新闻中心
白云石湿法研磨制备造纸填料的工艺研究
作者:admin日期:2020-02-14阅读
研究r以白云石矿粉为原料制备造纸填料的湿法研磨工艺,通过在砂磨机转速为3000r/min下对研壤过程中主要影响因素的研究表明,影响研磨效果的因素依次为研磨介质与白云石质量比、研磨时间、分散剂用量。佳研磨条件为:矿浆浓度60%,研磨介质白云石质量比6:1,研磨时间45min,分散剂用量0.5%;研磨后的白云石粒径分布均匀,粒径小于2m的微粒可以达到66.2%,满足了造纸填料的要求。
白云石的化学式为CaMg(CO),属于三方晶系,主要应用于冶金、化工、建材、农业和等领域¨。采用不同的物理化学工艺处理,可以改变白云石的晶形、颗粒形貌和尺寸,影响白云石的物理化学性质,提高其作为颜料、分散剂或者充填材料的使用性能J。对自云石矿进行拣选、破碎、磨细后可制得白云石粉。白云石粉可在一定程度上取代橡胶、涂料、塑料等行业中的轻钙粉或重钙粉,具有广阔的发展前景。
国内造纸用填料主要有碳酸钙、滑石粉和高岭土等。随着废纸回用量的增加及中、碱性造纸的发展,碳酸钙填料(尤其是重质碳酸钙)因其良好的抄造性能、较好的施胶效果以及对纸张强度影响等优点,正逐步替代其他填料。我国白云石资源分布广泛、蕴藏丰富、优、易开采。白云石的晶体结构与方解石类似,价格廉,拥有较高的不透明度,经湿法研磨后可以部分代替重质碳酸钙作为造纸填料或用于制备复合材料,改善纸张性能,进而更加合理有效地利用资源,降成本。因此,对填料级白云石湿法研磨工艺的研究具有一定意义。
目前用作造纸填料的碳酸钙大多为55级至65级。本研究利用SK立式砂磨机,研究了分散剂用量、研磨介质与白云石质量比、研磨时问等条件对湿法研磨白云石的影响。通过粒径分析探讨了白云石用作造纸填料的适宜研磨工艺。

1.1原料与试剂
实验原料为工业级白云石,纯度94.68%,粒径小于2m的微粒占10%,由青岛某公司提供,主要化学成分分析见表1。

分散剂采用六偏磷酸钠,AR级,山东某公司提供。
研磨介质为直径1.2~2mm氧化锆珠,某公司制造。
1.2设备与仪器
SK立式砂磨机,常州自力化工机械有限公司制造;SediGraphm型全自动x光透射沉降粒度分析仪,美国Micromeritics公司制造。
1.3研究方法
1.3.1矿粉的研磨与分析
取200g白云石,按照研究方案设定的比例加入水和分散剂,搅拌均匀,与一定量的研磨介质一起加入砂磨机中,在3000r/min转速下进行研磨。按照设定的研磨时间取样,经100目筛筛分之后,通过粒度仪检测粒径分布情况。然后,根据不同条件下样品的粒径分布,分析各因素对研磨效果的影响。终采用正交实验法确定合理的研磨工艺。
1.3.2研磨时问的确定
当矿浆浓度为60%、分散剂用量为0.5%、研磨介质与白云石质量比为5:1时,按照上述实法,每隔10min取样,筛分后通过粒度仪检测粒径分布情况,测得2m以下微粒所占比例达到55%~65%即为所需研磨时间。
1.3.3分散剂用量的确定
以矿浆浓度为60%,研磨介质与白云石质量比为5:1,分散剂用量分别为0、0.3%、0.5%、0.7%、0.9%的条件进行实验。按照1.3.1所述方法,研磨40min后取样,筛分后测其粒径分布情况,选取2Ixm以下微粒所占比例较高的分散剂用量进行正交实验。
1.3.4矿浆浓度的确定
设定分散剂用量为0.5%、研磨介质与白云石质量比为5:1,参照同类矿物的矿浆参数,将矿浆中物料的质量分数分别选定为50%、55%、60%和65%,按照1.3.1所述方法,研磨40rain后取样,筛分后测其粒径分布情况,选取2m以下微粒所占比例高的矿浆浓度进行后续实验。
1.3.5研磨介质与白云石质量比的确定
设定分散剂用量为0.5%,矿浆浓度为60%,参照同类实验结果],分别选取研磨介质与白云石的质量比为3:1、4:1、5-1、6:1、7:1进行实验,研磨40min后取样,筛分后测其粒径分布情况,选取2Ixm以下微粒所占比例高的研磨介质与白云石质量比进行正交实验。
2结果与分析
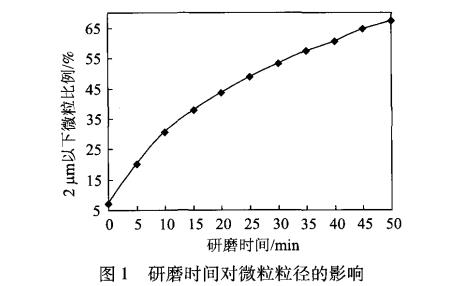
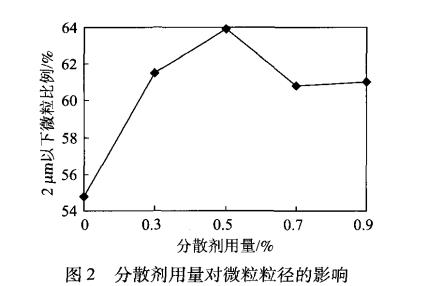
2结果与分析
2.1研磨效果的影响因素
2.1.1研磨时间对微粒粒径的影响
湿法研磨过程中,在高速旋转状态下研磨介质对白云石微粒产生了撞击、挤压和破碎作用,达到了研磨的目的J。随研磨时间的延长,白云石微粒的粒径不断减小。研磨后白云石微粒粒径与研磨时间的关系如图1所示。
由图1可以看到,在研磨0~35min时,白云石微粒粒径减小较快,2m以下微粒所占比例由7.8%升至57.6%;在35~45min时,2Ixm以下微粒增加速率逐渐降,所占比例由57.6%增至64.7%,满足了造纸填料的要求;当继续研磨至50min时,2Ixm以下微粒达到67.4%。随研磨时间的延长,白云石粒径不断减小,比表面积相应,矿浆黏度也提高。此时,微粒受到研磨介质的冲击力逐渐减弱,小颗粒增加速率减慢。因此,可以选择35、40、45rain这3个时问作为正交实验的时间水平。
2.1.2分散剂用量对微粒粒径的影响
湿法研磨过程中,随颗粒尺寸的减小,其相互之间的引力,致使产生团聚,矿浆黏度也随之提高。因此,在研磨时,加入分散剂有助于改善粉体的分散稳定性和流动性,同质颗粒之间出现团聚,降矿浆黏度,改善研磨效率¨。微粒粒径与分散剂用量的关系如图2所示。
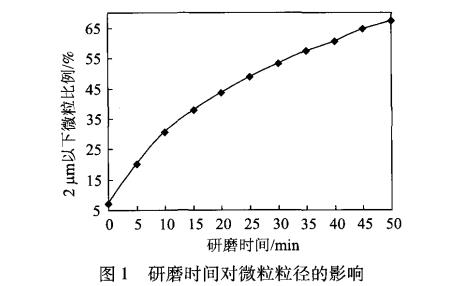
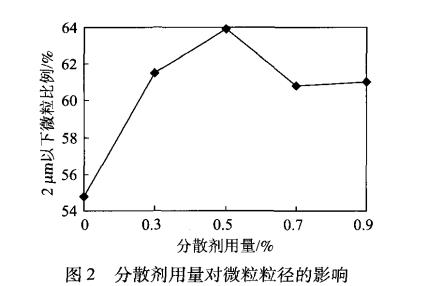
由图2可知,随分散剂用量的增加,2m以下微粒所占的比例先是迅速增加,而后开始降;在分散剂用量为0.5%时,其达到大值(63.9%)。这是因为随六偏磷酸钠用量的增加,微粒表面的电荷密度升高,粒子之问的斥力相应,使得体系的分散性得以改善。当分散剂用量增至0.7%及0.9%时,研磨后的微粒粒径在2Ixm以下比例分别降至60.8%和61.0%;当分散剂用量继续增加时,过剩的六偏磷酸钠分子会相互桥联,形成网状结构,限制了微粒之间的运动,致使流变性变差。因此,可以选择分散剂用量为0.4%、0.5%、0.6%进行正交实验。
2.1.3矿浆浓度对微粒粒径的影响
矿浆浓度也是影响白云石研磨状况的重要因素。
随矿浆浓度的升高,黏度变大而导致分散更为困难;而矿浆浓度如果过,则会减弱介质对白云石微粒的冲击和磨剥作用,影响研磨效果。实验结果如图3所示。
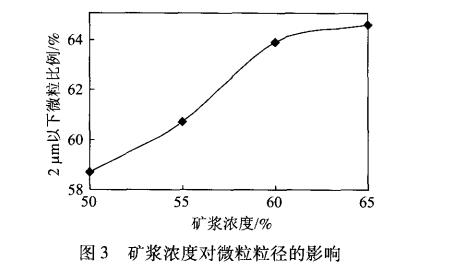
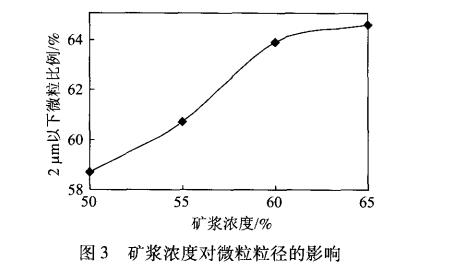
由图3可知,在研磨时间相同的条件下,随矿浆浓度的增加,粒径在2Ixm以下的微粒所占比例逐渐增加,而后趋于平缓;当矿浆浓度从50%增至60%时,2m以下微粒由58.7%增至63.9%,此时,随矿浆浓度的增加,矿粉与研磨介质之间的碰撞次数增加,剪切和挤压作用;当矿浆浓度继续增至65%时,小于2m的微粒缓慢增至64.6%,这是由于矿浆浓度升高引起矿浆黏度增加,流动速度变慢,研磨介质的冲击作用减弱的缘故,这与文献[11]中自云石在超细研磨时流变性的变化是相同的,即矿浆浓度达到65%~75%时,浆体黏度将有明显,分散操作比较困难,不利于研磨的进行。考虑到矿浆浓度的变化对2t.zm以下微粒所占比例影响较小,因此,选择矿浆浓度为60%进行下一步实验。
2.1.4研磨介质与白云石质量比对微粒粒径的影响
研磨过程中,以球料作为研磨介质对物料进行冲击、摩擦、剪切等作用,使得物料终被粉碎至合适的粒度。球料的质量比决定研磨过程中物料能否与研磨介质进行有效接触,进而影响研磨能耗和研磨效率。实验结果如图4所示。
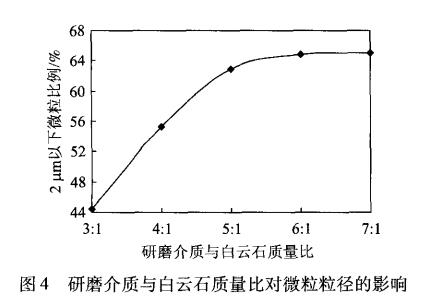
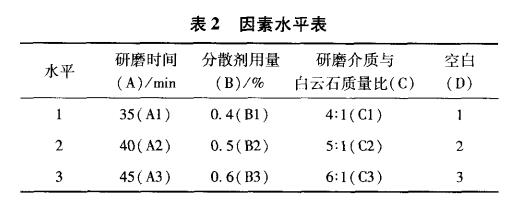
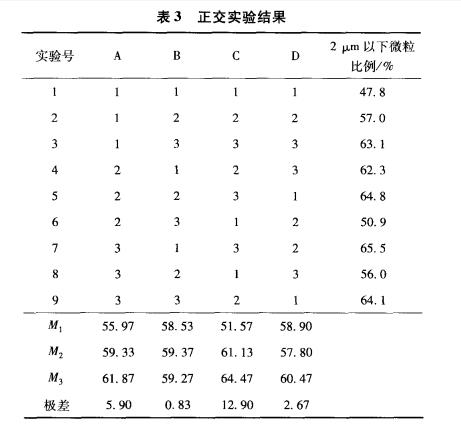
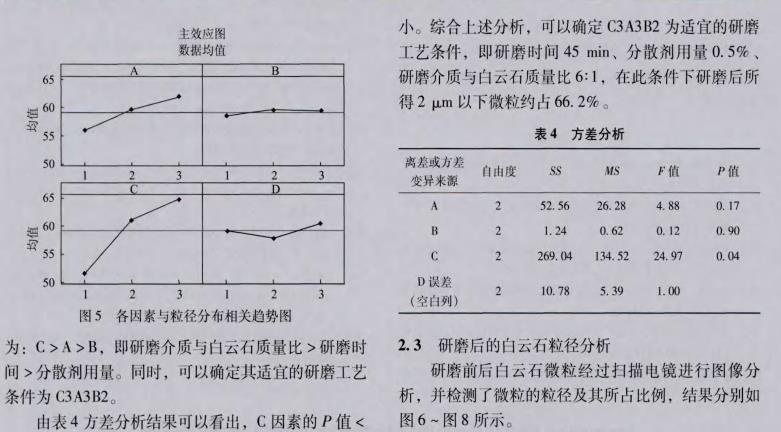
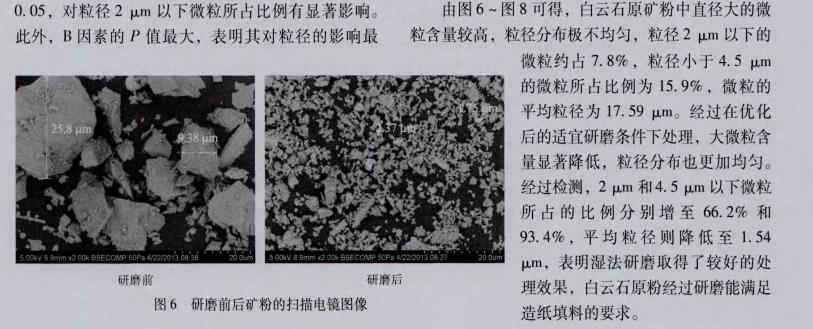
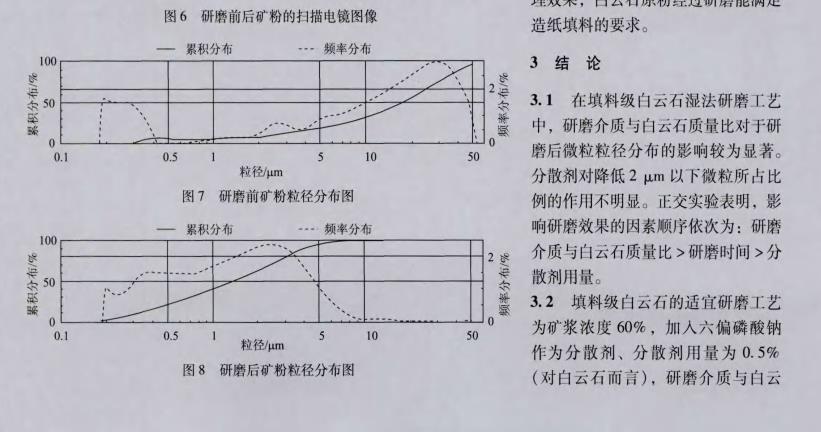
石质量比为6:l,在转速为3000r/mim下研磨45rain后,粒径小于2Ixm的微粒所占比例约为66.2%;研磨后白云石平均粒径变小,分布更均匀,满足了造纸填料的要求。
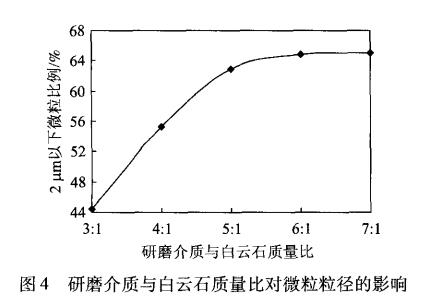
由图4可以看出,粒径小于2m的微粒比例随
研磨介质与白云石质量比的增加而快速;质量比为3:1时,微粒粒径在2m以下所占比例比较,为44.4%,表明转子的不能有效地作用于白云石微粒上,造成“空研”现象严重¨;随研磨介质与白云石质量比的升高,能够有效转化的逐渐增加,2m以下微粒所占比例不断,在4:1、5:1和6:1时分另0达到55.3%、62.9%和64-.8%;当研磨介质与白云石质量比为7:1时,白云石微粒粒径的变化与6:1时的情况差异不大,并考虑当矿浆浓度和黏度一定时,过高密度的研磨介质在重力和离心力的共同作用下,容易造成研磨介质磨耗、粉碎降等问题_】引,因此,选择研磨介质与白云石质量比为4:1、5:1、6:1进行正交实验。
2.2正交实验的结果分析
为了探讨各因素对研磨效果的影响程度,确定适宜的研磨工艺条件,将矿浆浓度固定为60%,分别以研磨时间、分散剂用量、研磨介质与白云石质量比为实验因素,进行3因素3水平的正交实验(L。(3),见表1和表2)。
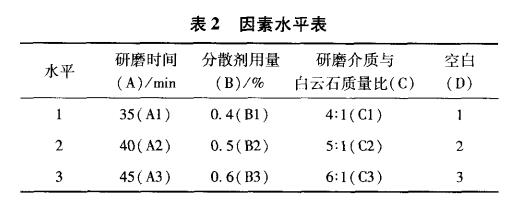
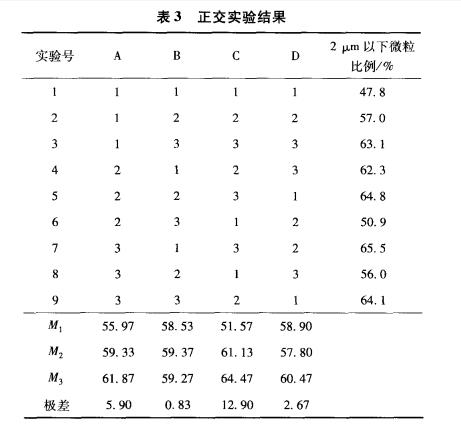
对表3和图5中的数据进行直观分析,以2Ixm 以下微粒所占比例为评价指标,各个因素主次顺序
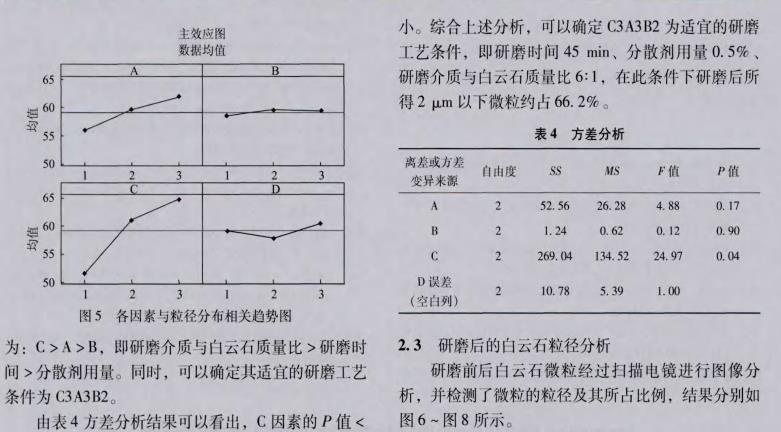
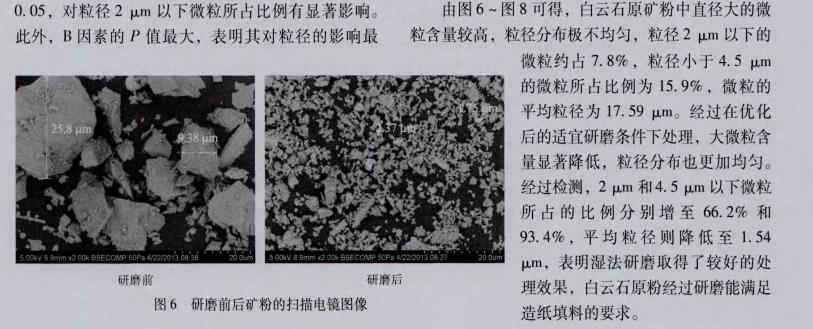
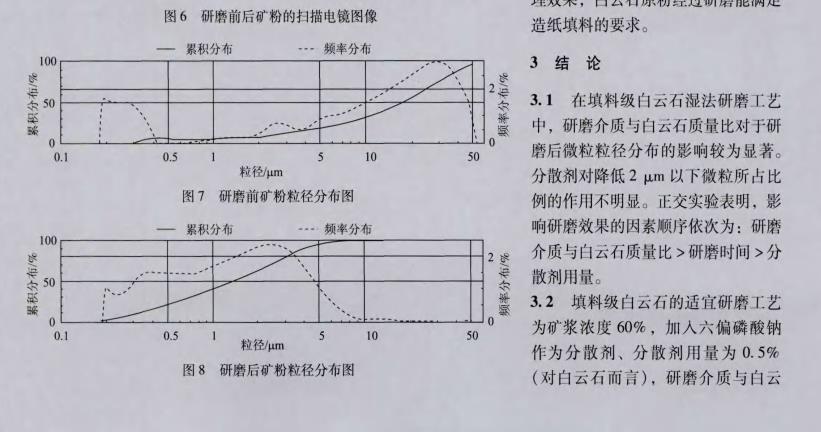
石质量比为6:l,在转速为3000r/mim下研磨45rain后,粒径小于2Ixm的微粒所占比例约为66.2%;研磨后白云石平均粒径变小,分布更均匀,满足了造纸填料的要求。