧化铝粉末的中位径小。但当氧化锆球尺寸继续减小到 2mm 时,球磨后的工业级氧化铝粉末的中位径反而有的趋势。这是由于当氧化锆球尺寸减小时,其质量也将减小,对工业级氧化铝粉末的撞击力减小,从而难以对工业级氧化铝粉末进行充分的研磨。因此在转速 500r/min、球磨时间 30min、球料比 4:1 的情况下,称量 28g 的 4mm 氧化锆球,球磨所得的工业级氧化铝粉末的中位径小,为 11.41µm。
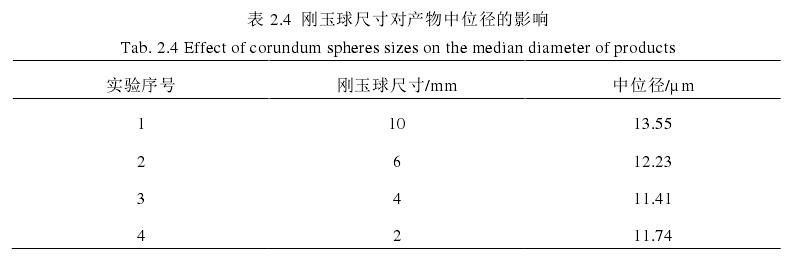
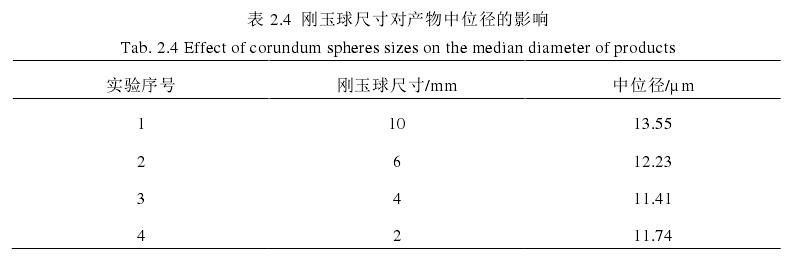
(2)两种氧化锆球配比
在球磨转速为 500r/min、球磨时间为 30min、球料比为 4:1 的情况下,以两种不同尺寸的氧化锆球作为磨料所获得产物的粒度分布如图 2.4 所示。从图中可以看出,经过球磨后,随着氧化锆球配比的不断改变,粉体的粒度分布范围越来越集中,粉体的大粒径不断减小。当采用 4mm 和
2mm 氧化锆球进行球磨时,粉体的粒度分布范围集中,粒度比较小,大粒径为为 54.18µm,说明经过氧化锆球研磨过的工业级氧化铝粉末的大部分团聚体已经打开,粉体得到了有效的细化,呈现单个颗粒分布。
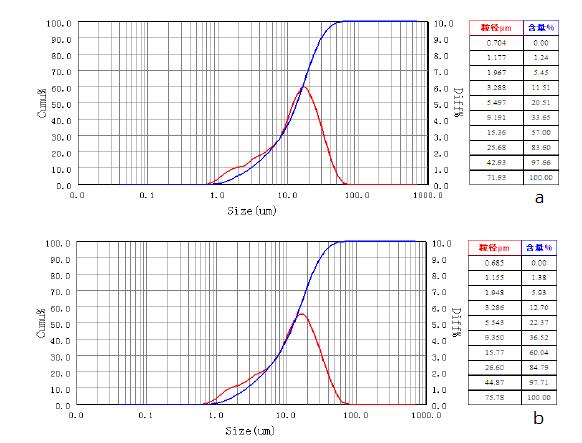
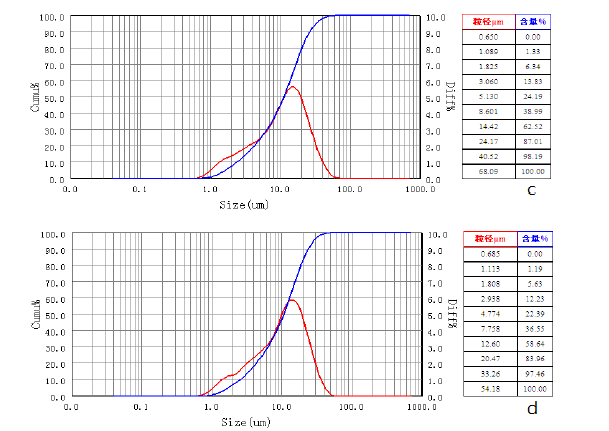
氧化锆球配比对产物粒度分布的影响
在球磨转速为 500r/min、球磨时间为 30min、球料比为 4:1 的情况下,以两种不同尺寸的氧化锆球作为磨料所获得产物的中位径数据如表 2.5 所示。从图中可以直接看出不同尺寸的氧化锆球对产物中位径的影响,使用不同组合尺寸的氧化锆球球磨后所获得的工业级氧化铝粉末的粒径不同,随着氧化锆球尺寸的减小,工业级氧化铝粉末的粒度不断变小。当采用尺寸为 4mm 和 2mm(质量比 1:1)的氧化锆球进行球磨时,所获得的工业级氧化铝粉末的中位径小,为 10.66µm。而只采用 4mm 氧化锆球球磨时,所获得的工业级氧化铝粉末的中位径为 11.41µm。因此在球磨转速为 500r/min、球磨时间为
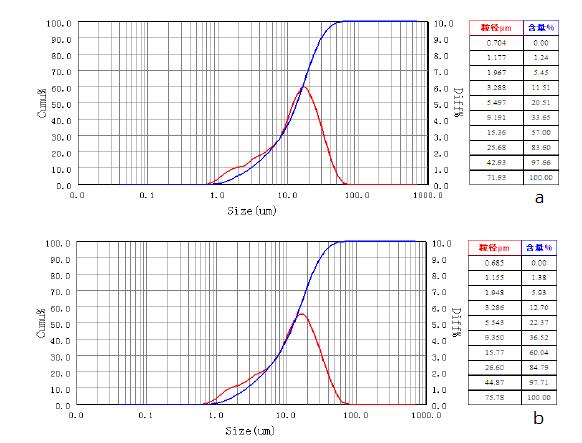
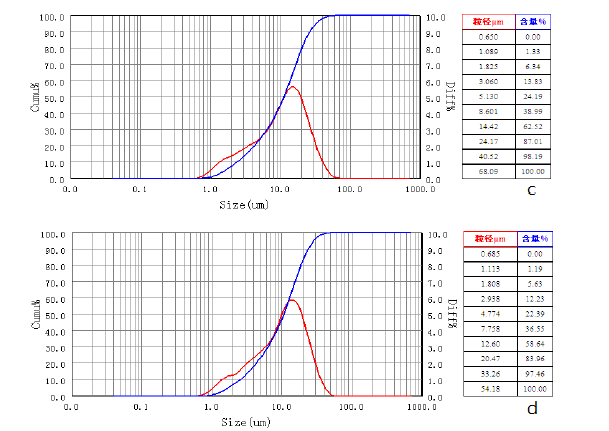
氧化锆球配比对产物粒度分布的影响
在球磨转速为 500r/min、球磨时间为 30min、球料比为 4:1 的情况下,以两种不同尺寸的氧化锆球作为磨料所获得产物的中位径数据如表 2.5 所示。从图中可以直接看出不同尺寸的氧化锆球对产物中位径的影响,使用不同组合尺寸的氧化锆球球磨后所获得的工业级氧化铝粉末的粒径不同,随着氧化锆球尺寸的减小,工业级氧化铝粉末的粒度不断变小。当采用尺寸为 4mm 和 2mm(质量比 1:1)的氧化锆球进行球磨时,所获得的工业级氧化铝粉末的中位径小,为 10.66µm。而只采用 4mm 氧化锆球球磨时,所获得的工业级氧化铝粉末的中位径为 11.41µm。因此在球磨转速为 500r/min、球磨时间为
30min、球料比为 4:1 的情况下,称量 14g 的 4mm 氧化锆球和 14g 的 2mm 氧化锆球,球磨所得的工业级氧化铝粉末的中位径小,为 10.66µm。
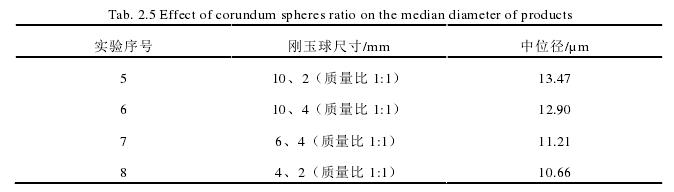
(3)三种氧化锆球配比
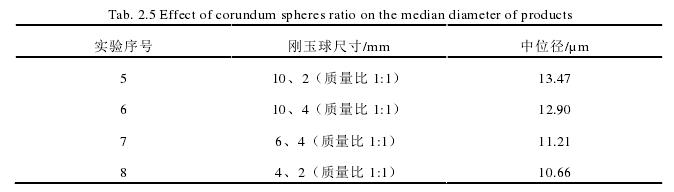
(3)三种氧化锆球配比
在球磨转速为 500r/min、球磨时间为 30min、球料比为 4:1 的情况下,采用三种不同尺寸的氧化锆球为磨料进行球磨所获得粉体的粒度分布如图 2.5 所示。从图中可以看出,粉体粒度分布范围比较窄,粒度比较小,说明球磨过的工业级氧化铝粉末大部分团聚体已经打开,呈现单个颗粒分布。采用 10mm、4mm、2mm 的氧化锆球作为磨料球磨后的粉体的大粒径为 68.09µm,采用 6mm、4mm、2mm 的氧化锆球作为磨料球磨后的粉体的大粒径为 71.93µm,两种产物的大粒径都大于采用 4mm 和 2mm 氧化锆球进行球磨时所获得的粉体大粒径 54.18µm。因此从球磨后粉体的粒度考虑,采用
4mm 和 2mm 的氧化锆球进行球磨较为适宜。
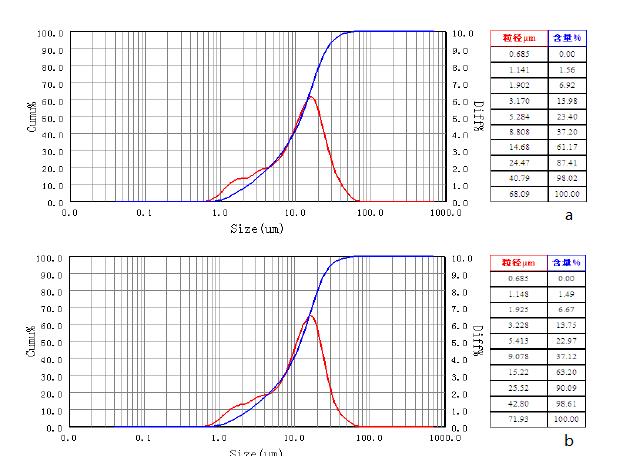
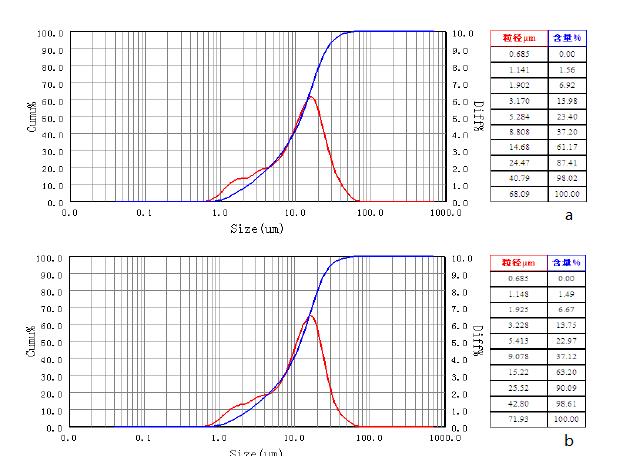
在球磨转速为 500r/min、球磨时间为 30min、球料比为 4:1 的情况下,以三种不同尺寸的氧化锆球作为磨料球磨后的样品的中位径数据如表 2.6 所示,可以直接看出氧化锆球尺寸对产物中位径的影响。由表 2.6 可以看出,采用三种不同尺寸的氧化锆球进行球磨后所获得的粉体的中位径比较小,但是采用 4mm 和 2mm 的氧化锆球球磨后的粉体的中位径为 10.66µm,采用三种不同尺寸的氧化锆球反而比采用 4mm 和 2mm 两种尺寸的氧化锆球进行球磨所获得的粉体的粒度大。所以,从促进粉体细化的角度考虑,采用 4mm和 2mm 两种尺寸氧化锆球来作为磨料进行球磨。
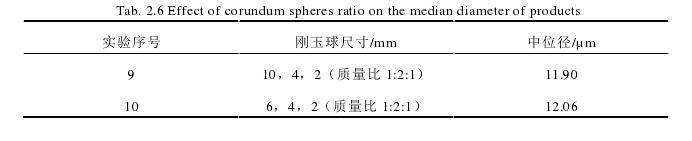
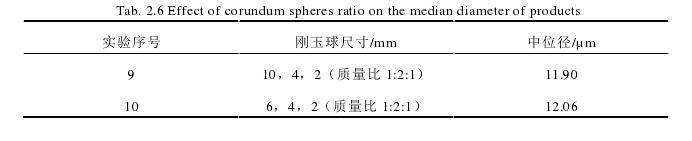
(4)氧化锆球的质量比
在球磨转速为 500r/min、球磨时间为 30min、球料比为 4:1 的情况下,以 4mm 和2mm 的氧化锆球作为磨料,采用不同的质量比进行球磨,所获得样品的粒度分布如图2.6 所示。从图 2.6 中可以得出,粉体的粒度分布范围比较窄,大部分颗粒的粒度小,说明经过氧化锆球研磨过的氧化铝粉末大部分团聚体已经打开,粉体得到了有效的细化,大部分粉体呈现单个颗粒分布。其中,采用 4mm 和 2mm(质量比为 1:3)的氧化锆球为磨料来进行球磨获得的粉体粒度分布范围更集中,粉体的粒度更加均匀。
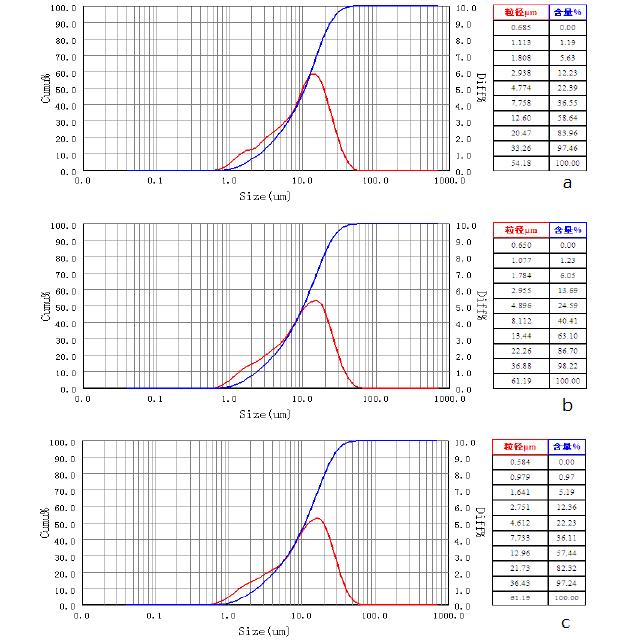
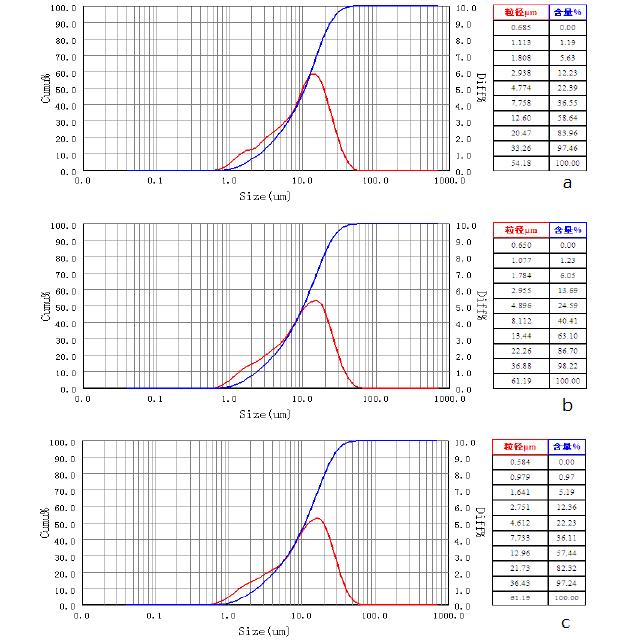
在球磨转速为 500r/min、球磨时间为 30min、球料比为 4:1 的情况下,以 4mm 和2mm 尺寸的氧化锆球作为磨料,采用不同的质量比,所获得的产物的中位径如表 2.7 所示,可以看出质量比不同的氧化锆球对产物中位径的影响。随着 2mm 氧化锆球的数量的增加,产物的中位径减小。当采用 4mm 和
2mm(质量比 1:3)的氧化锆球进行球磨所获得的氧化铝粉末的中位径小,所以选用 4mm 和 2mm(质量比为 1:3)的氧化锆球进行球磨适宜。因此在球磨转速为 500r/min、球磨时间为 30min、球料比为 4:1 的情况下,称量 7g 的 4mm 氧化锆球和 21g 的 2mm 氧化锆球,球磨后的工业级氧化铝粉末中位径小,为 10.02µm。
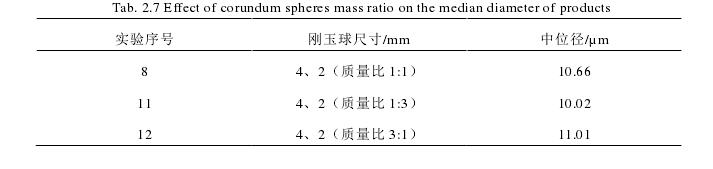
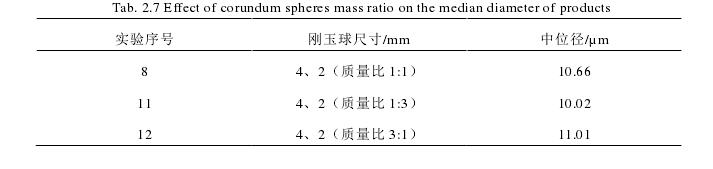
2.3.2 球磨时间、球磨转速、球料比对产物的影响
为探讨球磨时间、球磨转速及球料比等工艺参数对工业级氧化铝粉末的中位径的影响,采用了正交试验,正交表为 L9(34),正交试验数据如表 2.8 所示。因素中:球磨时间 A 分别为 10、30、50min;球磨转速 B 分别为 400、500、550r/min。球料比 C 分别为 2:1、4:1、6:1。
正交试验结果如表 2.9 所示,优工艺参数组合为 A3B3C3,即球磨时间为 50min,球磨转速为 550r/min,球料比为 6∶1。根据差分析,影响因素的大小顺序为球磨时间>球料比>球磨转速,且球磨时间和球料比对工业级氧化铝粉末的中位径的影响都非常显著。
(1)球磨时间
在试验的选择范围内,球磨时间对工业级氧化铝粉末的中位径的影响是大的。在球磨过程中,夹在氧化锆球之间的工业级氧化铝粉末被氧化锆球球磨和撞击,氧化铝粉末产生裂纹,继续球磨,裂纹逐渐扩大,并终破碎,从而使氧化铝粉末得到细化。随着球磨时间的延长,氧化铝粉末被氧化锆球球磨和撞击的频率,有利于粉末的细化,氧化铝粉末的粒度能得到有效的降。当球磨时间过短时,粉末难以得到氧化锆球充分的球磨和撞击,导致粉末的粒度较大。
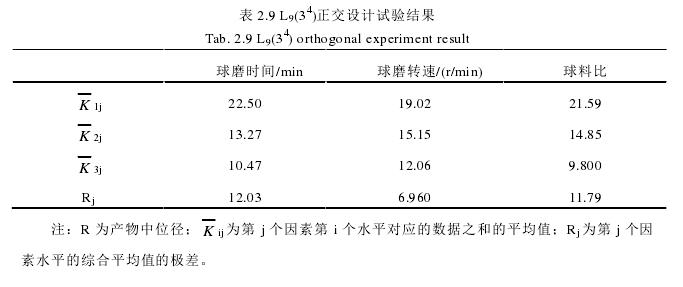
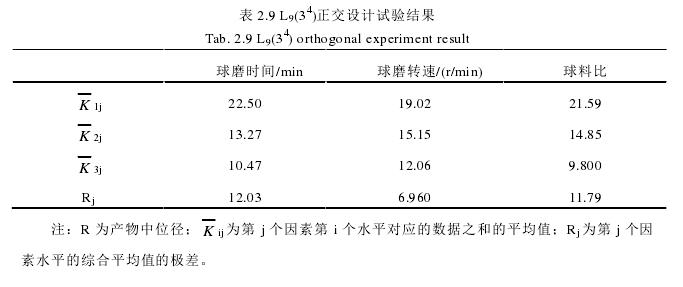
(2)球磨转速
在试验选择范围内,球磨转速对氧化铝粉末的中位径的影响是小的。在球磨过程中,球磨转速决定了的输入效率。球磨转速的提高增加了氧化锆球与工业级氧化铝粉末的碰撞频率和强度,促进了氧化铝粉末的细化,能够较为有效的降氧化铝粉末的粒度。而球磨转速过时,降了氧化锆球与工业级氧化铝粉末的碰撞频率和强度,
未获得足够的工业级氧化铝粉末难以得到有效的细化,粉末的粒度较大。
(3)球料比
在球磨过程中,夹在氧化锆球之间的工业级氧化铝粉末受到氧化锆球的撞击作用下,产生形变、断裂和细化。因此,工业级氧化铝粉末在氧化锆球空隙中的填充率显著得影响了球磨效率和粉末粒度。氧化锆球之间间隙的体积大,填充率过大,过多的工业级氧化铝粉末了氧化锆球之间的撞击,降了球磨效率,降了氧化铝粉末细化程度;填充率过小,磨球之间氧化铝粉末太少,氧化锆球撞击氧化铝粉末的机会将减小,从而降了氧化铝粉末细化程度。
2.3.3 湿法球磨
(1)助磨剂对产物粒度分布的影响
在球磨转速为 500r/min、球磨时间为 30min、球料比为 6:1 的情况下,添加了不同量的助磨剂所获得的产物的粒度分布如图 2.7 所示。从图中可以看出,未添加助磨剂的工业级氧化铝粉末的粒度分布范围比较宽,粒度大。未加入助磨剂的工业级氧化铝粉末经过一段时间球磨后,在氧化锆球的球磨和碰撞作用下,氧化铝粉末容易包覆在氧化锆球表面,不能达到球磨的目的。
添加了助磨剂之后,工业级氧化铝粉末的细化效果十分明显。随着助磨剂添加量的增加,氧化铝粉末的粒度分布范围逐渐变窄,大粒径不断减小,中位径不断减小。在加入 10m L 助磨剂时,球磨后的粉体的大粒径为 30.57µm。说明添加了助磨剂球磨后的氧化铝粉末比未添加助磨剂的氧化铝粉末的团聚体少,添加了助磨剂的氧化铝粉末得到了有效的细化
但是随着助磨剂添加量的增加,粉体的大粒径反而逐渐。这说明助磨剂有一个适宜的用量范围,添加 10m L 的助磨剂更利于粉体的细化。过量的助磨剂会消耗球磨时氧化锆球对粉末的球磨和撞击,严重影响球磨效率,粉末的细化速度明显降,从而造成粉末的粒度过大。
(2)助磨剂对产物中位径影响
在球磨转速为 500r/min、球磨时间为 30min、球料比为 6:1 的情况下进行试验,助磨剂添加量对产物中位径的影响如图 2.8。从图 2.7 可以看出,未加入助磨剂时,工业级氧化铝粉体的粒度较大。这是由于,未加入助磨剂的氧化铝粉末经过一段时间球磨后,在氧化锆球的球磨和碰撞作用下,氧化铝粉末容易包覆在氧化锆球表面,不能达到研磨的目的。
添加了助磨剂之后,工业级氧化铝粉末的细化效果十分明显。随着助磨剂添加量的增加,氧化铝粉末粒度显著减小,在加入 10m L 助磨剂时,球磨后氧化铝粉末的中位径小。在球磨过程中,助磨剂吸附在氧化铝粉末表面,能够有效减弱粉体之间的相互作用力,有利于大粒径的颗粒受到氧化锆球的球磨和撞击,使得大颗粒产生裂纹,裂纹逐渐扩大,并终破碎,从而使细化过程更加容易进行,助磨剂在研磨过程中也起到了小颗粒重新团聚的作用,大大提高了球磨效率。
但是随着助磨剂添加量的不断增加,经过球磨后的工业级氧化铝粉末中位径逐渐增加。这说明助磨剂有一个适宜的用量范围,当用量高于 10m L 时,过量的助磨剂会氧化铝粉末被氧化锆球的球磨和撞击,严重影响球磨效率。因此助磨剂佳添加量为 10m L,此时经过球磨后的工业级氧化铝粉末的中位径为 4.664µm。
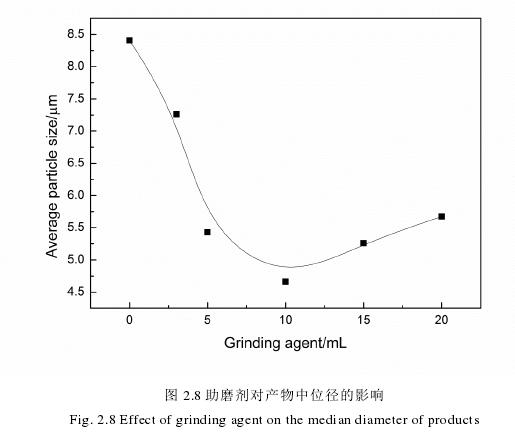
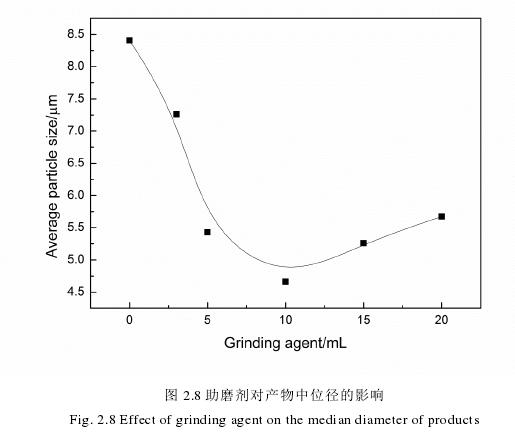
(3)助磨剂对产物形貌的影响
在球磨转速为 500r/min、球磨时间为 30min、球料比为 6:1 的情况下进行试验,采用不同助磨剂添加量的产物的 SEM 照片如图 2.9 所示。可以看出,未添加助磨剂的产物形貌不均匀,团聚现象严重。加入助磨剂后,促进了氧化锆球对于工业级氧化铝粉末的球磨和撞击,粉末的细化效果明显,粉末的粒径变小,颗粒尺寸比较均匀,团聚现象明显减少,改善了氧化铝粉末形貌的均匀性。但是随着助磨剂添加量的增加,粉体的形貌变得不均匀,又产生了团聚现象。这是由于过量的助磨剂会氧化锆球对于粉末的球磨和撞击,严重影响球磨效率,粉末的细化速度明显降,使得颗粒的粒径呈
现变大的趋势。因此,助磨剂的添加量要适当,否则既容易使产物团聚又浪费成本。在本实验条件下,助磨剂的添加量为 10m L 时佳。
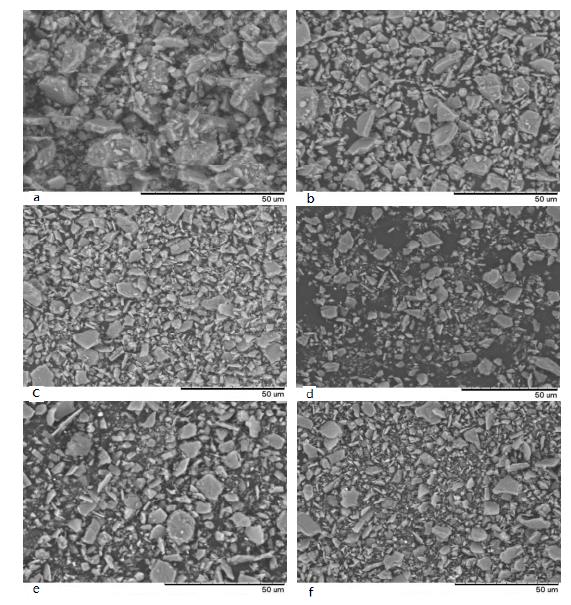
(3)添加助磨剂能够有效的提高球磨的细化效率,但是过量的助磨剂会消耗球磨。助磨剂的加入量要适当,助磨剂的佳用量为 10m L,能够得到中位径为 4.664µm的超细氧化铝粉末。
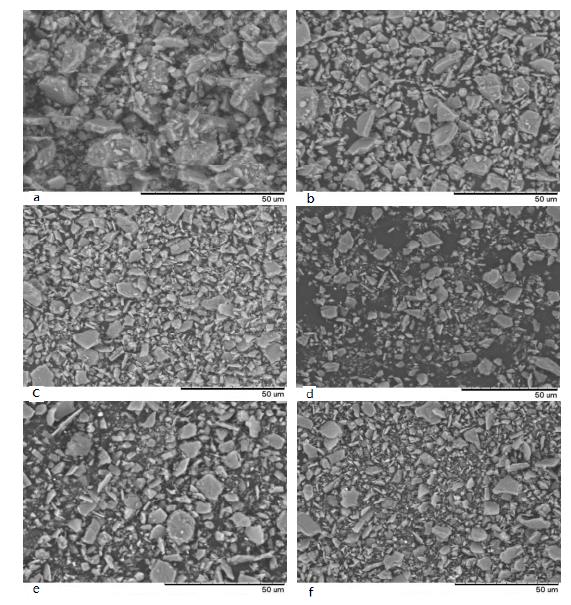
2.4 本章小结
以工业级氧化铝粉体为原料,采用球磨法制备了超细氧化铝粉末,研究了球磨过程中影响因素对于产物粒度分布、粒度和形貌的影响,获得如下结论:
(1)采用不同配比氧化锆球球磨后所得的工业级氧化铝粉末的粒径不同,采用 4mm和 2mm(质量比 1:3)两种尺寸氧化锆球进行球磨实验为佳,此时获得的氧化铝粉末的中位径为 10.02µm。
(2)球磨时间、球料比、球磨转速等工艺参数对制备超细氧化铝粉末有重要影响,影响因素的大小顺序为球磨时间>球料比>球磨转速,且球磨时间和球料比对氧化铝粉末的中位径的影响都非常显著。优工艺条件:球磨时间为50min,球磨转速为550r/min,球料比为 6∶1。
(3)添加助磨剂能够有效的提高球磨的细化效率,但是过量的助磨剂会消耗球磨。助磨剂的加入量要适当,助磨剂的佳用量为 10m L,能够得到中位径为 4.664µm的超细氧化铝粉末。